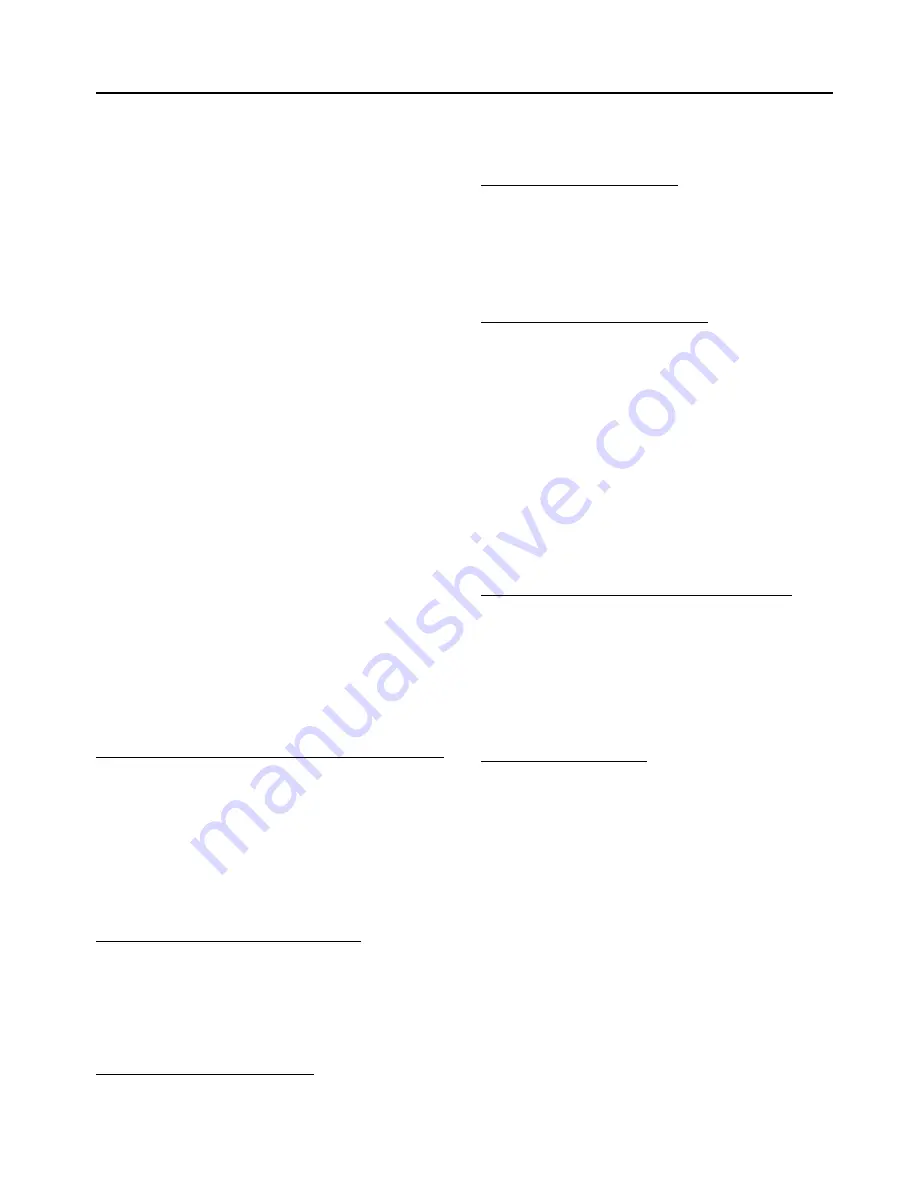
MASTERTRACE
Chapter 7 Networking Modules
7.1
7 Networking Modules
7.1 RS-485 Communications in Modbus RTU
The Master
Trace™
System uses RS-485 for all serial
communications. RS-485 provides for one master
(MR100 Group or Computer Interface) and several slaves
(Control Modules) on one data highway. The
Master
Trace™
Control Modules expand this limitation by
the use of two serial ports. This allows a Control Module
to connect to two different data highways and therefore to
two masters. The Central Computer Interface has one port
per data highway, allowing communication to an
unlimited number of Control Modules. Refer to the
Master
Trace™
MC100 Operator’s Manual.
Figure 7.1
indicates how the Control Modules and Interface Modules
can be networked.
7.2 RS-485 Wiring
Beldon cable 9841 or equivalent is recommended for the
RS-485 connection. It is a 2-wire, shielded, twisted pair.
From the serial port of the Interface Module, the cable is
connected to a serial port on each Control Module in
daisy-chain fashion. The total length of this daisy-chain
should not exceed 4,000 feet. A repeater can be used to
exceed this length or to create a “T” connection. The last
Control Module on the daisy-chain must be terminated.
Set the RS485-120 Jumpers to the IN position to terminate
the serial port. The RS-485 communications circuitry is
opto-isolated from the control circuitry. Do not externally
ground the shield. Refer to the figure for the appropriate
Module.
7.3 Removing a Control Module from the
Network
7.3.1 Remove from the Module List/Communication map:
From the MR100 Group Interface on the data highway,
access the MODULE LIST function (msg. S3-02), find
the Module Number to be removed and change the select
setting to NO.
From the Central Computer or MR100 for Windows CE
Group Interface on the data highway, access the
Communication Map, find the Module Number to be
removed and clear the check-box.
7.3.2 Disconnect from the Data Highway: Remove the
RS-485 cable from the serial port of the Control Module.
If the Control Module was at the end of the data highway,
change the RS485-120 jumpers setting on the new
end-of-line Control Module to the IN position.
7.4 Adding a Control Module to the Network
7.4.1 Connect to the Data Highway: Connect the Control
Module to the existing data highway by daisy-chaining
RS-485 cable to the serial port. Note that only the last
Control Module on the data highway should have its
RS485-120 jumpers set to IN.
7.4.2 Check the Module Number: Check the Programming
Sheet for Control Panel or Modules that came with the
new Control Module for the Module Number. It must be a
unique number for the data highways to which the Control
Module connects. If the Module Number is unique then
proceed to Enabling the Module. Otherwise, change the
Module Number as follows.
7.4.3 Change the Module Number: Choose a unique
Module Number for the Control Module. From the
MR100 Group Interface, use the SET MODULE
NUMBER function (msg. S3-20) to give the Control
Module a new, unique number. Note that the new Control
Module, and no other, must be in the Address Enable
Mode. The Address Enable light is on when the Control
Module is in Address Enable Mode. Refer to
Chapter
5.1.2.
For the Central Computer or MR100 for Windows CE
Group Interface, tap into the Module Commissioning
/Addressing Function Page and use the Set Module
Number option to give the Control Module a new, unique
number.
7.4.4 Add to the Module List/Communication map: From
the MR100 Group Interface, access the MODULE LIST
function (msg. S3-02), find the Module Number of the
Control Module to be added and change the select setting
to YES.
From the Central Computer or MR100 for Windows CE
Group Interface, access the Communication Map, find the
Module Number to be added and check the check-box.
7.4.5 Program the Module: Set the HEATER ENABLE
setting to YES for each circuit that is used on the Control
Module, and then enter the setpoints and configuration as
required.
7.5 Communication with Third Party Equipment
As indicated in
Figure 7.1
, any third party equipment,
such as PLC or automation system, can join Master
Trace
communication network through its Modbus RTU
supported RS485 serial port/link and acts as a master to
gather data from MasterTrace
™
control modules. The
popular PLCs such as Micro820 from Allen-Bradley and
M221 from Modicon have been proved to be successful
masters. For a third party equipment to act as a master in
Master
Trace
communication network, Master
Trace
Modbus registers must be programmed into the equipment.
The MasterTrace Modbus Communication Protocol,
which details the Modbus registers map and data
structures in MasterTrace Modbus communication, is
Содержание MASTERTRACE
Страница 1: ...MASTERTRACE TM OPERATOR S MANUAL HEAT TRACING CONTROL ...
Страница 51: ...MASTERTRACE 5 15 Chapter 5 Operation Figure 5 13 MR100 for Windows CE Group Interface Module RearView ...
Страница 54: ...MASTERTRACE Chapter 7 Networking Modules 7 2 Figure 7 1 MASTERTRACE System Network ...
Страница 87: ...D 2 MASTERTRACE Appendix D Typical Wiring Diagrams MS 2DXH0 MS 2DIN2 MS 5ADXH0 ...
Страница 88: ...MASTERTRACE D 3 Appendix D Typical Wiring Diagrams MS 5ADIN2 MS 5ATXH0 ...
Страница 89: ...D 4 MASTERTRACE Appendix D Typical Wiring Diagrams MS 10ADIN2 MS 10ADXH0 ...
Страница 90: ...MASTERTRACE D 5 Appendix D Typical Wiring Diagrams MS 10ADIN2X MS 10ADIN2T ...
Страница 91: ...D 6 MASTERTRACE Appendix D Typical Wiring Diagrams Driving Contactors Serial Communication 1 ...
Страница 92: ...MASTERTRACE D 7 Appendix D Typical Wiring Diagrams Serial Communication 2 ...