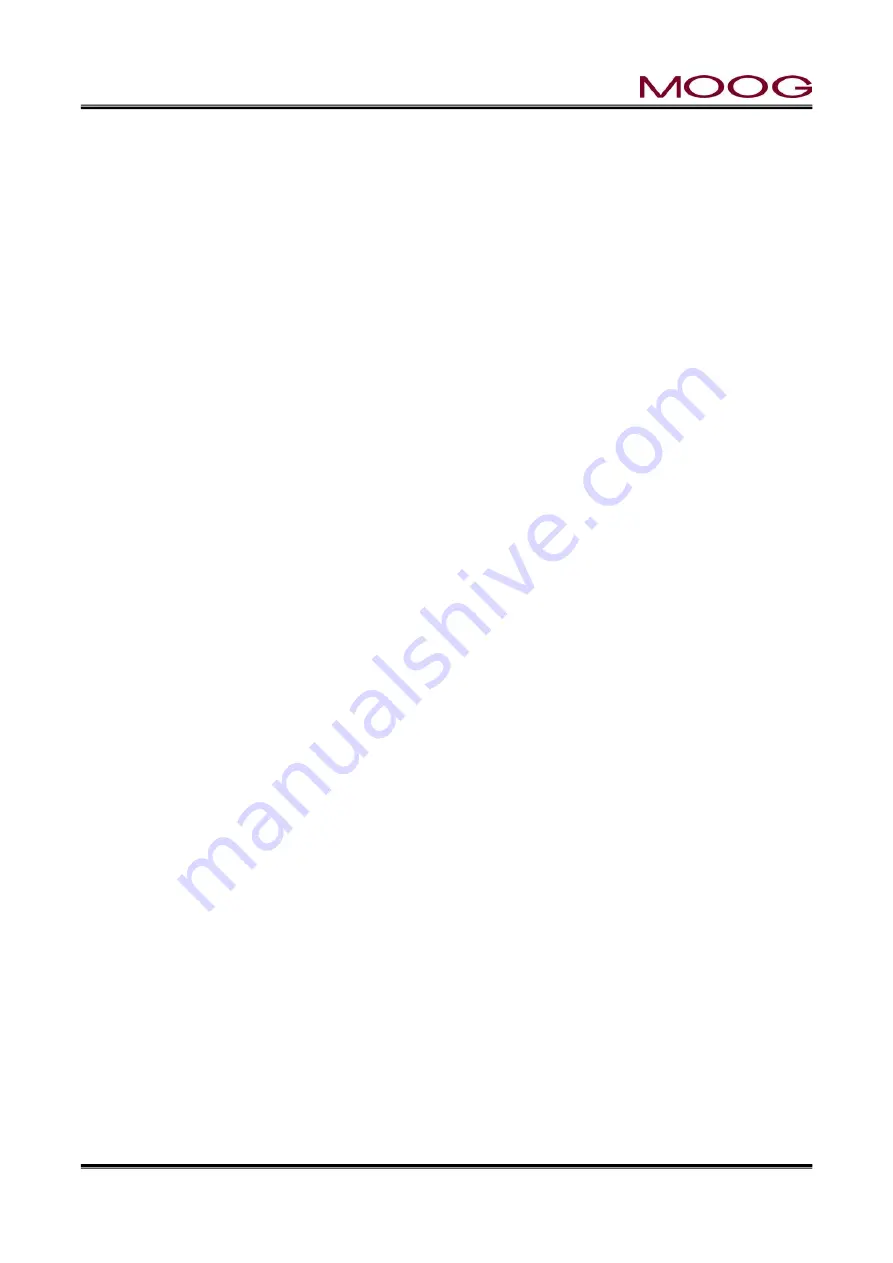
© MOOG 2019
This document is subject to MOOG INTELLECTUAL AND PROPRIETARY INFORMATION LEGEND . The details are on page II.
80
MRJ06301
2-7-4. INITIAL TRIALS
After the heater bands have brought the extruder barrel and extrusion head to the desired temperature,
some trial containers are blown. The blow molding machine timing and motions are adjusted to obtain a
sealed container. Adjustments to the constant die gap program,
Shot Size, Die Gap
and
Delay
may have
to be made before a sealed container is obtained. At this time, the die gap tooling opening is fixed and the
operator would follow the same logic he would use if the tooling was mechanically fixed in position to
obtain a sealed container.
Once a sealed container is obtained, it should be sliced open along the axis parallel to the parison length.
If the containers plastic material is translucent, then thick and thin areas can be found by visual observation
In any case, container wall thickness measurements should be made along the cut edge and compared
with the target wall thickness. The wall thickness or die gap opening program is then changed based upon
the differences with the target thickness.
More containers are then blown, cut open and the die gap opening changed as required. After two or three
trials it would be helpful to know the location of the programmed portion of the parison in the mold.
One method is to reduce the programmed thickness at one point and determine where that reduced wall
thickness ring is located in the container wall. Often, the reduced thickness point can be clearly seen.
Further trials with a single reduced thickness point at different locations along the container will help to
determine the position of the programmed points along the length of the actual container.
Do not run tests with more than one reduced thickness point. Reducing the wall thickness at a point will
change the distribution of plastic along the parison length and the use of more than one reduced thickness
point will lead to improper assessment of the results.
A second method to determine the program point distribution on the container is to mark the parison wall
at or as near as possible to the place where the parison leaves the die gap tooling. The marks may be
applied manually or it may be possible to use marker pulses to operate an ink jet. This method marks the
program points on the parison without distorting the parison or container.
When program points 1 and 200 are marked, the position of the programmed portion of the parison in the
mold may be determined and adjusted.
A constant thickness container wall will be probably obtained before the correct weight. Adjustment of
Weight, Range H or Range L will then allow both the correct container weight and wall thickness to be
obtained with minimum requirement for the operator to change the value of any individual programmed
die gap opening points.
++