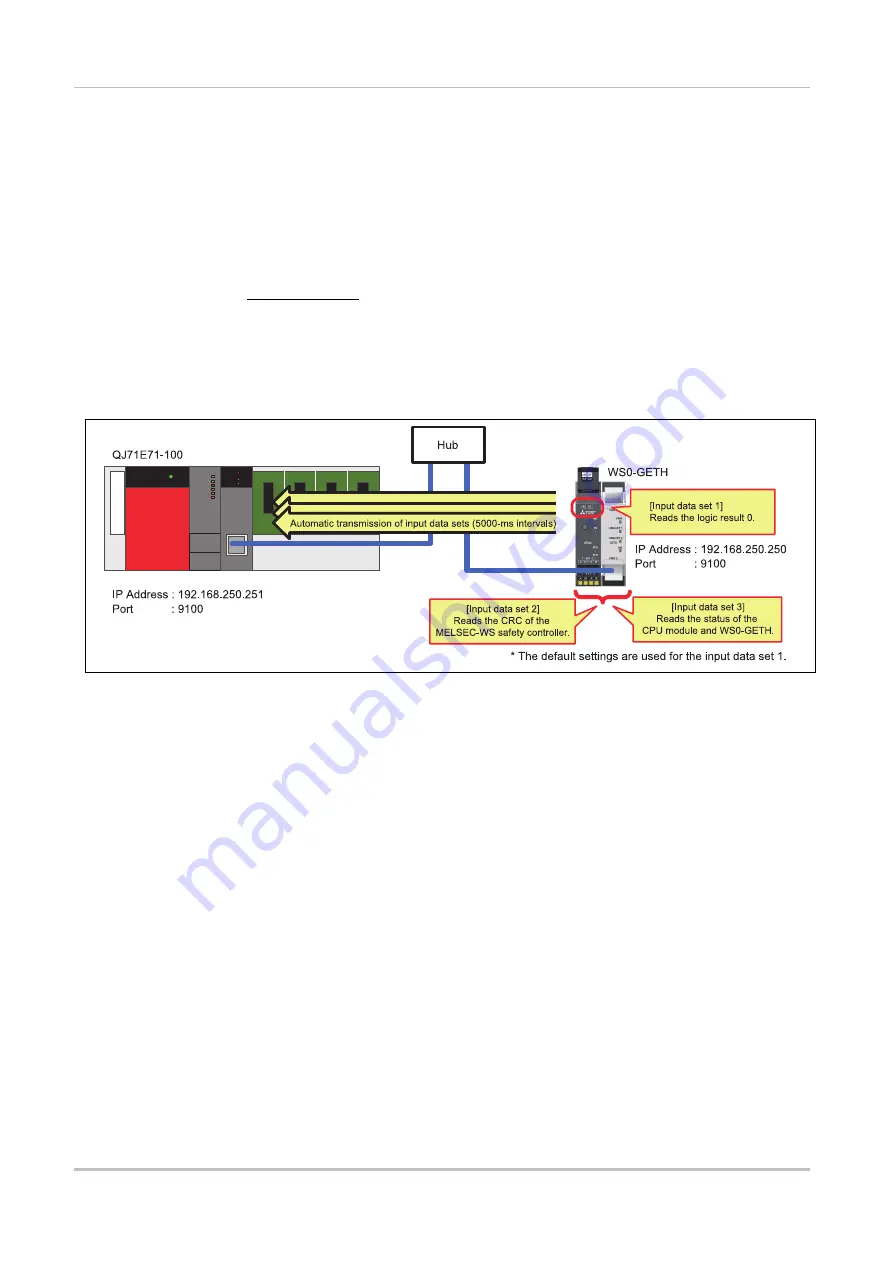
Procedures before operation
MELSEC-WS
98
8.2.4
Auto update mode
This section describes an example of communications in auto update mode.
The QCPU reads MELSEC-WS safety controller information (e.g. logic result, CRC,
and each module status) from the safety controller through communications
between the WS0-GETH and the QJ71E71-100. The WS0-GETH automatically
sends input data sets to the QJ71E71-100 at 5000-ms intervals.
Read-target data
Logic result 0 (input data set 1)
CRC (input data set 2)
Each module status (input data set 3)
Figure 56: System configuration example
(1) Parameter configuration
(a) Configuration required for the WS0-GETH
Configuration examples of network parameters required for communications in
auto update mode are shown below. Configure these parameters using Setting
and Monitoring Tool.
The WS0-GETH requires no program for communications.
1) Creating a hardware configuration
Refer to Section 8.2.2 (1).
2) Assigning an IP address
Refer to Section 8.2.2 (1).
Содержание Melsec WS Series
Страница 1: ...Safety Controller Ethernet Interface Module User s Manual WS0 GETH ...
Страница 2: ......
Страница 89: ...Procedures before operation MELSEC WS 86 ...
Страница 90: ...MELSEC WS Procedures before operation 87 ...
Страница 91: ...Procedures before operation MELSEC WS 88 ...
Страница 97: ...Procedures before operation MELSEC WS 94 ...
Страница 98: ...MELSEC WS Procedures before operation 95 ...
Страница 99: ...Procedures before operation MELSEC WS 96 ...
Страница 108: ...MELSEC WS Procedures before operation 105 Sample program auto update mode Figure 62 Sample program auto update mode ...
Страница 141: ......