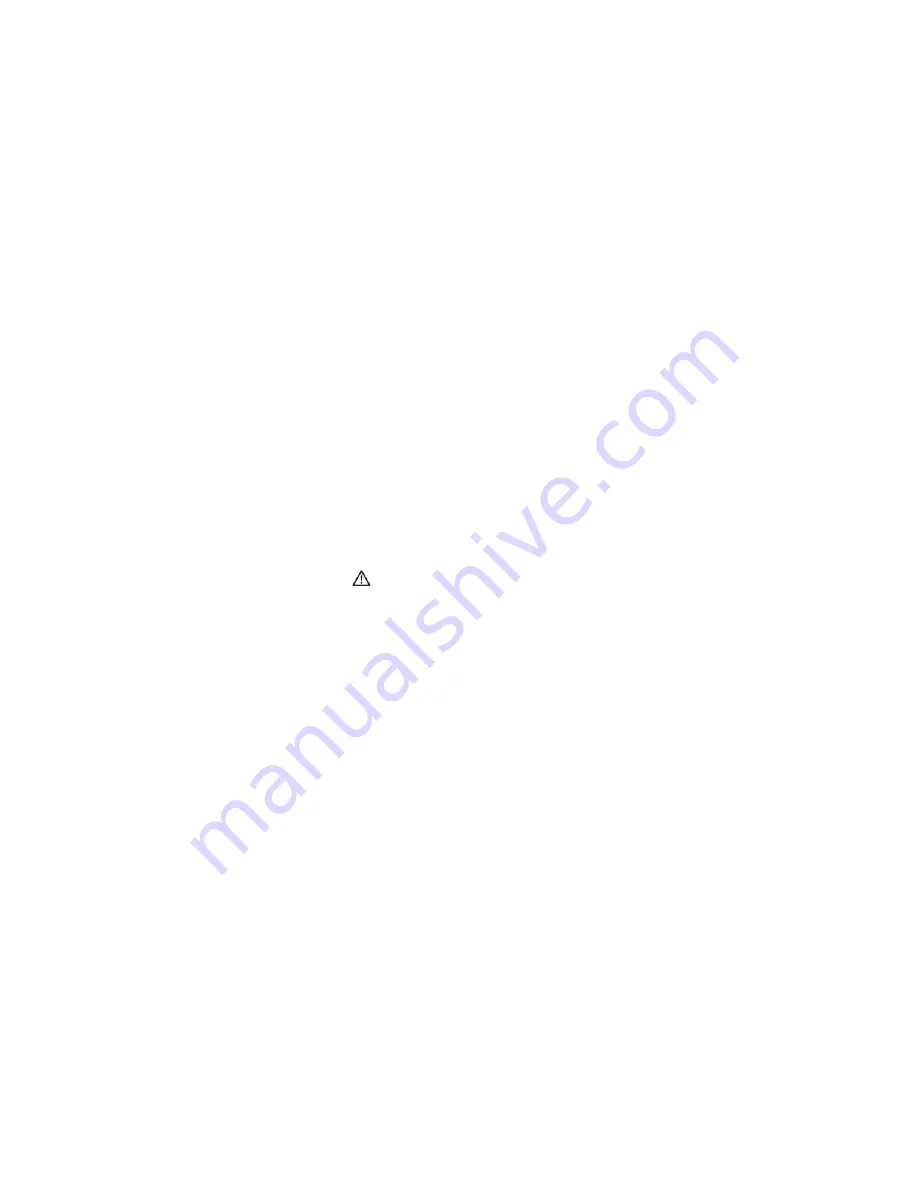
MHS Boilers Ltd ©
191007
37
Setting the required flow temperature for central heating system operation.
Attention! This setting is not active if a KKM6/8, E6/8 or BME/BM8, or an external 0-5 V signal is
connected.
- Open the lid of the KM 628, and a black arrow will appear above P1.
- Press the reset/programming button (item 3); the red LED will light up, then turn the rotary
selection switch until the desired temperature appears in the display.
- Again press the reset/programming button: the red LED will go out
- The new flow temperature will now be active
- Close the lid.
Set the required hot water temperature for hot water operation.
This is only applicable if the hot water mode is being used.
- Open the lid
- Turn the rotary switch until the arrow at the bottom of the LED displays parameter P2
- Press the reset/programming button (item 3), the LED lights up, then turn the rotary switch
(item 5) until the desired hot water temperature appears in the display
- Again press the reset/programming button; the LED will go out
- The new value will now be active
- Close the lid
6.4 Fault signals
In the case of the fault, a flashing
and an error code will constantly appear in the display. In the
case of a fault, the cause should first be eliminated before the relevant safeguard is reset. The OK
signal will be lost if a fault occurs more than twice within 6 minutes (the error code will be shown
in the display with a “3” appearing above it), or in the case of a fault that remains active for more
than 6 minutes.
1 High Limit thermostat (STB) has been triggered
If the flow temperature has risen above 100
°
C the high limit will be activated.
Wait until the flow temperature is below the value set for at least one minute and then reset this
safety function by pressing the reset button.
2/3 Interlock circuit has been interrupted
An external safety device connected to the terminals (ST 9.3-9.4) has been triggered. Check and
repair this safety device.
4 No flame signal when the burner starts
No flame is detected within the preset safety time when burner starts. Restart is possible if
programmed.
5 Flame signal lost during operation
When the burner is in operation, the measured ionisation has fallen below 1
µ
A.
Содержание Ultramax WM 100
Страница 46: ...MHS Boilers Ltd 191007 46 ...
Страница 47: ...MHS Boilers Ltd 191007 47 ...
Страница 48: ...MHS Boilers Ltd 191007 48 ...
Страница 49: ...MHS Boilers Ltd 191007 49 ...
Страница 50: ...MHS Boilers Ltd 191007 50 Notes ...