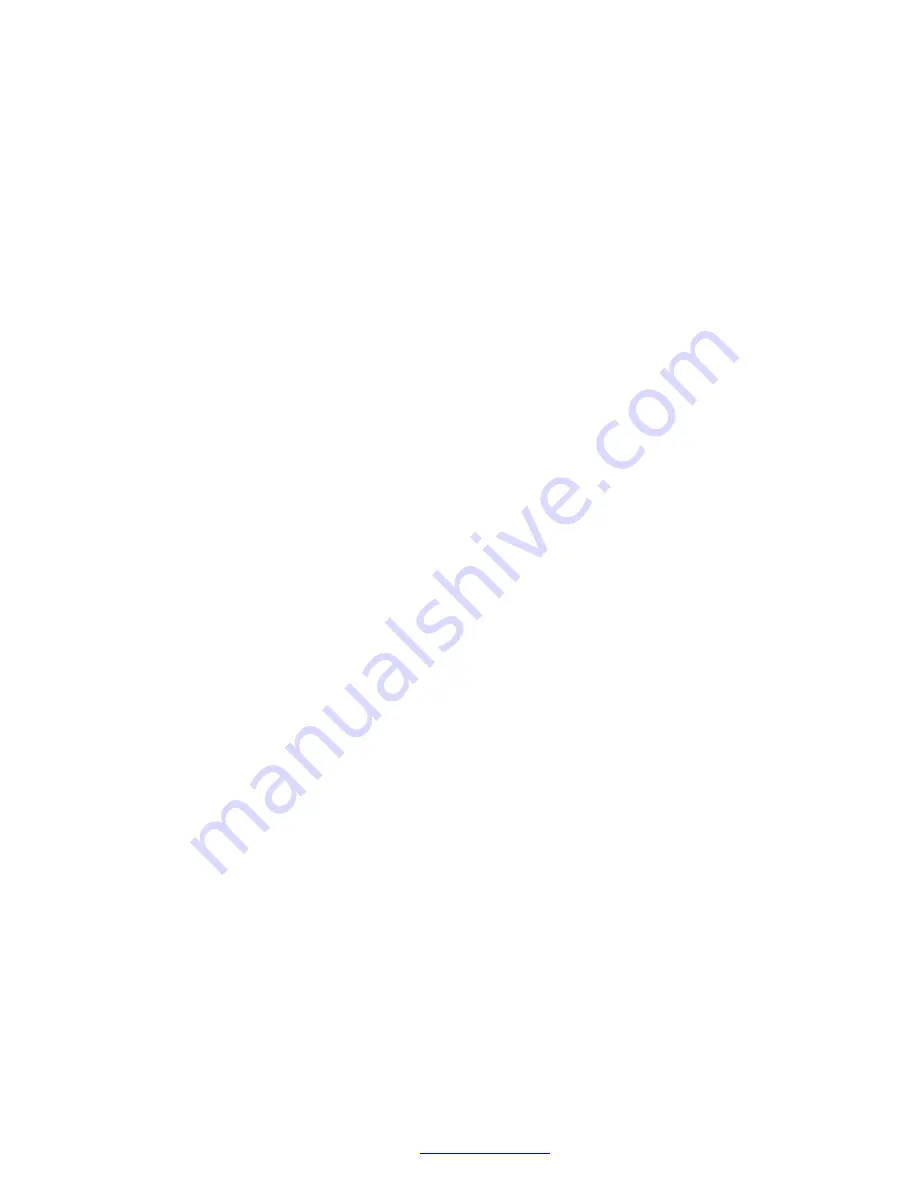
© MHG Heating Ltd
MHG Heating Ltd, Unit 4 Epsom Downs Metro Centre, Waterfield, Tadworth, Surrey, KT20 5LR
P:0845 6448802 F:0845 6448803 E:
W: www.mhgheating.co.uk
010617
65
KIND, MUST NOT BE USED TO CLEAN THE BURNER SURFACE. If damage has occurred to
the burner lance surface or the mounting gasket either item MUST be replaced.
m)
To ensure that the rectification circuit operates correctly the resistance between the
burner and burner door must be check with a multi-meter to ensure that it is less than
1 Ohm (<1 Ohm.)
n)
Clean with abrasive material and inspect the ignition electrode. Replace if necessary.
Adjust the spark gap to 4mm.
o)
Check the combustion fan blades for debris build-up. Remove any debris with a soft
bristle brush or preferably compressed air. DO NOT TOUCH, OR SPIN, THE FAN BLADES
WITH YOUR FINGERS AS THIS COULD AFFECT THE BALANCING OF THE FAN BLADES.
p)
Re-fit the Burners, in the reverse order of dismantling, ensure that all electrical
connections are correctly and securely connected.
q)
Inspect all water joints. Any joints found to be leaking MUST be replaced. It is also
advisable when replacing water joints to also change any adjacent joints at the same
time.
r)
Inspect all gas joints with a suitable leak detection method. Any joints found to be
leaking MUST be replaced. It is also advisable when replacing gas joints to also change
any adjacent joints at the same time.
s)
Via the tappings on the boiler connector elbow or straight a flue gas recirculation check
must be undertaken when the boiler is operating on high and low fire modes.
t)
Inspect and clean the condensate neutralising tank, replenishing the neutralising
granules as required. Granules available from MHGHeating Ltd Spares Department.
u)
With the use of a suitable Flue Gas Analyser, check and adjust the combustion settings,
as detailed in Section 15.2.
v)
Inspect the general condition of the flue system, including the termination, repair as
necessary or advise on any remedial action as required.
w)
Following the satisfactory completion of the above service procedure, the internal
Routine Service Control Timer needs to be reset. Utilising the QAA73 Room Unit/Service
Tool gain access to the Second Level Parameters, as detailed in Section 14.2, and select
Parameter Line H630 – Bit 6. using the + button, adjust the value from 0 to 1 and press
the INFO button to reset the Service Interval counter.