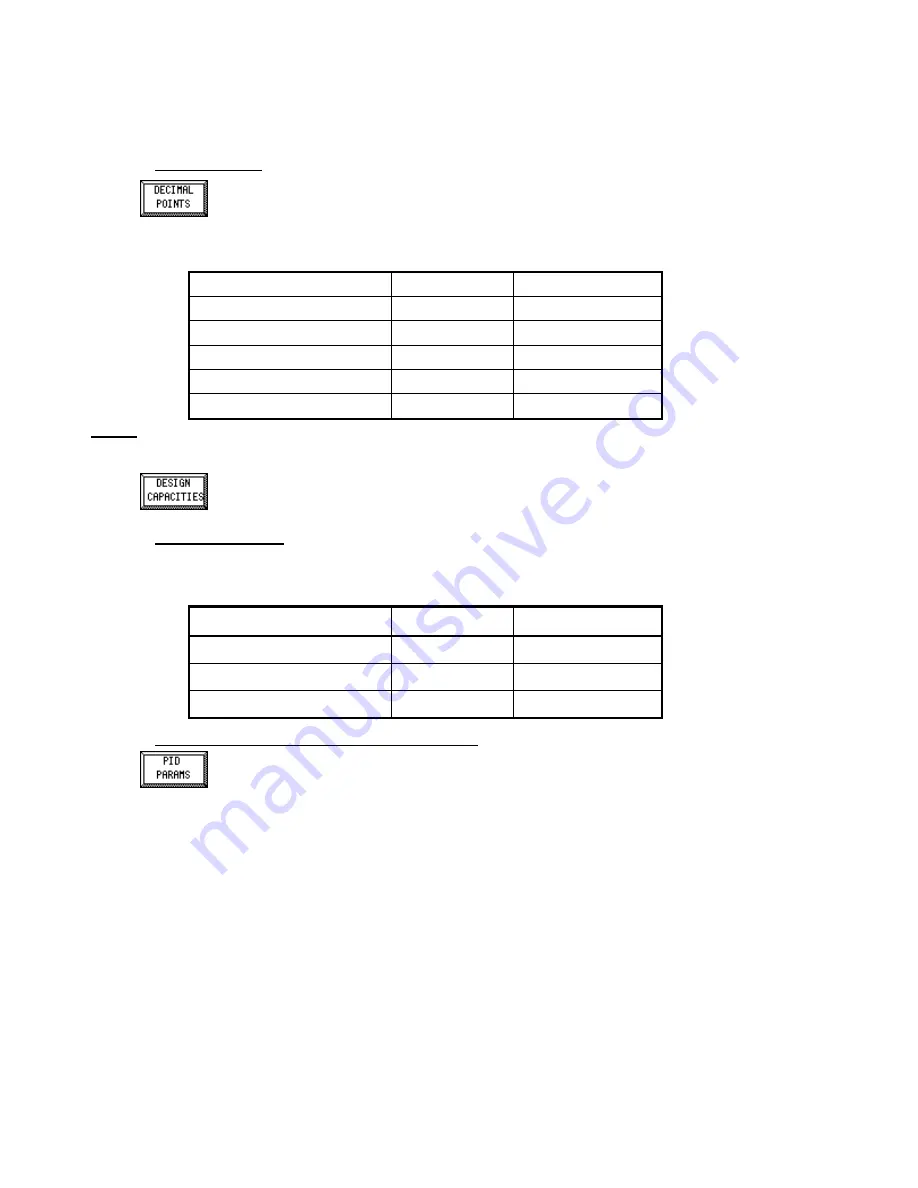
MC³ 24.96.EX O&M Manual
Page 25
08/14/01 4:34 PM/LDD
points are necessary, you should at least look at each decimal point option to insure the proper
display of values.
Decimal Points
Internally the MC³ Controller uses floating point numbers. Any changes to the decimal
point settings affects
only the display
of the values which will be rounded appropriately.
To enter the Decimal Points Menu, press the Decimal Points button while in the first
Setup Screen menu. The display will be a Numeric Entry Screen. Use the directions on page 9 to
change the value of the parameter.
Parameter
Min
Max
Belt Load
0
4
Total
0
4
Belt Speed
0
4
Belt Length
0
4
Feedrate
0
4
NOTE:
Please note that the maximum number of decimal places is four.
Design Capacities
To enter the Design Capacities Menu, press the button from the first Setup Screen menu. The
display will be a Numeric Entry Screen. Use the directions on page 9 to change the value of the
parameter.
Parameter
Min
Max
Design Load
1
30000
Design Feedrate
0.01
30000
Design Speed
0.5
30000
PID Parameters & Output Dynamic Protection
The MC³ Controller, when in control mode, uses a PID (Proportional (Gain), Integral,
Derivative) control algorithm. To tune this algorithm to a particular feeder, changes can
be made to these parameters.
When the MC³ is in control, it is the MC³’s job to maintain a feedrate setpoint. This is done by
controlling the belt speed to a point where the difference between the setpoint and the actual
feedrate is minimal. In the MC³, error is defined as (error) = (actual feedrate) - (setpoint). The PID
algorithm uses this error term to adjust the speed of the feeder belt. For example: If the error is
slightly positive (the actual feedrate is larger than the setpoint), the MC³ will slow down the belt
speed.
The advantage of a PID algorithm is that it is an industry standard and many books and articles
have been written on how to tune a PID controller. Several of these methods require little
knowledge about the actual dynamics of the system to be tuned. If possible, Merrick will tune the
PID controller before the feeder is shipped to you. Otherwise, we recommend you use whatever
tuning method you are most familiar with.
To enter the PID Parameters, press the button from the first Setup Screen menu The display will
be a Numeric Entry Screen. Use the directions on page 9 to change the value of the parameter.