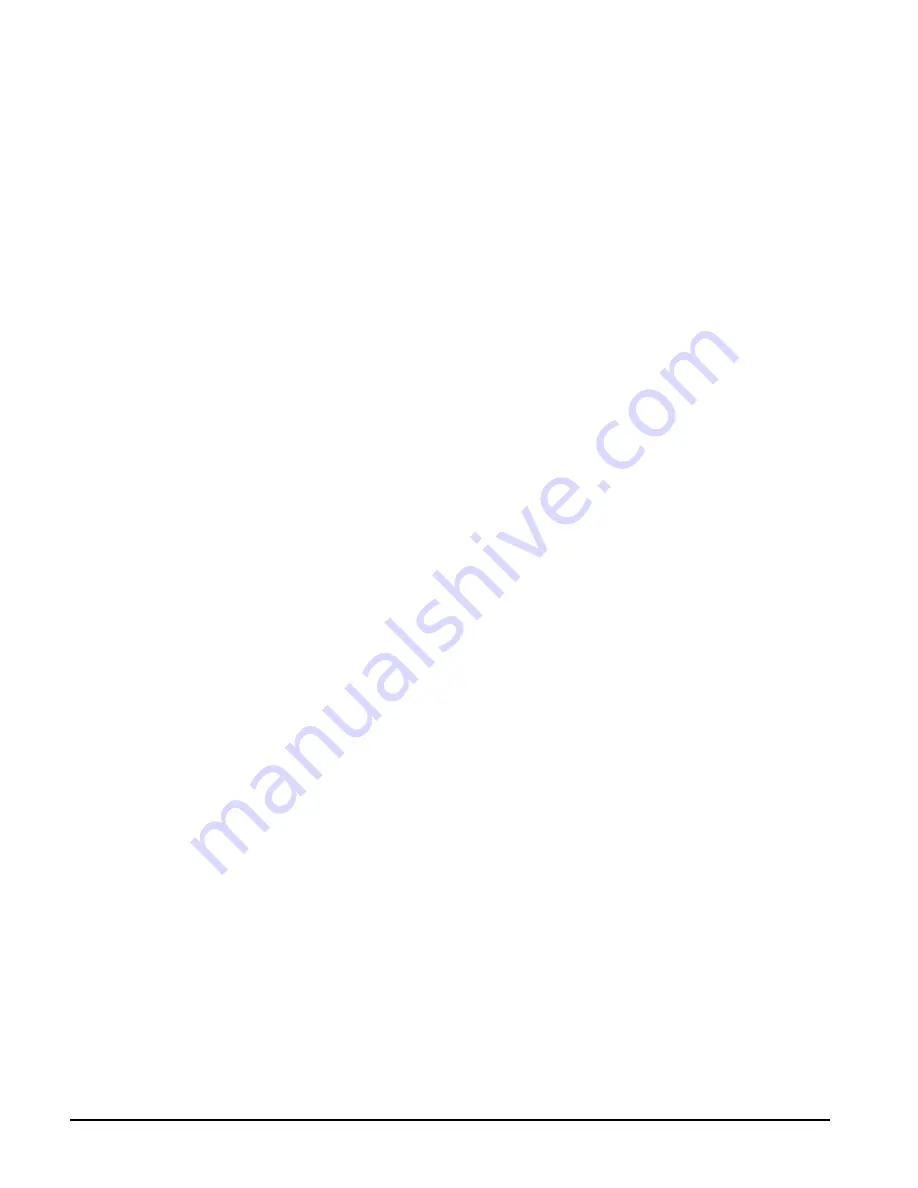
76
AGR 070A through 100A
IOMM AGR-1
Press the Next Item key. The display will show the current Day, Hour, Minute and Second. If this
information needs to be changed, follow the same procedure used to set the Date in the previous
section.
Menu #20
: Daily Schedule—This section will help you to set the Daily Start/Stop time for automatic
operation of the chiller. Pressing the Next Menu key and the Next item key will advance the display to
the Daily Time Schedule. This is where the Start and Stop times for each day of the week will be set
using the 24 hour format. Beginning with Sunday, use the Incr and Decr keys to set the desired start
and stop time and press the Enter key to store the information in the controller. If the chiller is to be
programmed to run continuously 24 hours a day, set the stop tie for 1 minute before start time
(Stop=23:59; Start=00:00). Press the Next Item key to advance through the remaining week days and
Holiday Start/ Stop times.
Menu #21:
Holiday Date—Up to 14 holiday dates may be entered. When the MicroTech controller's
current date matches a date set in the holiday schedule, the normal daily start/stop times are replaced
by the holiday start/stop ties which were set in the previous section. At the date prompt, use the Incr
and Decr keys to set the first holiday month and press Enter to advance to the Day position of the
display. Use the lncr, Decr and Enter keys to set the first day of the holiday. Press Next Item to
advance to Holiday 1 Duration. If the scheduled holiday spans more than one day, use the lncr and
Decr keys to set the holiday duration and press Enter to store the information in the controller. Use the
Next Item key to set additional holiday dates and duration’s for the entire year.
Menu#22:
Alarm Set Points—On a call for cooling or heating, the controller will open the liquid line
solenoid valve. When the evaporator pressure rises above the Low Pressure Cutin set point, the first
compressor will be started. The Low Pressure cut out set point determines the point at which the
compressors will shut off during a pumpdown sequence. The Refrigerant Freeze and Water Freeze
alarm set points may be adjusted as required. Water and refrigerant freeze alarm time delays may also
be adjusted for this menu. If the condenser High Pressure set point is exceeded, the controller will
shut off the unit.
Menu #23:
Miscellaneous Setup—Several general operating characteristics are defined here. These
are set at the factory prior to unit delivery and should not require adjustment. The control software
version number is displayed form this menu. Outdoor air temperature is displayed on Menu 12.
Alarm Menus
Menus 24 through 27 are used to display any alarm conditions that may be present in the unit. The
date and time when the alarm occurred accompany all alarm messages. Important operating
conditions at the time of the alarm are stored in the controller's memory and may be viewed within the
following alarm menus.
Menu #24:
Circuit #1 Current Alarm—If refrigerant circuit # 1 is in an alarm condition, the
appropriate alarm message will be displayed here. The temperature and pressure readings at the time
of the alarm will be stored in the controller's memory and may be displayed for analysis from this
menu.
Menu #25:
Circuit #2 Current Alarm—If refrigerant circuit #2 is in an alarm condition, the
appropriate alarm message will be displayed here. The temperature and pressure readings at the time
of the alarm will be stored in the controller's memory and may be displayed for analysis from this
menu.
Menu #26:
Circuit #1 Previous Alarm—The alarm type for the last recorded circuit #1 alarm may be
displayed from this menu. The time and date at which the previous alarm occurred are also displayed
here. This information will be replaced when a current alarm condition is cleared.
Menu #27:
Circuit #2 Previous Alarm—The alarm type for the last recorded circuit #2 alarm may be
displayed from this menu. The time and date at which the previous alarm occurred are also displayed
here. This information will be replaced when a current alarm condition is cleared.
Содержание AGR 070AS
Страница 20: ...20 AGR 070A through 100A IOMM AGR 1 Figure 9 Typical Field Wiring with Global UNT Controller...
Страница 21: ...IOMM AGR 1 AGR 070A through 100A 21 Figure 10 Typical Field Wiring Diagram with MicroTech Controller...
Страница 22: ...22 AGR 070A through 100A IOMM AGR 1 Figure 11 Standard Single Point Connection with FanTrol...
Страница 23: ...IOMM AGR 1 AGR 070A through 100A 23 Figure 12 Standard Single Point Connection with Optional SpeedTrol...
Страница 24: ...24 AGR 070A through 100A IOMM AGR 1 Figure 13 Unit Control Schematic 2 compressor UNT...
Страница 25: ...IOMM AGR 1 AGR 070A through 100A 25 Figure 14 Staging Schematic 2 compressor 4 stage UNT...
Страница 26: ...26 AGR 070A through 100A IOMM AGR 1 Figure 15 Staging Schematic 2 compressor 6 stage UNT...
Страница 27: ...IOMM AGR 1 AGR 070A through 100A 27 Figure 16 MicroTech Controller Schematic...
Страница 28: ...28 AGR 070A through 100A IOMM AGR 1 Figure 17 Unit Control Schematic MicroTech...
Страница 29: ...IOMM AGR 1 AGR 070A through 100A 29 Figure 18 Staging Schematic 4 stage MicroTech...
Страница 30: ...30 AGR 070A through 100A IOMM AGR 1 Figure 19 Staging Schematic 6 stage MicroTech...
Страница 31: ...IOMM AGR 1 AGR 070A through 100A 31 Figure 20 Unit Control Schematic 2 compressor MicroTech...
Страница 32: ...32 AGR 070A through 100A IOMM AGR 1 Figure 21 UNT Instrument Layout See legend on page 34...
Страница 33: ...IOMM AGR 1 AGR 070A through 100A 33 Figure 22 MicroTech Instrument Layout See legend on page 34...
Страница 35: ...IOMM AGR 1 AGR 070A through 100A 35 Figure 25 MicroTech Sensor Layout...
Страница 99: ...IOMM AGR 1 AGR 070A through 100A 99 Notes...
Страница 100: ...Post Office Box 2510 Staunton Virginia 24402 USA 800 432 1342 www mcquay com...