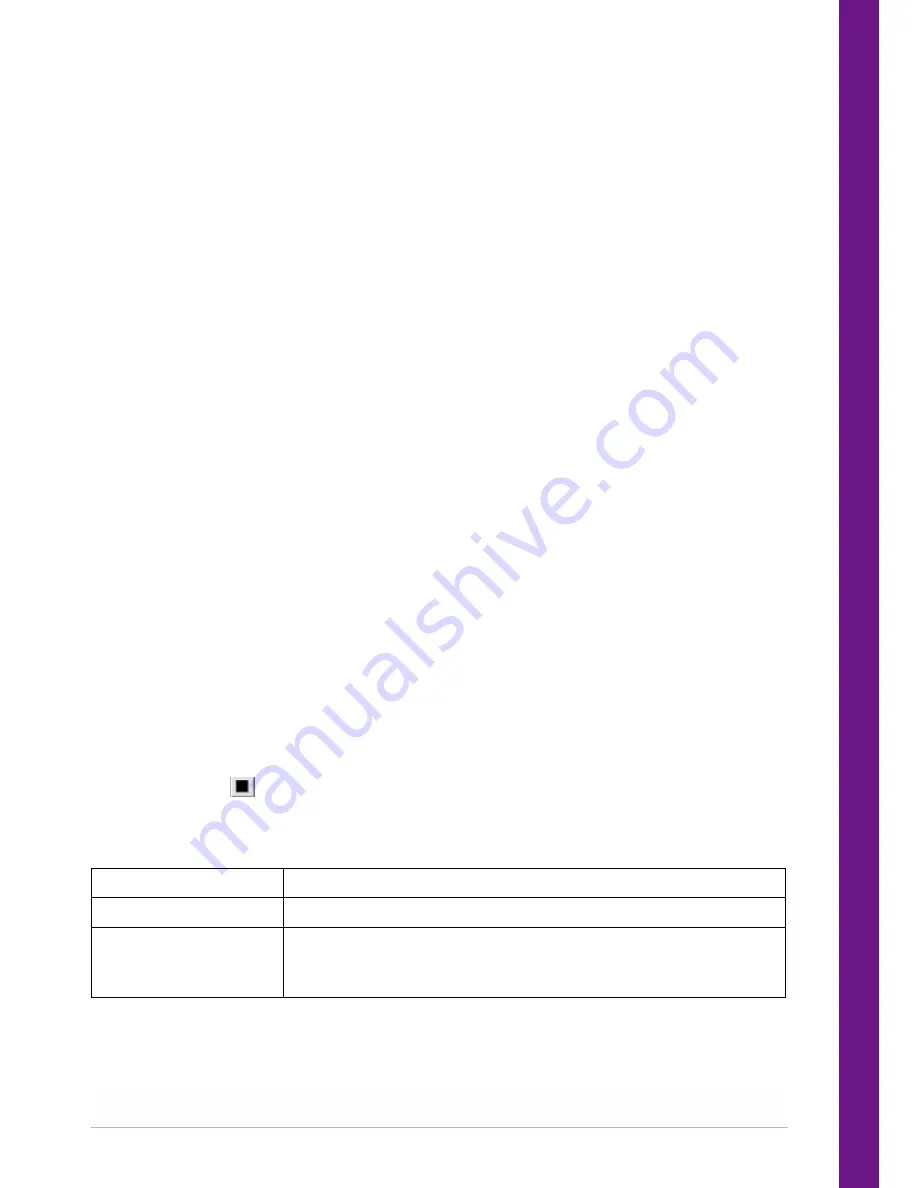
QUI-1057
Page 36
Markes International Ltd
T:
+44 (0)1443 230935
F:
+44 (0)1443 231531
E:
www.markes.com
Cycle Count
Displays the number of sequence cycles that have been completed.
3.5
UNITY 2 method options
3.5.1
Split on or off in standby
When UNITY 2 is in standby state, i.e. not being used overnight or at weekends, it is usual to have the split
turned off in order to save expensive carrier gas (8 hours overnight at 50 ml/min would use ~24 litres of
carrier gas).
However if UNITY 2 is being operated with a mass spectrometer (MS) or an electron capture detector
(ECD) on the gas chromatograph, it is strongly recommended that the split be left on in standby [if there is
no positive gas flow passing through the split vent for long periods of time, air will enter the system
through the split vent and cause an undesirable increase in background signal. This is common to all split
capillary injectors].
The split flow may be reduced to 10 ml/min to minimise carrier gas consumption if required.
Checking the box on the top line of the method page selects Split On in Standby. An unchecked box will
turn the Split Off in Standby.
3.5.2
The Leak Test
Once in position in the desorber flow path, each tube is pressure tested, without heat or carrier gas flow,
to ensure there are no leaks. The test is deliberately stringent. If sample tubes fail to seal properly or if a
leak develops in any other part of the system flow path, data obtained from that analysis would be invalid.
Every part of the UNITY 2 flow path, including the main valve, is tested for leaks during the pressure test
(the only exception is the point where the transfer line is connected to UNITY 2). For this reason, following
installation of the transfer line, it is recommended that a leak detector is used to detect any leaks at this
point in the flow path. Many competitive thermal desorption systems do not offer such a comprehensive
leak test. Without this, there is always risk of an undetected leak and data integrity cannot be guaranteed.
The 'no-heat, no-flow' specification ensures that sample integrity is maintained while the UNITY 2 leak test
is in progress. If the tube fails the leak test, it will not be analysed and UNITY 2 displays a Tube leaked
error message in the status box on the main status bar. The user must clear this message by pressing the
Stop sequence icon (
) on the tool bar, before proceeding.
3.5.3
Determining the prepurge time
The flow through the sample tube during the ambient temperature purge is controlled as follows:
Trap in line, split off
purge flow controlled via the needle valve on the desorb flow vent
Trap off line, split on
purge flow controlled via the needle valve on the split vent
Trap in line, split on
total purge flow = flow through cold trap (controlled via the needle valve
on the desorb flow vent) + flow through split vent (controlled by the needle
valve on the split vent)
The Prepurge time should be set such that, with the given purge flow, the necessary purge volume is
passed through the sample tube before the end of ambient purge and the beginning of tube heat. Typical