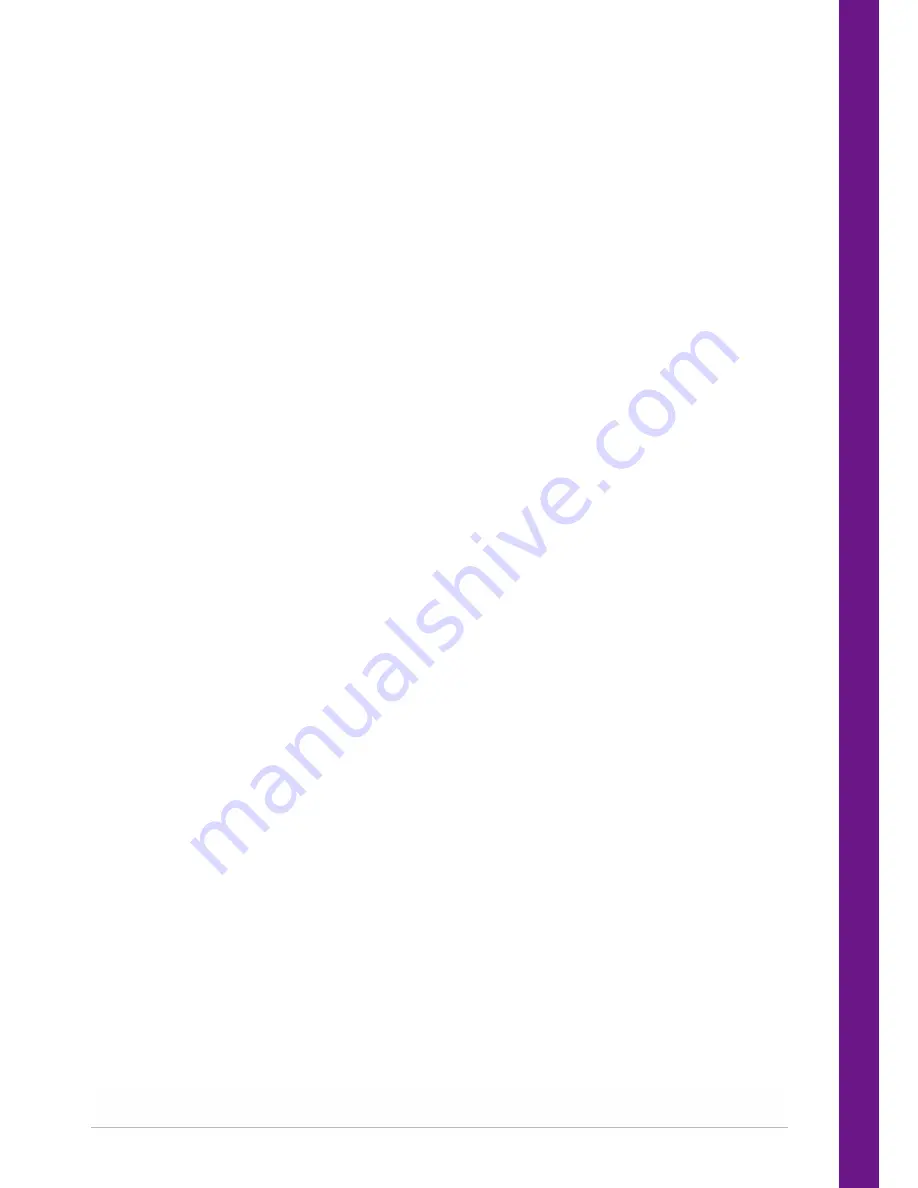
QUI-1057
Page 18
Markes International Ltd
T:
+44 (0)1443 230935
F:
+44 (0)1443 231531
E:
www.markes.com
2.3
Insertion and removal of a sample tube in UNITY 2
2.3.1
Insertion
Tubes are inserted using the left-hand lever mechanism. Orientate the tube such that the sampling
(grooved) end is pointing to the rear of the instrument. Before inserting a sample ensure that the tube
oven is relatively cool, note that the oven temperature is displayed on the UNITY 2 software status bar
(see section 3.2). Place the tube horizontally in the tube oven, such that it is clear of the seals at both
ends. Operate the lever towards the rear of the instrument to seal the tube into the UNITY 2 flow path.
The instrument is then ready to run.
2.3.2
Removal
As soon as a tube has been desorbed (i.e. after primary desorption) it can be removed from the desorption
oven. If the oven and tube are still hot (you can check this by looking at the software status bar, it is
strongly recommended that the tube extractor tool, included in the shipping kit, is used to remove the
tube. Use the tool to grasp the tube at the end released from the tube seal and pull steadily.
2.4
Desorb and split flows
2.4.1
Gas flow through the cold trap
The UNITY 2 cold trap operates in backflush mode - the sample gas stream enters and leaves the cold trap
through the narrow-bore/restricted end which points to the rear of the instrument. Backflush desorption
allows use of a series of 2 or 3 sorbents of increasing strength in the cold trap. This facilitates the
analysis of wide volatility range samples (High boiling compounds are retained by and quantitatively
desorbed from the first weak sorbent, without ever coming into contact with the stronger sorbents behind).
2.4.2
When should desorb/split flows be measured?
Whenever a needle valve adjustment knob has been moved (deliberately or accidentally).
Whenever the GC column has been changed.
Whenever the carrier gas pressure to UNITY 2 has been changed.
Measuring the flows is often done at the start of a sequence of analyses to confirm/ensure that no
system changes have taken place.