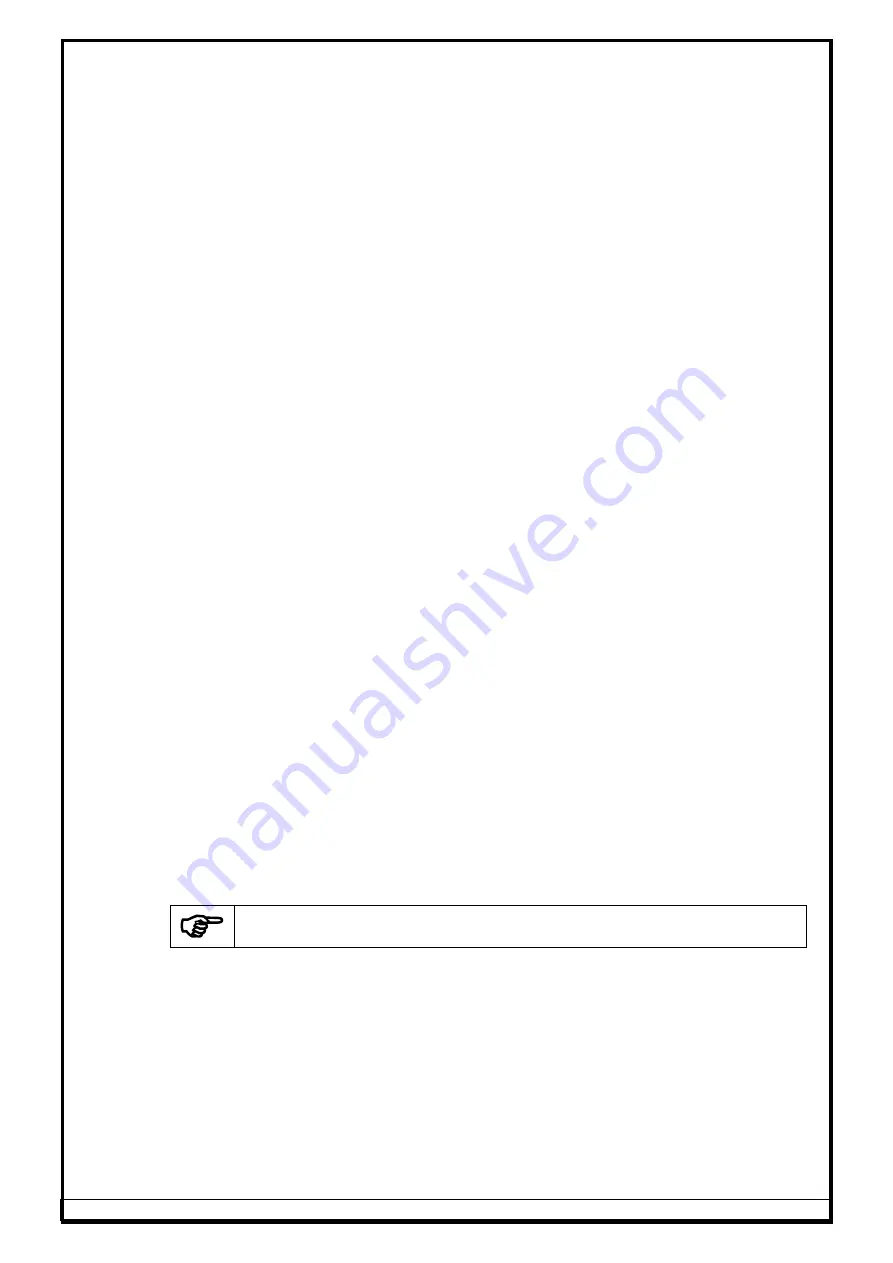
Ref.: 3DWA - SM Ver.1.8
88
3.
Replace the defective board with new MOV Board and re-fix it. Restore
all the connections.
4.
Power up the system. Check & ensure Input & Output voltage (230V AC)
at respective sections of EMI Filter board with the help of Multimeter.
5.
Ensure the Alignment program is running.
6.
Close the Safety and then Interface box top cover.
9.3.
VERTICAL COLUMN
(Applicable only for AVH model)
9.3.1.
POWER NUT
1.
Remove the Bellows and dismantle the Front cover.
2.
Move the Saddle plate to top most point.
3.
Remove the Mechanical stopper.
4.
Disconnect the Limit switch wirings and remove the Top plate.
5.
Unscrew the Power nut from Saddle plate and then remove the Saddle
plate.
6.
Replace the Power nut in the Saddle plate and restore it.
7.
Re-fix the Mechanical stopper by ensuring a gap of 5mm between the
bottom phase to Guide bush top phase.
8.
Fix the Top plate and then do the wirings again for Limit switch.
9.
Fix the Front cover & finally Bellows.
9.3.2.
BELT
1.
Remove the Motor cover.
2.
Loosen the Motor fixing bolt and remove the worn out belt from Motor
pulley.
3.
Replace the belt with new one
4.
Tighten the Motor fixing bolt.
5.
Ensure the tightness of belt.
9.4.
TARGET PLATE
1.
Fix the New Target plate with Calibration kit.
2.
Run the alignment program and go to Settings option. Provide the required
password (mas<space>algn) and select
Camera testing
.
3.
Ensure the Camera gain & intensity as explained in Chapter 8.1. Also ensure the
Target plates are displayed corrected.
4.
Perform
Calibration
as explained in Chapter 7.4.
5.
Then calibrate the respective Target plate as explained in Chapter 7.4.3.
6.
Ensure the equipment functions without any errors.
9.5.
PERSONAL COMPUTER
Alignment PC software & Calibration data are pre-loaded in the Desktop
computer if supplied by Manufacturer
Following procedures are to be done in case if the PC is arranged by Customer himself
or during re-installation:
1.
Disconnect all the connections from the PC and replace the defective PC with
new Computer and re-fasten it again.
2.
Restore all the connections.
3.
Install the Windows OS & Alignment PC software as explained in Chapter 6.1.
4.
Restore Factory calibration data from the Optical media provided by
Manufacturer or other external device to PC as explained in Chapter 7.7.8
respectively.
5.
Install International Vehicle data (Autodata) as explained in Chapter 6.2 & enable
the feature as explained in Chapter 7.7.10.1 (Lock details) of Operating manual.
NOTE : Refer scope of supply for availability of this feature
Содержание Fox 3D Smart Mobile PT
Страница 9: ...Ref 3DWA SM Ver 1 8 6 PIT DIMENSIONS Max Wheel base 3 2 4metre For VH model Fig 3...
Страница 16: ...Ref 3DWA SM Ver 1 8 13 FOUR POST LIFT DIMENSIONS Max Wheel base 4 metre For VH model Fig 10...
Страница 19: ...Ref 3DWA SM Ver 1 8 16 FOUR POST LIFT DIMENSIONS Max Wheel base 4metre For In Lift Fig 13...
Страница 25: ...Ref 3DWA SM Ver 1 8 22 VH model 12 3 7 8 9 4 5 2 1 10 11 11 13 14 Fig 15...
Страница 26: ...Ref 3DWA SM Ver 1 8 23 AVH model 12 3 7 8 9 4 5 2 1 11 13 14 6 Fig 16...
Страница 69: ...Ref 3DWA SM Ver 1 8 66 For Drive Through model Fig 118...
Страница 70: ...Ref 3DWA SM Ver 1 8 67 Fig 119...
Страница 72: ...Ref 3DWA SM Ver 1 8 69 For Drive Through model Fig 121...
Страница 73: ...Ref 3DWA SM Ver 1 8 70 For In Lift model 865 865 Fig 122...
Страница 92: ...Ref 3DWA SM Ver 1 8 89 10 DIAGRAMS 10 1 BLOCK DIAGRAM Fig 154...
Страница 93: ...Ref 3DWA SM Ver 1 8 90 10 2 WIRING DIAGRAM 10 2 1 PT VH MODEL Fig 155...
Страница 94: ...Ref 3DWA SM Ver 1 8 91 Fig 156...
Страница 95: ...Ref 3DWA SM Ver 1 8 92 10 2 2 AVH MODEL Fig 157...
Страница 96: ...Ref 3DWA SM Ver 1 8 93 Fig 158...
Страница 97: ...Ref 3DWA SM Ver 1 8 94 10 2 3 IN LIFT MODEL Fig 159...
Страница 98: ...Ref 3DWA SM Ver 1 8 95 Fig 160...