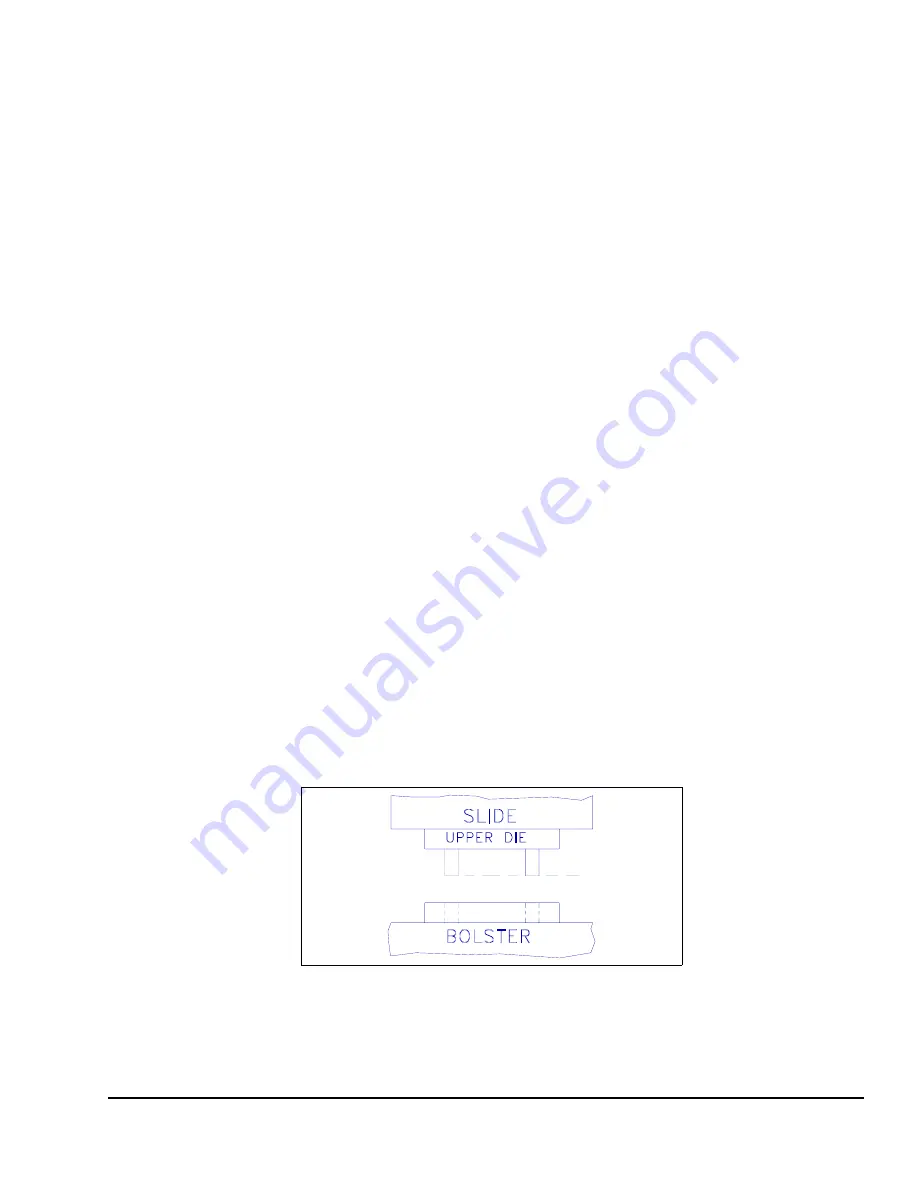
April 27, 2004 Manual Version 1.01
3.1
Figure 3.1:
Example Die 1
Section 3
Definitions and Terminology
This section will give some background and explain the meaning of various settings and readings in the
tonnage monitor. It is strongly recommended that this section be read in order to use the tonnage
monitor effectively!
Section 3.1
Tonnage
The tonnage monitor reads forming forces (“tonnage”) from strain gauges mounted on the machine
frame. Each strain gauge is a “channel”. Tonnage monitors typically have two or four strain gauges
depending on the type of machine. For example, OBI presses typically use two strain gauges (one on
each side), while straight side presses typically use four strain gauges (one on each corner). Section 7
covers gauge mounting considerations and procedures.
Section 3.1.1 Channel Tonnage
A channel tonnage is the tonnage read from a single strain gauge. A numerical channel tonnage reading
shown by the tonnage monitor is the highest tonnage exerted on that channel through the stroke or data
window (data windows are discussed in section 3.2). In addition, the tonnage monitor can show the
tonnage waveform for a channel. This waveform shows how the tonnage varies with press crankshaft
angle.
Section 3.1.2 Total Tonnage
In addition to recording the maximum tonnage measured for each channel, the tonnage monitor module
calculates and records the instantaneous summation of all channels. It performs the same peak
measurement on this value as is performed on the individual channels. This value is displayed as the
total tonnage exerted on the machine frame at any single position in the stroke.
When forces occur on all channels at the same time, the maximum total tonnage is the summation of the
maximum channel tonnages. For example, the die shown in Figure 3.1 contains two equally sharp
punches of equal cross-sectional area and equal length.
This die is located in the center of an OBI press bed equipped with a two channel tonnage monitor with
strain gauges mounted on both sides of the press frame. If the tonnage required for each punch is 100
tons and both punches impact the material at the same position in the stroke (at the same time) the graph
Содержание OmniLink II
Страница 5: ...April 27 2004 Manual Version 1 01 iv ...
Страница 7: ...April 27 2004 Manual Version 1 01 1 2 ...
Страница 21: ...April 27 2004 Manual Version 1 01 3 8 ...
Страница 43: ...April 27 2004 Manual Version 1 01 4 22 Section 4 5 3 3 N A Section 4 5 3 4 N A Section 4 5 3 5 N A ...
Страница 44: ...April 27 2004 Manual Version 1 01 4 23 Section 4 5 4 N A ...
Страница 45: ...April 27 2004 Manual Version 1 01 4 24 ...
Страница 69: ...April 27 2004 Manual Version 1 01 7 14 ...
Страница 77: ...April 27 2004 Manual Version 1 01 8 8 ...
Страница 79: ...April 27 2004 Manual Version 1 01 9 2 ...
Страница 81: ...April 27 2004 Manual Version 1 01 10 2 ...