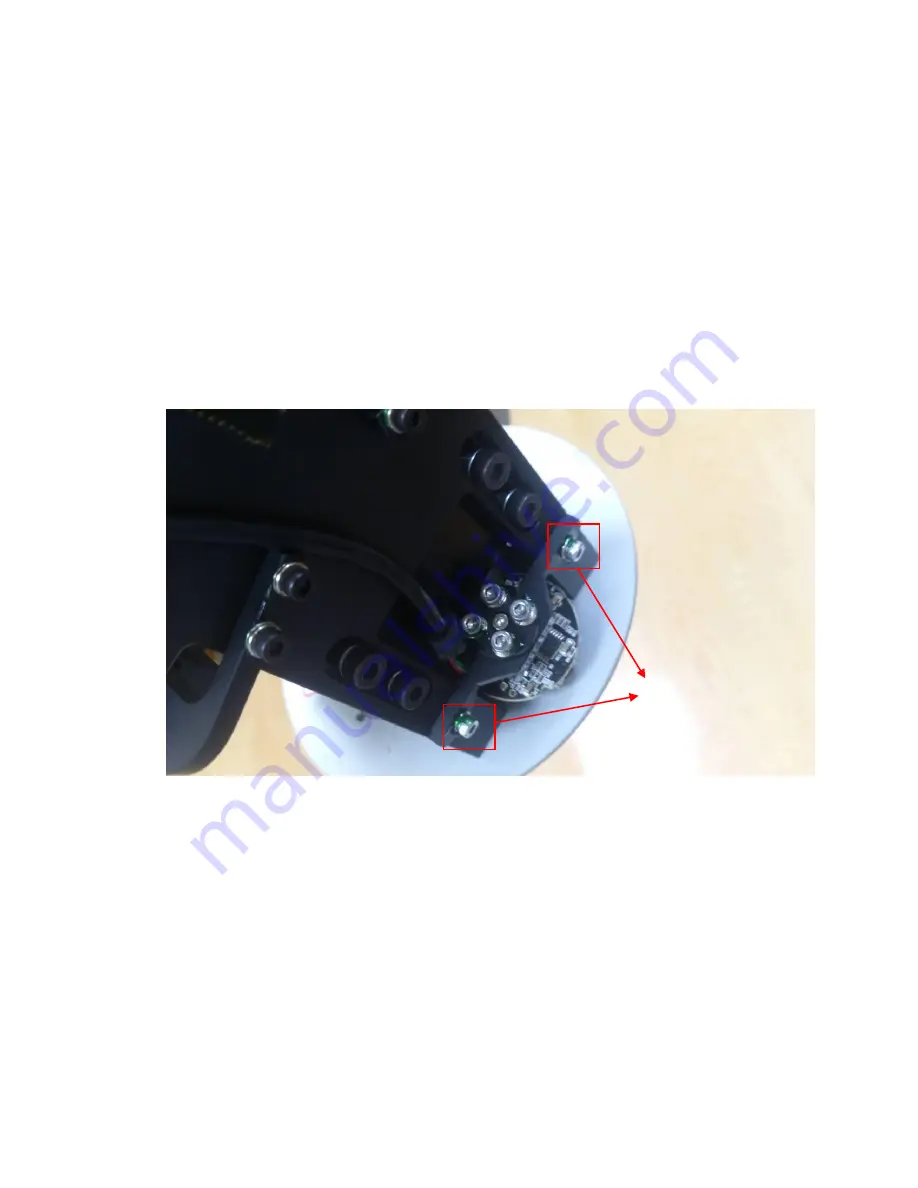
LightLink-CXL – Service Manual
Rev. No. : 01
Page
54
of
98
F. CCD Camera Replacement
Removal
1.
Remove the laser head front cover off and open the rear cover partially
2.
Disconnect and tag the cablings or connectors
3.
Remove the three screws
4.
Gently and slowly remove the PCB down
Note: Do remember to tag all the connectors
5. Loosen two screws and take CCD and holder off
6. Loosen nut at front side and take connect off
Note: This step must take all the connector off in addition to aiming connector
Figure 6.8 CCD Camera Replacement
Two screws and wirings
Содержание LightLink-CXL
Страница 1: ...Service Manual LightLink CXL Corneal Cross Linking System ...
Страница 90: ...LightLink CXL Service Manual Rev No 01 Page 89 of 98 ...
Страница 91: ...LightLink CXL Service Manual Rev No 01 Page 90 of 98 ...
Страница 93: ...LightLink CXL Service Manual Rev No 01 Page 92 of 98 ...
Страница 97: ...LightLink CXL Service Manual Rev No 01 Page 96 of 98 Finish this process we will get PASS ...
Страница 99: ...LightLink CXL Service Manual Rev No 01 Page 98 of 98 ...