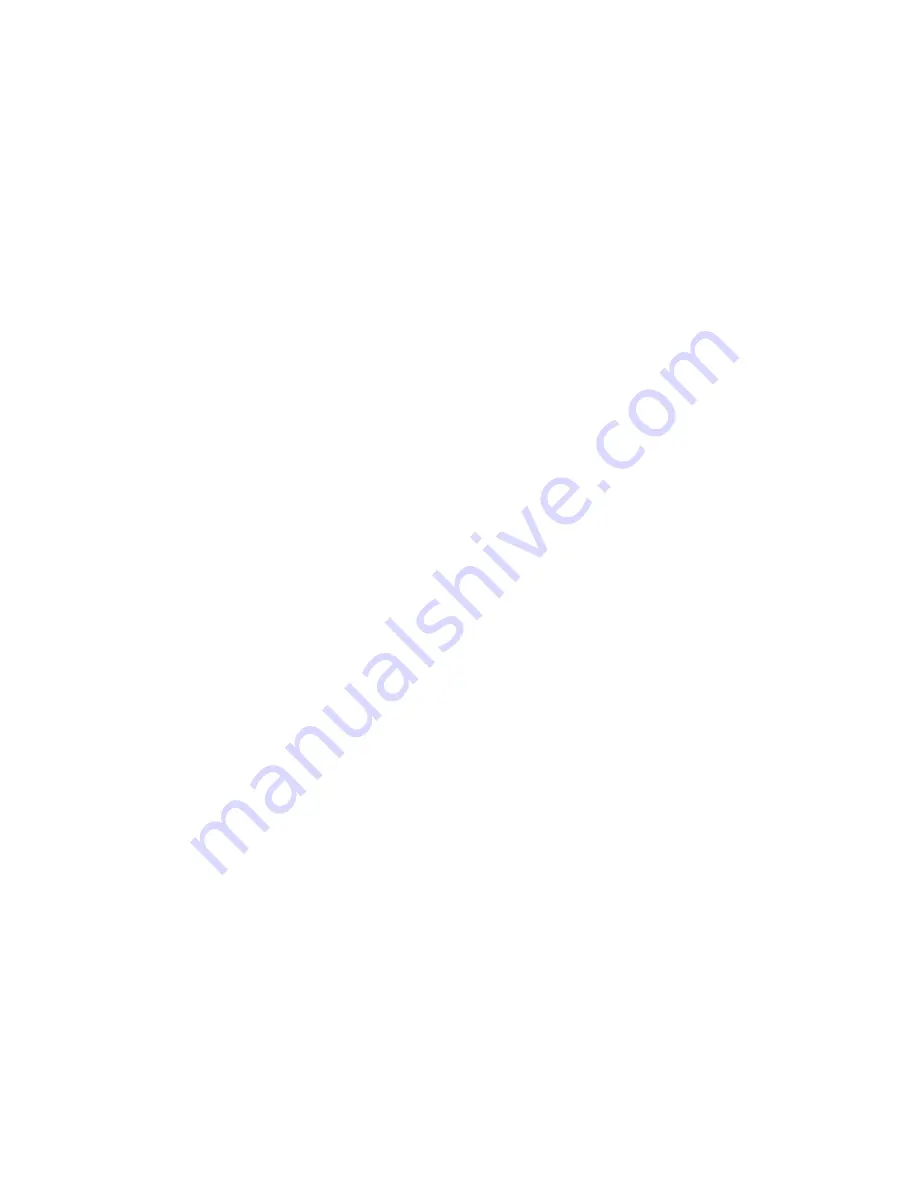
PROBLEM:
The film shrinks as it passed over the heat roller is known as “necking” in the
laminating trade.
SOLUTION
: Reduce the heat and/or the supply roll tension. The film is not shrinking so much
as it is being stretched by excess heat and tension, causing the web to get narrower as it is pulled
over the shoes.
PROBLEM
: No power is getting to the laminator.
SOLUTION
: Make sure there is power at the electrical outlet being used, and make sure both
ends of the power cord are firmly engaged. There are fuses inside the laminator, but dead outlets
and loose power cord connections are the most common causes of this problem.
PROBLEM:
Wavy or rippled sections in the laminate, especially toward the center of the web.
SOLUTION:
These “heat wrinkles” are caused by excess temperature and/or speed for the film
being used. Slow down the motor and/or use a lower appropriate temperature for that particular
film.
PROBLEM:
General haziness or cloudiness in the film after lamination.
SOLUTION:
Increase the temperature. That cloudiness is a function of incomplete adhesion.
On a variable speed machine loaded with thicker film, it may be that the film is being run too
fast and is not getting enough time on the heat rollers.
PROBLEM:
Bubbles in the center of the web and/or film not sticking to the center of an item.
SOLUTION:
. The likely cause of this symptom is worn rollers. For example, if hundreds of
thousands of 18-inch wide sheets are laminated on a 38-inch machine, the center of the rollers
can get worn down more than the ends of the rollers, creating a gap in the middle of the nip. In
this situation, the laminating rollers should be replaced. The rollers worn in this way are not
suitable for use as pull rollers.
For problems not listed here, contact your Ledco Dealer. If the Dealer doesn’t know the answer,
please ask the dealer to contact
LEDCO
and get back to you.
31