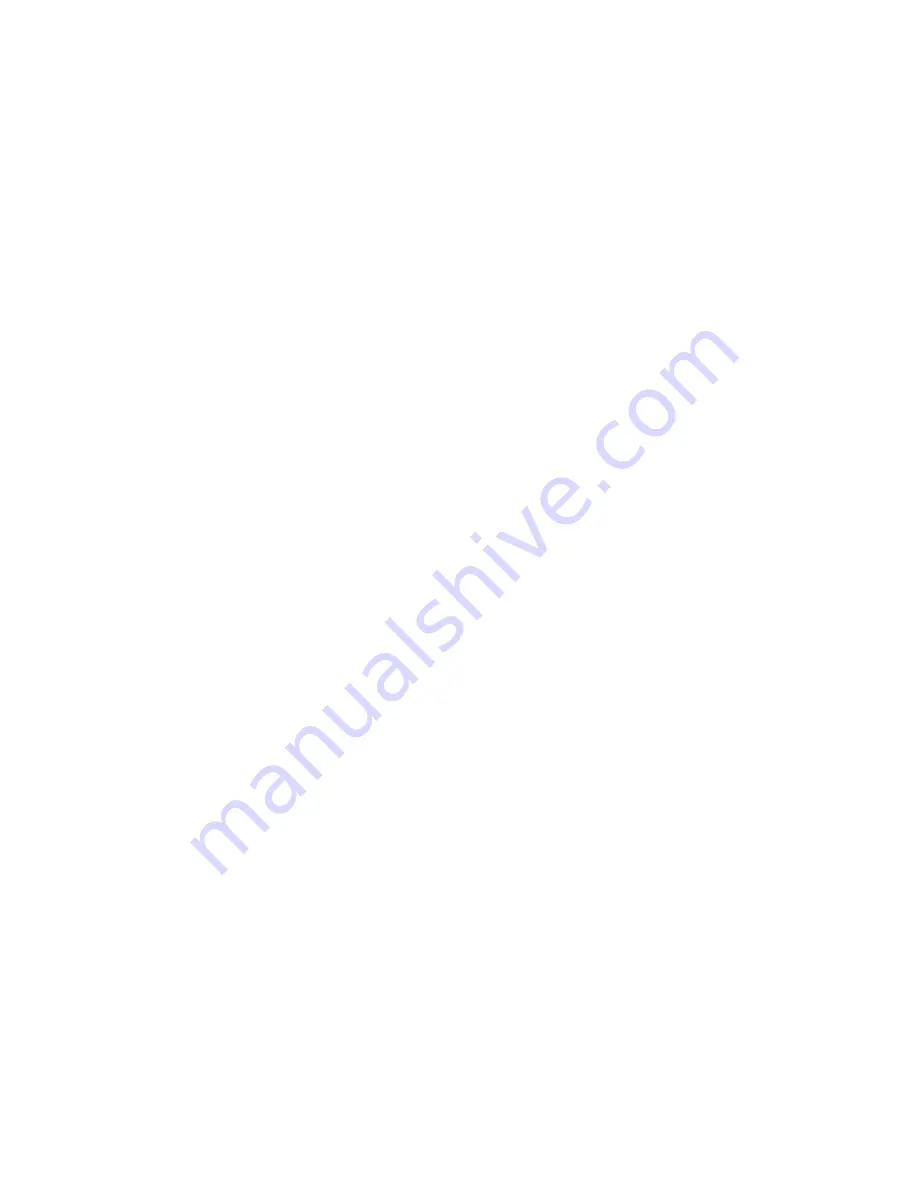
•
film with low-melt adhesives, also known as co-polymer films; these often have better clarity and
are less likely to curl or ripple
•
matte films to eliminate glare or to accept printing or writing; many suppliers offer films with both
glossy and matte (non-glare) finishes
•
film with UV inhibitors to protect colors in the laminated material from fading in sunlight
•
thermal film that has a pressure-sensitive adhesive and a release liner on its outer side; for
example, a poster with this material laminated on the back could easily be mounted without
fasteners or tape
•
high clarity films; some of these have a protective liner on the top outer surface… after a piece of
material has been laminated, trimmed, packed, and shipped, the person using the material can
remove the protective liner revealing a surface perfectly free of dust, scratches or abrasion
•
opaque or colored films for the back side of a lamination; these can form a border for a laminated
piece
•
iridescent clear films for special visual effects
•
permanently waterproof films for outdoor, underwater, or special applications; the most common
thermal laminating films are made with water-based primers and will eventually de-laminate if
continually exposed to water or weather; truly waterproof films are made with special primers
Rolls of film may be purchased in different widths. The size of the laminator is the only limitation to
the width of the film rolls you can use. The Professor 27 can use 4, 12, 18, 25, or 27 inch rolls. Make
sure the upper and lower roll widths are the same, and are aligned with each other.
When installing film, always center the rolls of film on the supply roll mandrels so the core grippers
engage the cardboard core
Rolls are also produced with different lengths of film on a roll (250', 500', 1000'). The Professor 27
will easily accommodate film rolls up to a 5" diameter.
We recommend 3-mil film for most common applications, including posters, signs or instructional
aids. The 3-mil film provides better protection, more rigidity, and a more lustrous appearance than1.5-
mil film. Five to ten mil film is suggested for those applications that need the most protection and
rigidity.
Lamination with 1.5-mil film can sometimes present problems because the film is so thin it loses heat
easily. It sounds backwards, but 1.5-mil film has to be run at a higher temperature than a 3-mil film
with the same adhesive. The higher temperature compensates for the faster rate of heat loss during
lamination. A standard 3-mil film is applied at 280 degrees Fahrenheit, while a standard 1.5-mil film
must be applied at 310 degrees F. Even when applied at 310 degrees F, a 1.5-mil film is still more
likely to delaminate later.
If the item being laminated is fairly thick, it will pull heat from the film.. This will lower the
temperature of the 1.5-mil film and prevent it from sticking properly. When laminating thick items
with standard 1.5-mil film, it may be necessary to raise the temperature to 330 or 340 degrees. Do not
8