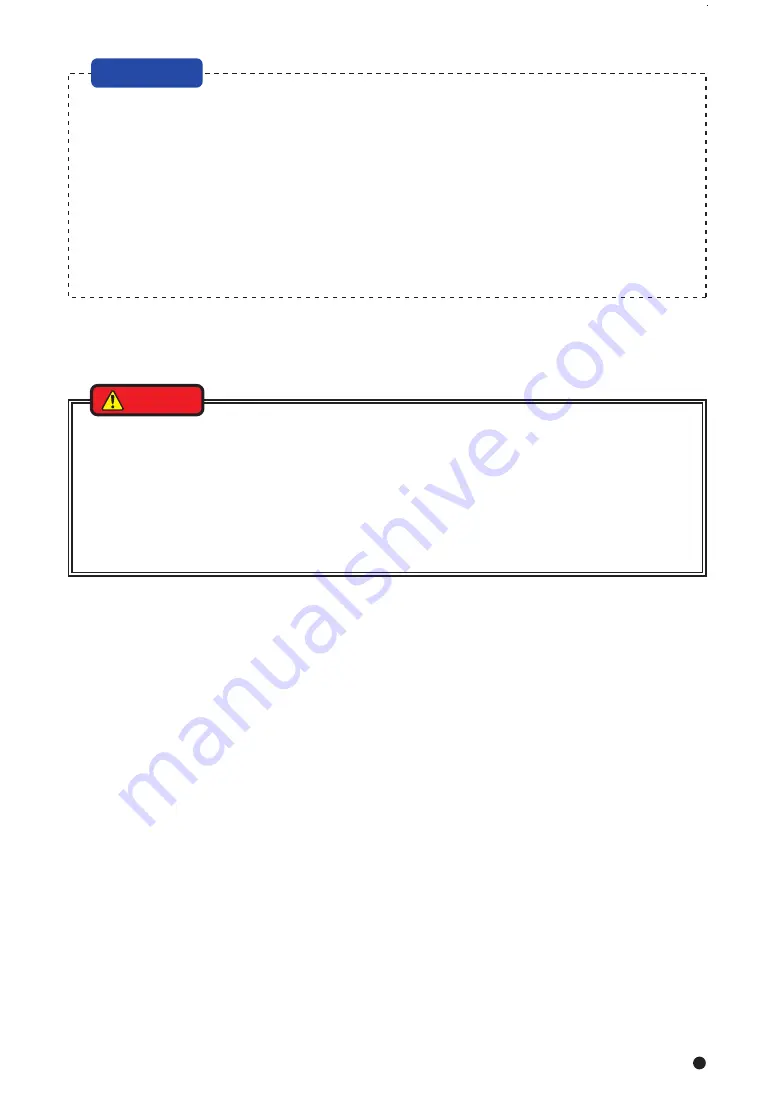
16
・In the case of inside diameter gripping, keep the input to 1/2 of the allowable maximum input or less. In the case
of inside diameter gripping, the length of engagement of the master jaw and the dovetail groove is shorter when
compared to the outside diameter gripping, therefore, the chuck will break, the work will fly out and this is
dangerous.
・In the case of using only 1 jaw for gripping reduce the input force by 2/3 or more. If 2 jaws are used for gripping
reduce the input force by 1/3 or more. If it is used without lowering the input, the input which is normally applied
evenly onto 3 of the jaws is concentrated onto 1 or 2 of the jaws. Otherwise the chuck will break, the work will fly
out and this is dangerous.
Analysis of the gripping force, input force and rotation speed using Fig. 8 is carried out as shown below.
・For example, in the case of BB206 standard soft jaw (mass moment 59.1kg・mm), it cannot exceed 6000min
-1
(rpm), and the gripping force loss due to the centrifugal force at this rotation speed is 39kN (approx. 3977kgf).
The required static gripping force for the dynamic gripping force (gripping force loss by static gripping force -
centrifugal force) to become 1/3 of the static gripping force is 58.5kN, and the required input to obtain this
gripping force is 20kN. However, it is necessary to use at the gripping part center height H=17.2 mm or less.
・If the gripping part center height H is high, it is necessary to lower the static gripping force.
・If the top jaw mass moment is large, the rotation speed needs to be lowered.
・If the rotation speed is high, the gripping force loss due to the centrifugal force becomes large. The centrifugal
force is proportional to the square of the rotation speed.
The required static gripping force and input force required at the rotation speed in use are predicted from Fig.8,
however, it contains a number of hypothetical conditions. Therefore, it is necessary to only use these as reference, and
the processing conditions must be determined after trial cutting without fail.
15
DANGER
NOTICE
Static gripping force
(k
N)
Fig.8
10
50
50
0
40
30
20
10
60
70
17.2
31
20kN
18kN
16kN
14kN
12kN
10kN
8kN
6kN
10
50
0
80
40
120
8kN
11kN
14kN
17kN
20kN
23kN
26kN
29kN
32kN
20
99
39
10
50
0
80
40
120
48.8kN
42kN
37kN
32kN
27kN
22kN
17kN
12kN
32
22.2
126
10
50
0
80
40
120
160
59kN
53kN
47kN
41kN
35kN
29kN
23kN
17kN
49
26.7
153
100
39
30
20
10
0
6000 min
-1
5500 min
-1
5000 min
-1
4500 min
-1
4000 min
-1
3500 min
-1
3000 min
-1
2500 min
-1
2000 min
-1
1500 min
-1
100
200
300
0
20
40
60
200
400
600
0
20
40
60
80
84
67
0
20
40
60
80
100
102
400
800
1200
3500 m
in
-1
3000 mi
n
-1
2500 mi
n
-1
2000 min
-1
1500 min
-1
1000 min
-1
750 min
-1
BB210
BB208
BB206
BB212
Input force
Input force
Limit
Gripping force loss
(k
N)
Standard soft top jaw
Mass moment of top jaw
m×r×3(㎏・㎜)
Standard soft top jaw
Gripping part center height H(㎜)
Static gripping force
(k
N)
Limit
Limit
Gripping force loss
(k
N)
Standard soft top jaw
Mass moment of top jaw
m×r×3(㎏・㎜)
Standard soft top jaw
Gripping part center height H(㎜)
Static gripping force
(k
N)
Input force
Gripping force loss
(k
N)
Standard soft top jaw
Mass moment of top jaw
m×r×3(㎏・㎜)
Standard soft top jaw
Gripping part center height H(㎜)
Static gripping force
(k
N)
Input force
Limit
Gripping force loss
(k
N)
Standard soft top jaw
Mass moment of top jaw
m×r×3(㎏・㎜)
Standard soft top jaw
Gripping part center height H(㎜)
4500 min
-1
4000 min
-1
3500 min
-1
3000 min-1
2500 min-1
2000 min-1
1500 min-1
1000 min-1
5000 min
-1
4500 min
-1
4000 min
-1
3500 min
-1
3000 min
-1
2500 min
-1
2000 min
-1
1500 min-
-
1
Содержание BB200 Series
Страница 35: ......