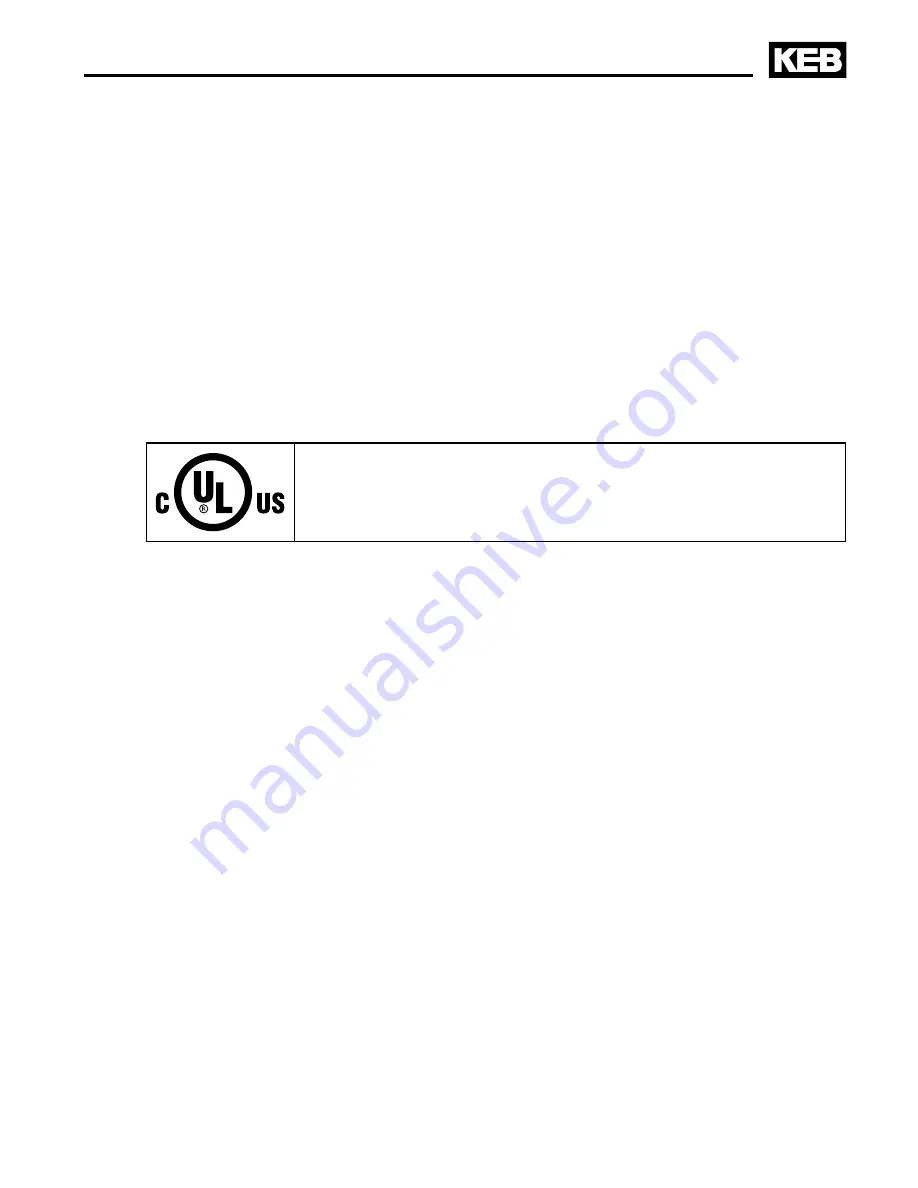
GB - 39
Annex B
Annex B
B.1 CE-Marking
CE marked frequency inverters and servo drives were developed and manufactured to
comply with the regulations of the Low-Voltage Directive 2006/95/EC.
The inverter or servo drive must not be started until it is determined that the installation
complies with the directive 2006/42/EC (machine safety directive) as well as the EMC-
directive (2004/108/EC)(note EN 60204).
The frequency inverters and servo drives meet the requirements of the Low-Voltage Direc-
tive 2006/95/EC. The harmonized standards of the series EN 61800-5-1 in connection with
EN 60439-1 and EN 60146 were used.
This is a product of limited availability in accordance with EN 61800-3. This product may
cause radio interference in residential areas. In this case the operator may need to take
corresponding measures.
B.2 UL marking
Acceptance according to UL is marked at KEB inverters with the
adjacent logo on the type plate.
To be conform according to UL for the use on the North American Market the following
instructions must be observed (original text in accordance with UL):
•
Control Board Rating (30Vdc, 1A) and rating of PTC terminal (S100B) (10V, 0.01A)
•
Marking for more than one factory
•
"Maximum Surrounding Air Temperature 40 °C"
•
“Internal Overload Protection Operates prior to reaching the 200% of the Motor Full
Load Current”
•
For 240V Models:
"Suitable For Use On A Circuit Capable Of Delivering Not More Than 18,000 rms
Symmetrical Amperes, 240 Volts Maximum. See instruction manual for Branch Circuit
Protection details"
For 400/480V Models:
"Suitable For Use On A Circuit Capable Of Delivering Not More Than 18,000 rms
Symmetrical Amperes, 480 Volts Maximum. See instruction manual for Branch Circuit
Protection details". For use in solid grounded wye sources only.
•
”Integral solid state short circuit protection does not provide branch circuit protection.
Branch circuit protection must be provided in accordance with the Manufacturer
Instructions, National Electrical Code and any additional local codes”.
•
"Use in a Pollution Degree 2 environment"
•
"Use 60/75°C Copper Conductors Only"
•
Motor Overtemperature Protection:
These drive models are not provided with load and speed sensitive overload protection
and thermal memory retention up on shutdown or loss of power (for details see NEC,
article 430.126(A)(2)”.