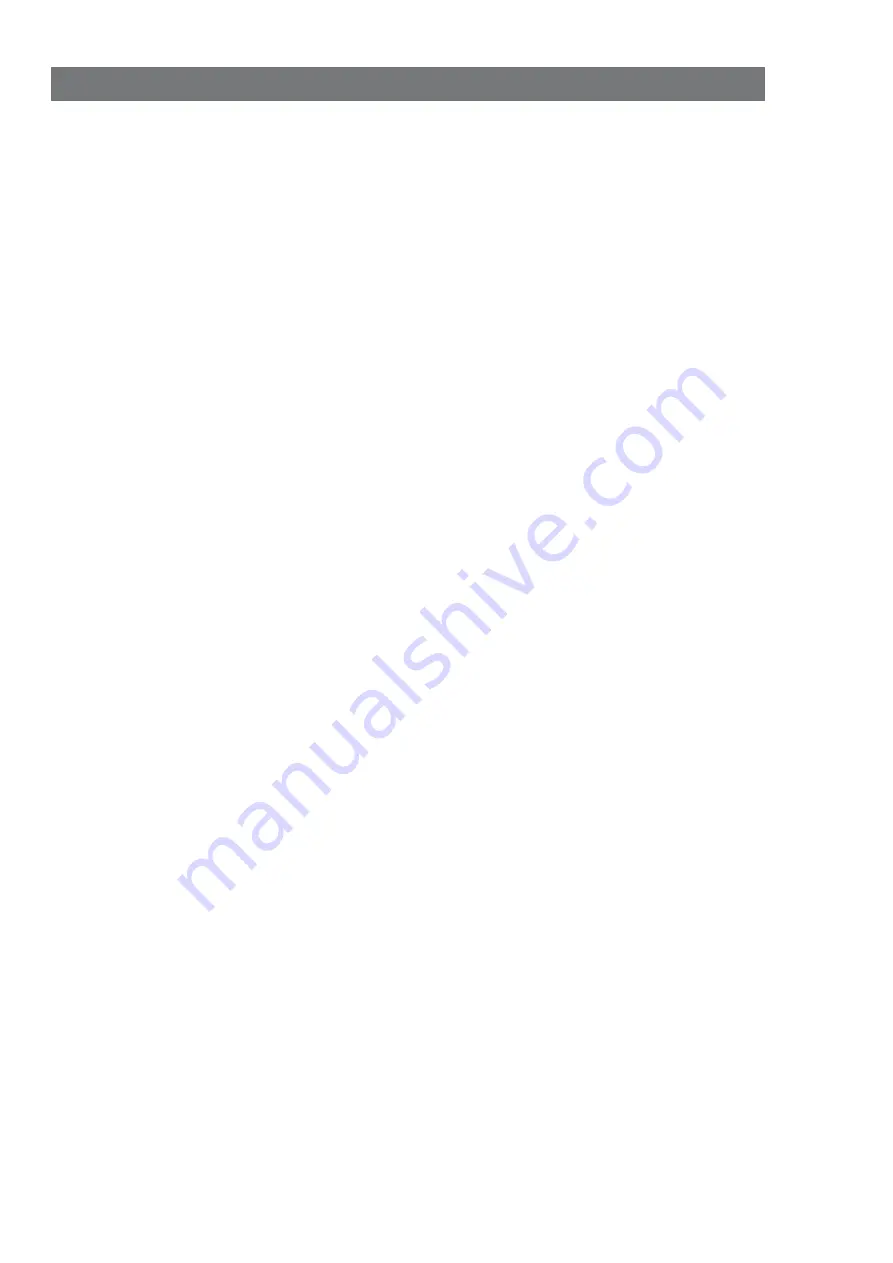
www.johnsonandstarley.co.uk
16
15. SERVICING & MAINTENANCE
IMPORTANT: Ensure that the gas and electricity supplies are isolated before commencing any servicing &
maintenance or replacement of components. Because the appliance is room sealed, it is also imperative that if
at any stage of repairs the gasket on the sealing plate is damaged it MUST be replaced! After completion of any
maintenance, always test for gas tightness and carry out a complete functional test of the appliance in accordance
with the Commissioning Instructions at paragraphs 13.1 to 13.6 inclusive.
15.1 ROUTINE MAINTENANCE
15.1.1 Operate the appliance and check for the correct function of the burner and controls.
15.1.2 Turn OFF the gas and electrical supplies to the appliance.
15.1.3 Remove the air heater front panel.
15.1.4 Remove and check the return air filter/cleaner for cleanliness, remove and clean the Air Circulation
fan as detailed in paragraph 15.8.
15.1.5 Remove the Burner and Controls Assembly as detailed in para 8.2. Inspect and clean the Main
Burner and injector as necessary. Examine the Main Burner for cracks, including hairline cracks,
exchanging the burner as necessary.
15.1.6 Inspect and clear the pilot burner orifice.
15.1.7 Clean the heat exchanger flueways by thoroughly brushing from above and below.
15.1.8 By viewing through the Fan Aperture, and using a torch or similar, examine the heat exchanger
externally for signs of cracks or holes, particularly around welded joints.
15.1.9 Using a torch or similar, introduce a light source into the heat exchanger burner aperture and upper
access port, and again examine the heat exchanger for signs of cracks or holes, particularly around
welded joints, whilst again viewing through the Fan Aperture.
15.1.10 Refit the Air Circulation fan, Burner and Controls Assembly, and air filter/air cleaner.
15.1.11 Light the appliance and note the main burner flame profile. If the flame profile is affected when
the Air Circulation fan switches on, check for any air leaks between the air heater and the base
plenum, paying particular attention to heaters with rear draught diverters. Rectify any air leaks before
continuing with this procedure.
15.1.12 Allow the air heater to operate for approximately 15 minutes to ensure stability, and with the main
burner lit, ensure that the operation of Air Circulation fan does not affect the main burner flame
profile.
15.2 BURNER
& CONTROL ASSEMBLY REMOVAL
15.2.1 Ensure that the Gas and Electrical supplies are switched OFF
15.2.2 Remove the appliance lower door.
15.2.3 Disconnect the igniter at the Piezo unit.
15.2.4 Disconnect the Multifunctional Control electrical connections.
15.2.5 Disconnect the gas supply by breaking the union at the input side of the Multifunctional Control.
15.2.6 Release the burner assembly fixing screw at the left hand side of the burner bar and withdraw the
Burner and Controls Assembly
15.2.7 Refit the Burner and Controls Assembly in reverse order.
15.3
BURNER & CONTROLS ASSEMBLY CLEANING
15.3.1 Remove the Burner and Controls Assembly as detailed in 15.2.
15.3.2 Remove the 2 screws securing the gas feed pipe to the burner bar, and remove the burner bar.
15.3.3 Clean the burner thoroughly both inside and out with a soft brush.
DO NOT ENLARGE, DISTORT
OR DAMAGE BURNER HOLES.
15.3.4 Reassemble in reverse order.
15.4
MAIN INJECTOR REMOVAL, CLEANING & REPLACEMENT
15.4.1 Remove the Burner and Controls Assembly as detailed in 15.2.
15.4.2 Unscrew the main injector from the housing.
15.4.3 Clean as necessary.
DO NOT ENLARGE, DISTORT OR DAMAGE THE MAIN INJECTOR HOLE.
15.4.4 If the injector is to be replaced, ensure that it is correctly marked, referring to the data badge for
details.
15.4.5 Refitment or replacement is in reverse order.
15.5
PILOT BURNER, THERMOCOUPLE & ELECTRODE REMOVAL AND REPLACEMENT
15.5.1 Remove the Burner and Controls Assembly as detailed in 15.2
15.5.2 Disconnect the Igniter lead from the Electrode.
15.5.3 Release the Pilot Feed Pipe from the pilot injector.
15.5.4 Release the retaining nut and withdraw the Thermocouple from the Pilot Burner Assembly, taking
care to avoid causing damage to the capillary.
15.5.5 Release the Electrode securing nut from the Pilot Burner Assembly and withdraw the Electrode.
Содержание 42-451-09
Страница 21: ...21 Sales Spares Replacement Help Line 01604 762881 FIGURE 11 HI SPEC J40 DIMENSIONS 17 DIMENSIONS...
Страница 23: ...23 Sales Spares Replacement Help Line 01604 762881 MAIN BURNER NOT OPERATING...
Страница 24: ...www johnsonandstarley co uk 24 20 DEFECT DIAGNOSIS FLOWCHART FIGURE 12 SYSTEM E T FUNCTIONAL DIAGRAM...
Страница 25: ...25 Sales Spares Replacement Help Line 01604 762881 FIGURE 13 BASIC FUNCTIONAL DIAGRAM...
Страница 26: ...www johnsonandstarley co uk 26 FIGURE 14 SYSTEM E T CONTROL CIRCUIT DIAGRAM 21 LOGIC DIAGRAM...
Страница 27: ...27 Sales Spares Replacement Help Line 01604 762881 FIGURE 15 BASIC CONTROL CIRCUIT DIAGRAM...
Страница 29: ...29 Sales Spares Replacement Help Line 01604 762881 FIGURE 16 HI SPEC J40 EXPLODED DIAGRAM 23 EXPLODED DIAGRAM...