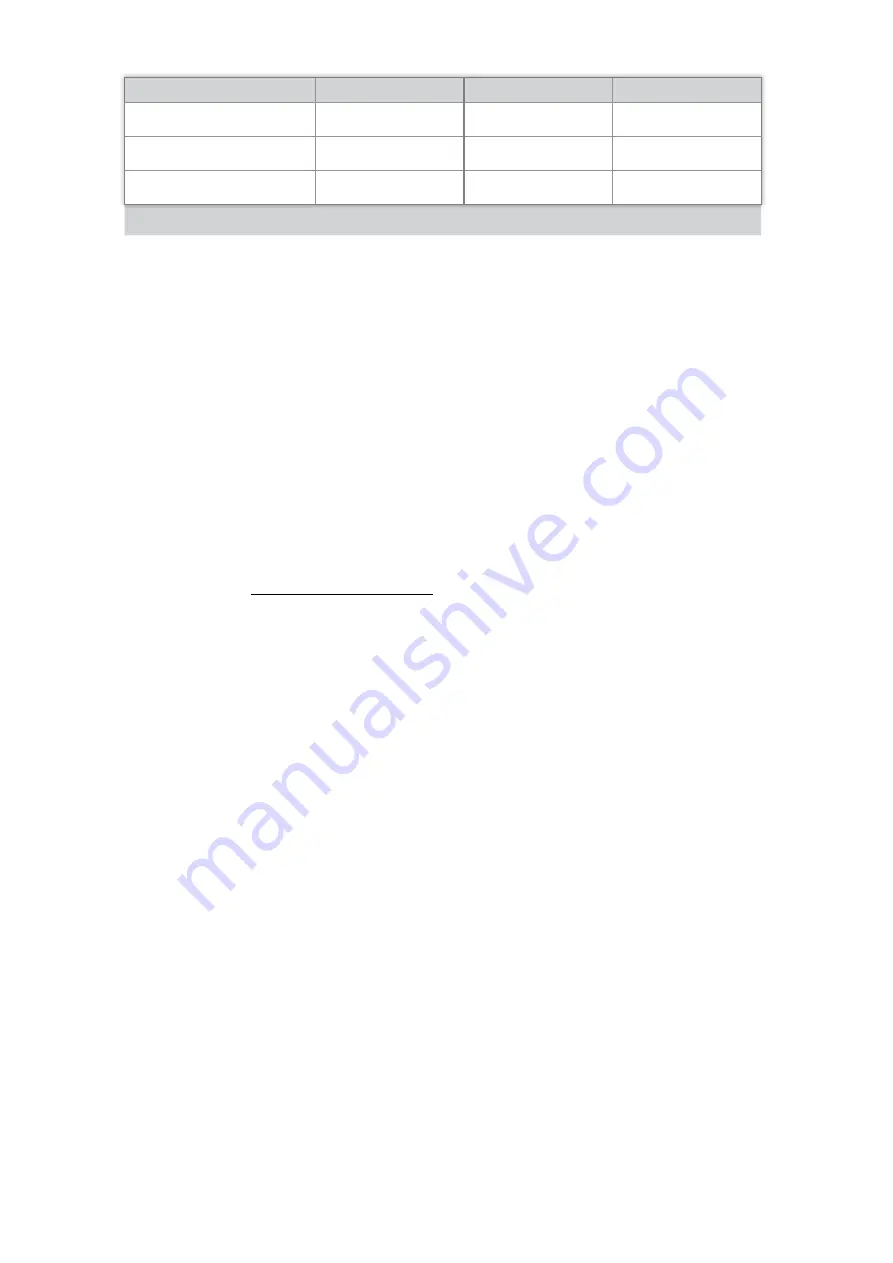
www.johnsonandstarley.co.uk
10
TABLE 5. INLET & OUTLET RESISTANCE
d.
Worked Calculation Example
A warm air unit with a 100mm (4”) diameter flue spigot, fitted with a prefabricated flue system leading to a
ridge tile in the loft. Refer to Figure 4.
From Table 3
K
ia
Inlet resistance of actual flue
=
2.5
K
oa
Outlet resistance of actual flue
=
2.5
K
ie
Inlet resistance of equivalent flue
=
2.5
K
oe
Outlet resistance of the actual flue
=
2.5
From Table 2
Other resistances of actual flue:
Terminal
=
2.5
Pipe bend ( 2 x 0.61)
=
1.22
Pipe (4 x 1m @ 0.78)
=
3.12
(5 x 0.3m @ 0.78)
=
1.17
Sum K
=
8.01
Equivalent height
From the formula
(2.5 + 2.5)
H
e
= 6.2 x
(2.5 + 2.5) - (0.78 x 6.2) + 8.01
H
e
= 3.793
This flue exceeds 1.0m equivalent height and is therefore satisfactory.
NOTE:
Ventilation of the compartment, room or internal space in which the appliance is to be installed must be
checked for compliance with the requirements of BS 5440 Part 2, Refer to section 3 of these instructions and
upgraded as necessary.
9.5.12 Special consideration must be given to external flues with a view to prevention of condensation and weathering
problems.
9.5.13 An approved terminal should always be used; a ridge terminal or “GC1” terminal is specifically recommended.
The latter should be positioned in a free air space where it is not shielded by any structure. A minimum of
1m (3ft.) from any vertical or inclined roof structure must be allowed for.
9.5.14 Where flue blocks are used, builders should ensure that no obstruction is created during erection. The installer
should ensure that the connection flue does not project beyond the internal wall of the flue blocks and that
there is provision for examination and servicing.
9.5.15
IMPORTANT
: Before installing the appliance, carry out a visual check of the flue system as directed in the
relevant section of BS 5440 Part1, then check the flue performance as follows:-
a.
Close all doors and windows in the room in which the appliance is to be installed.
b.
Introduce some heat into the flue, using a blow torch or other means.
c.
Carry out a flow visualisation check with a smoke pellet at the intended position for the appliance.
Ensure that there is discharge of smoke from the correct terminal only, and no spillage into the room.
Smoke coming out of other than the correct terminal only, or a down draught or ‘no flow’ condition,
indicates that the flue has failed the test, and the appliance shall not be connected until the defect has
been found and rectified, and the test satisfactorily completed.
APPLIANCE
INLET RESISTANCE (K
i
)
FLUE
OUTLET RESISTANCE (K
o
)
100mm Dia Spigot
2.5
100mm Flue
2.5
125mm Dia Spigot
1.0
125mm Flue
1.0
150mm Dia Spigot
0.48
150mm Flue
0.48
Содержание 42-451-09
Страница 21: ...21 Sales Spares Replacement Help Line 01604 762881 FIGURE 11 HI SPEC J40 DIMENSIONS 17 DIMENSIONS...
Страница 23: ...23 Sales Spares Replacement Help Line 01604 762881 MAIN BURNER NOT OPERATING...
Страница 24: ...www johnsonandstarley co uk 24 20 DEFECT DIAGNOSIS FLOWCHART FIGURE 12 SYSTEM E T FUNCTIONAL DIAGRAM...
Страница 25: ...25 Sales Spares Replacement Help Line 01604 762881 FIGURE 13 BASIC FUNCTIONAL DIAGRAM...
Страница 26: ...www johnsonandstarley co uk 26 FIGURE 14 SYSTEM E T CONTROL CIRCUIT DIAGRAM 21 LOGIC DIAGRAM...
Страница 27: ...27 Sales Spares Replacement Help Line 01604 762881 FIGURE 15 BASIC CONTROL CIRCUIT DIAGRAM...
Страница 29: ...29 Sales Spares Replacement Help Line 01604 762881 FIGURE 16 HI SPEC J40 EXPLODED DIAGRAM 23 EXPLODED DIAGRAM...