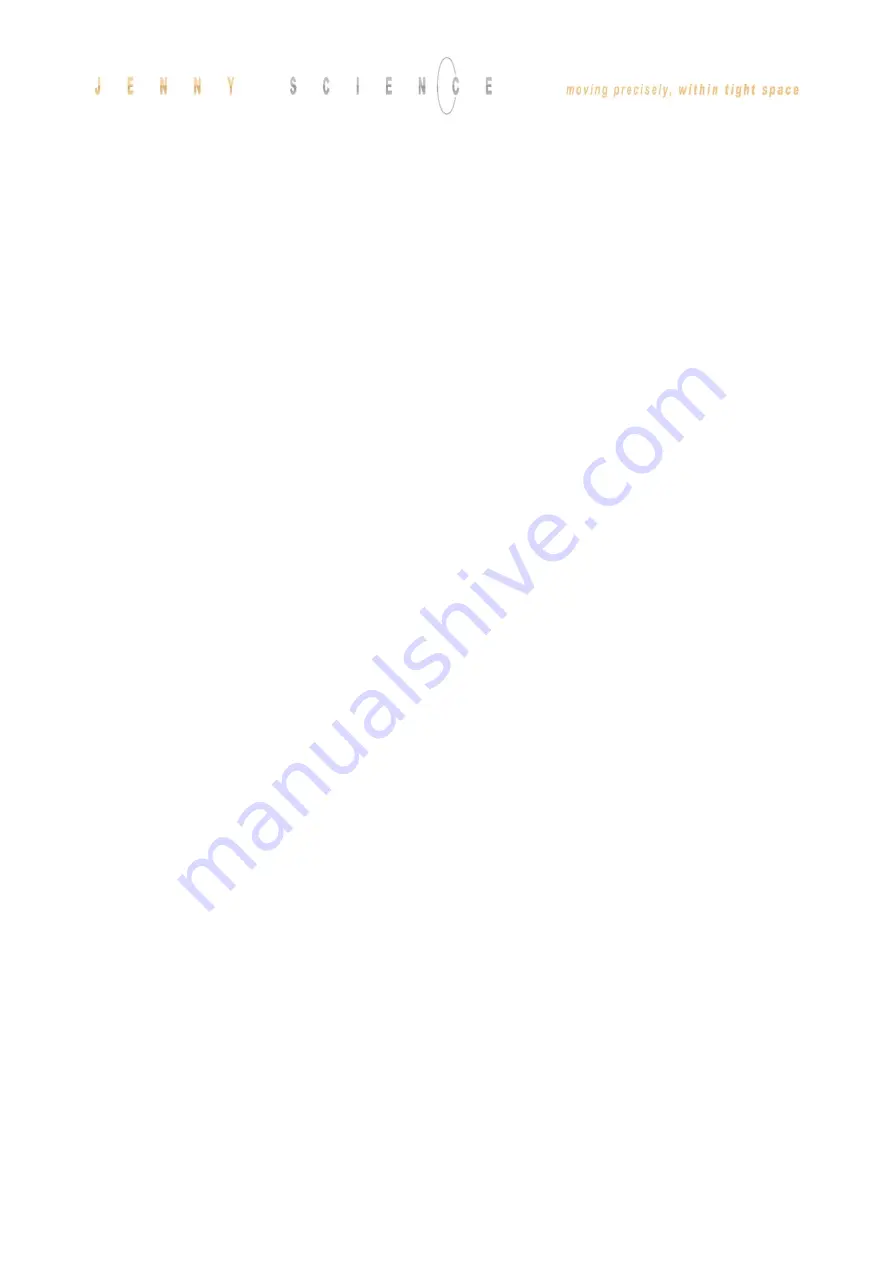
96
30
Limit I Force reached
Force proportional motor current reached “Limit I_Force Value”
(LIF). Motor current is
limited to “Limit I_Force Value”. A possible
detected error 50 (position deviation to large) is suppressed.
32
I_Force Drift Compensation failed
Automatic I_Force Drift Compensation drive was blocked or the
compensation position could not be held steady for 150ms (e.g.,
due to vibration)
Warnings
40
Driveway limitation due to soft limit
values
Soft limits can be adjusted in WebMotion® in menu
„move axis / by
click“.
41
HW-Limit switch positive/negative active
HW-Limit switches are defined as input function
“
LIMIT SWITCH
NEGATIVE”
/
“
LIMIT S
WITCH POSITIVE”
42
Remote Controller Command rejected
One of the slave axes has an error or command for the slave could not
be executed
43
Remote Controller not recognized
Master Slave configuration: Not all remote controllers defined in the
master were recognized. The programs in the master have to be
checked and the invalid remote controllers (Rem ID) have to be
deleted.
44
Remote controller communication error
Check Master/Slave cable
45
AD Offset Error
The AD-Offset for measuring the current could not be retrieved
correctly during the first drive. The linear motor has to be turned off
while the output stage is turned on for at least 0.5s, so the AD-Offset
can be retrieved correctly.
46
Cyclic data are not valid
Cyclic data specified via the bus modules are not valid.
Check the Data S-Curve, Deviation position, Deviation Target position, I
Force Max, Speed and Acceleration. Or PDO cycle time it not correct
(only a multiple of 100us is valid).
47
Drive interrupted through SMU
The current drive was interrupted through the functional safety SS2 or
SLS.
Errors
50
Position deviation is too large.
The difference between the internal calculated position and the
present motor position (encoder) is larger than the value defined as DP
(deviation position) in Closed Loop setup.
Refer to chapter 14.2 Notes for Error 50
54
Excessive rise of temperature or weak
signal of LINAX® read head
Temperature rise too high/fast or the signal in the detector head of
the measuring system is too weak.
Check our drive profile or clean glass scale on LINAX® linear motor.
55
Excessive rise of temperature
Temperature rise too high/fast.
Check our drive profile.
59
JSC Motor does not fit application data
Connected JSC motor does not fit to the motor stored in application
data (e.g. if a new JSC motor type is connected to the servo
controller). Motor type reset (RESM) is required.
60
Over-temperature power stage
Above 85° detected by separate temperature sensor on power stage.
Power stage will be switched off.
61
Overvoltage of power supply
Power supply voltage or retarding energy from motor too high. Error
occurs only if power stage is turned off. If power stage is turned on,
please refer to error code 62.
62
Ballast circuit too long active
The ballast circuit is still more than 5 sec continuously active: Retarding
energy too high or the power supply voltage is too high, the power
stage will be switched off.
63
Over-temperature LINAX®/ELAX®/ROTAX®
Coil temperature above 80° in LINAX® / ELAX® linear motor or ROTAX®
rotative axis. Power stage will be switched off.
64
Under voltage of power supply
Motor power supply voltage is too low. The power supply probably is
not able to temporary deliver the demanded current.
65
Field adjustment on the magnet poles
The adjustment on the magnet pole was not successful, travel-plate of
LINAX® / ELAX® or rotor of the third party motor is blocked or encoder
/ motor cable is broken. If at multi-axis applications, all servo
controllers show error 65, then the D-sub encoder connector is
unplugged at one axis. Check the value payload (ML).