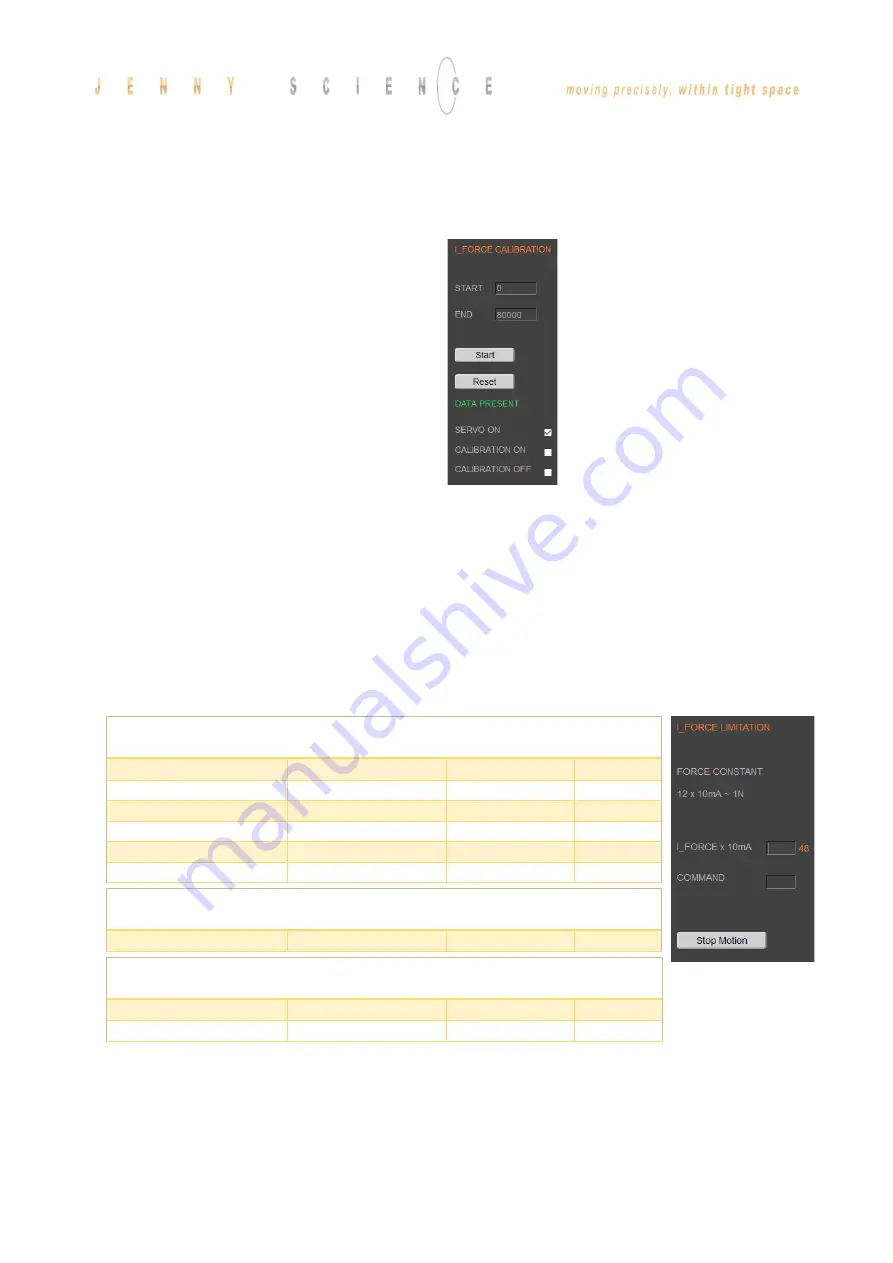
86
12.3
Forceteq® basic via XENAX®
12.3.1
I_Force Calibration
With the patented function „force calibration“ of the
XENAX® servo controller, the cogging-, load- and
friction forces of the iron core LINAX® and ELAX®
linear motor axes and the ROTAX® rotary axes from
Jenny Science can be detected. This is how it
becomes possible to limit, monitor and control forces
in processes.
START
: Determining the beginning position of
calibration process in increments.
END
: Determining the ending position of calibration
process in increments.
In order to increase the accuracy of the detected
forces at temperature variations, the temperature
drift of the detection is continuously compensated at
disabled power stage. The compensation also takes
place before each start of a
„force
C
alibration“
.
12.3.2
I_Force Limitation
The current value „I_Force“ is proportional to the
force. Following graph shows corresponding relations
for the different linear motor types.
LINAX®
Linear Motor Axis
Force Constant
Minimal
detectable force
Resolution
Lxc F04
50 * 10mA ~ 1N
0.5N
0.25N
Lxc F08
32 * 10mA ~ 1N
0.5N
0.25N
Lxc F10
28 * 10mA ~ 1N
0.5N
0.25N
Lxc F40
11 * 10mA ~ 1N
1N
0.5N
Lxe F40
11 * 10mA ~ 1N
10N
5N
Lxu/Lxs F60
10 * 10mA ~ 1N
10N
5N
ELAX®
Linear Motor Slide
Force Constant
Minimal
detectable force
Resolution
Ex F20
12 * 10mA ~ 1N
0.5N
0.25N
ROTAX®
Rotary Motor Axis
Torque Constant
Messbares
Min.moment
Resolution
Rxhq T0.3
8 * 10mA ~ 0.01Nm
0.02Nm
0.01Nm
Rxvp T0.04
23 * 10mA ~ 0.01Nm
0.006Nm
0.003Nm
Example:
A compression die should apply no more than 4N
force on an object.
Force Limitation with „LIMIT I
-
FORCE“
e.g.. ELAX® force constant: 12 x 10mA ~ 1 N
48
x 10mA ~ 4 N
Normal operation, calibration active
Test calibration active
Test without calibration