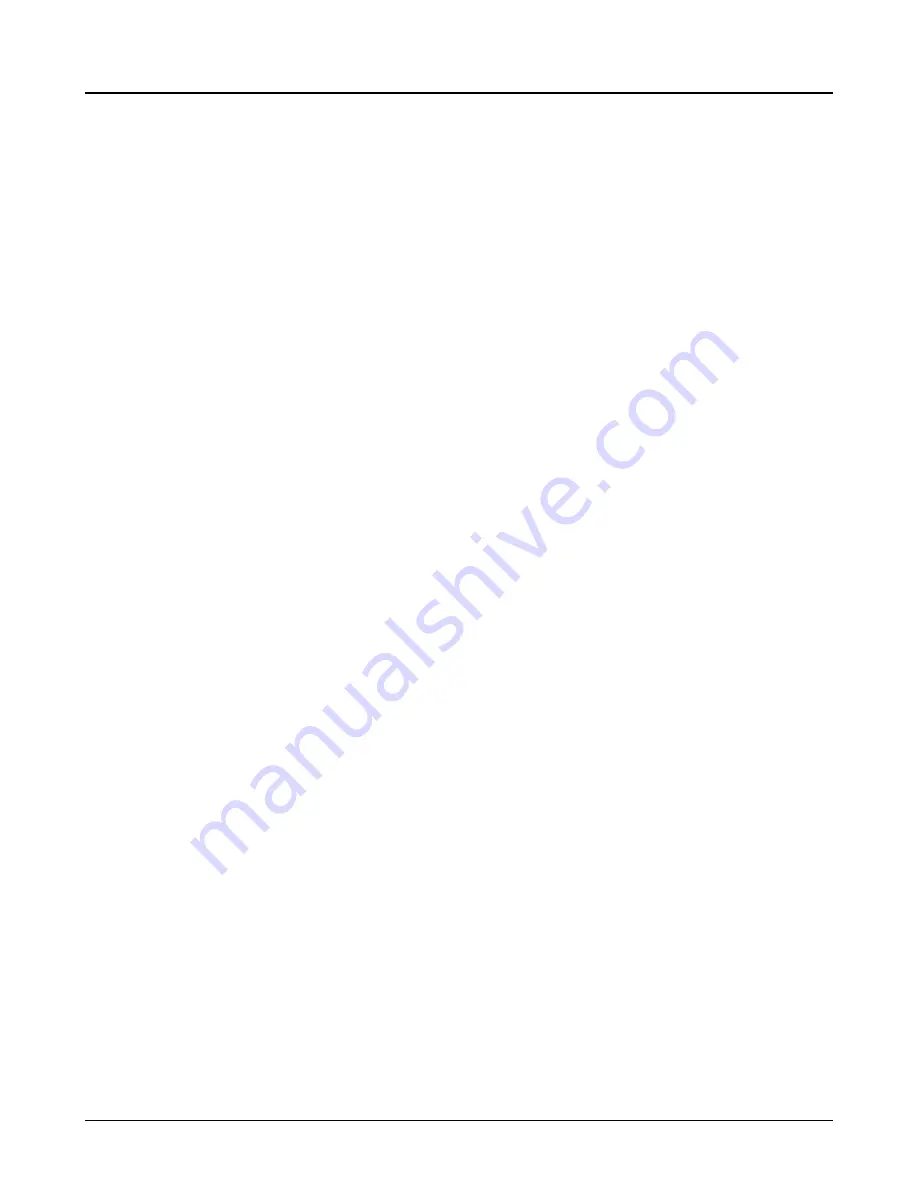
6.3 Reassembly
6.3.1 Reassemble the Pump
1.
Be sure shaft (122) and sleeve (126) are clean and free of all burrs. Slide shaft sleeve (126) over
shaft (122), making sure that O-rings are in place as indicated on assembly drawing. Secure sleeve
with set screw (222C) and key (128D).
2.
Provide adequate support for bearing housing (134) and shaft (122). Carefully slide shaft through
stuffing box of suction elbow. Bolt bearing housing to suction elbow (315A).
3.
Install shaft O-rings (496C & 496D) on shaft (122). Place the shaft key (178) in the keyway. Lubri-
cate the O-rings as required.
4.
Carefully install impeller (101) on shaft (122). With shaft washer (9985) in place, install (4) cap
screws (370C) to secure the impeller to the shaft. Install impeller end cap (9988) with o-ring (496B)
as required.
5.
Bolt casing (100) to elbow (315A) with (6) bolts evenly spaced around bolt circle. Leave bolts loose
enough to shift casing for alignment with impeller. The actual adjustment of casing is accomplished
by turning the adjusting screws (370B) against casing flange.
6.
The procedure for setting impeller clearance is described in the ALIGNMENT section of these in-
structions. When acceptable alignment has been achieved, secure the initial (6) bolts, then install
the remaining bolts and tighten.
7.
Before connecting the coupling halves, check direction of motor rotation. Manually turn pump shaft
to insure no rubbing. Be sure the pump and gear box shafts are in alignment according to the previ-
ously discussed alignment procedure.
8.
Connect coupling halves and any intermediate shafting.
9.
Assemble discharge piping to casing.
10. If packing is used, assemble gland, packing, lantern rings and sleeve into stuffing box. Do not com-
press too tightly until after start-up. The packing will need to be "run-in" and adjusted for proper flow
of lubricating water. If a mechanical seal is used, please see the mechanical seal IOM for proper
installation of seal.
11. Connect seal water and cooling lines to pump. Fill the oil lubrication system. Be sure bearing hous-
ing oil is level with the center of the sight glass.
6.3.2 Reassemble the Power End
1.
Be sure shaft is clean and free from all burrs.
2.
Heat inboard radial bearing (168C) in a 200°F (93°C) oil bath or by induction heater. Slide bearing
on shaft (122), butting against shaft shoulder. Position oil wheel (248) on shaft (122) and secure
with set screws.
3.
Heat thrust end bearings (112) & (112C) and sleeve (if used), in 200°F (93°C) oil bath. If thrust bear-
ing rotation race mounts on spacer (443), install race on collar and heat collar with bearing mounted
in oil bath.
8.2.1 42-54 (Top Suction) AF with LMR Bearings on page 66
, slide
bearing (112), spacer (237), and sleeve into position, tight against each other and against shaft
shoulder. After sleeve has cooled, install thrust bearing (112C).
4.
When the thrust bearing is in the outboard position the stationary race will usually fit over the lock
nut and washer. This saves the trouble of trying to keep the race in position because it can be set
aside until retainer (109) is installed.
a) For end suction pumps
8.2.2 42-54 (End Suction) AF with LM Bearings on page 66
, slide
spacer (443) with mounted thrust bearing (112C), including stationary race, into position
against shaft shoulder. If a spacer drive key is used, be sure it is installed. Install bearing (112)
against collar.
5.
Secure bearings with lockwasher (382) and locknut (136). Retighten locknut while components are
cooling to keep them tight together.
6.3 Reassembly
Model AF (42"/1200mm/54"/60"/66") LM/LMR Bearings Installation, Operation, and Maintenance Manual
55