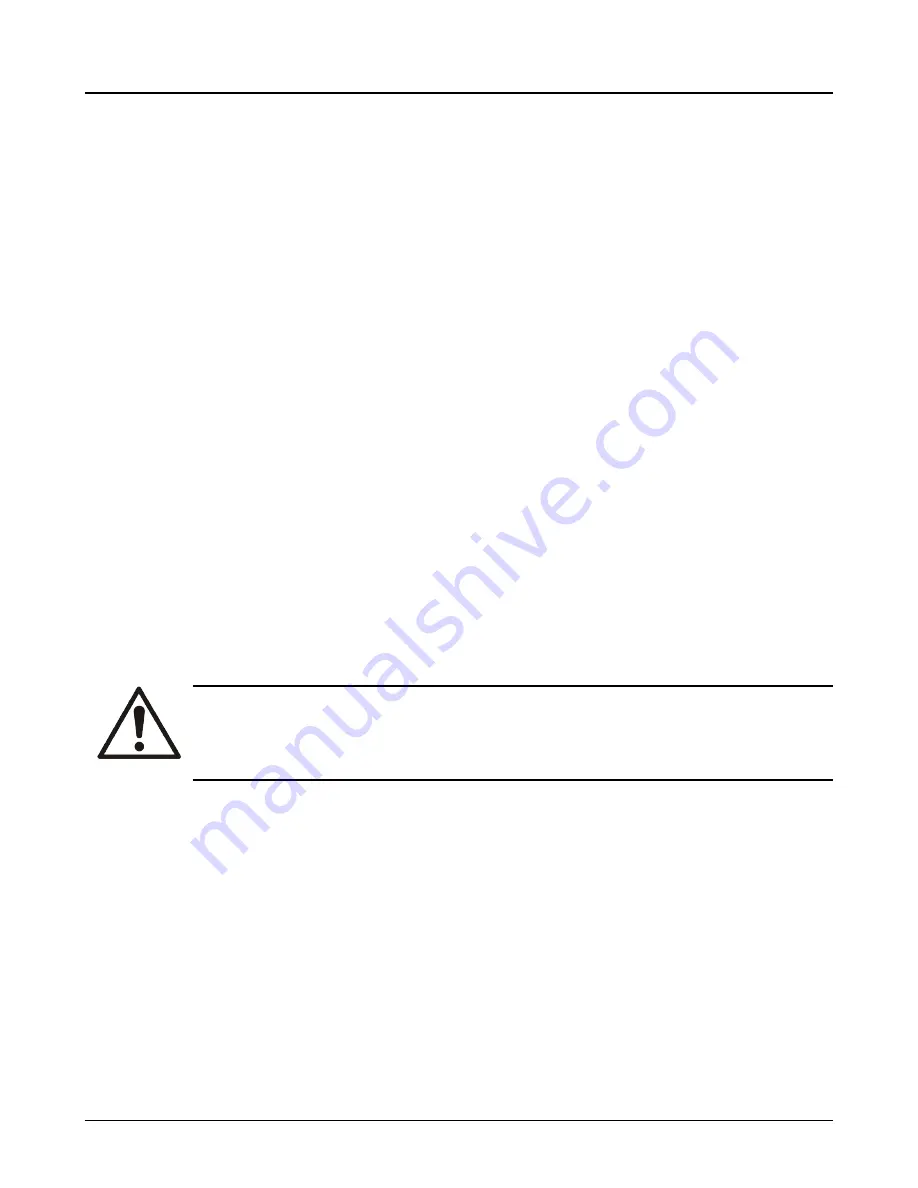
High HP demand
1.
Increased head or viscosity
2.
Pump speed too high
3.
Specific-gravity of slurry higher-than normal
4.
Packing gland pulled up too tight
5.
Impeller rubbing in casing
Noisy or rough operation
1.
Throttled suction or plugging
2.
Impeller rubbing in casing
Damage occurs from:
1.
Increased vibration levels - Affects bearings, stuffing box seal chamber, and mechanical seals.
2.
Heat build up - Vaporization causing rotating parts to score or seize.
3.
Cavitation - Damage to internal surfaces of pump.
4.
Loose impeller
5.
Broken impeller blade
6.
Bearings not properly lubricated
7.
Bent shaft
8.
Impeller out of balance.
Operating under freezing conditions
Exposure to freezing conditions, while pump is idle, could cause liquid to freeze and damage the pump.
Liquid inside pump should be drained.
5.4 Shut down the pump
1.
Turn off power to pump motor.
2.
In case of necessary maintenance or pump inspection, lock driver to prevent accidental rotation.
WARNING:
When handling hazardous and/or toxic fluids, skin and eye protection are required. If pump is
being drained, precautions must be taken to prevent physical injury. Pumpage must be handled
and disposed of in conformance with applicable environmental regulation.
5.5 Final Alignment
1.
Run the pump under actual conditions for a sufficient length of time to bring the pump and driver
up to operating temperature.
2.
Check alignment per alignment procedure outlined earlier.
5.4 Shut down the pump
44
Model AF (42"/1200mm/54"/60"/66") LM/LMR Bearings Installation, Operation, and Maintenance Manual