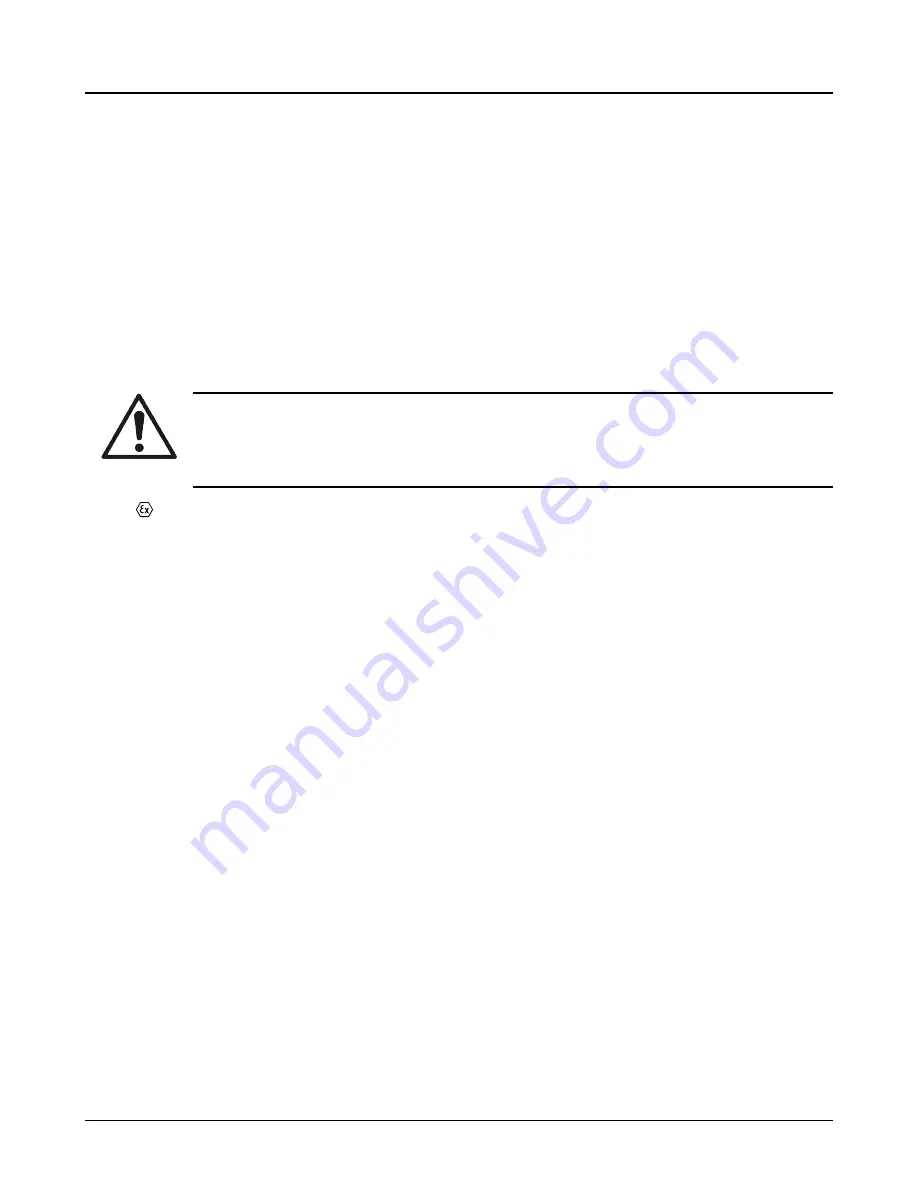
12. While field conditions preclude absolute accuracy, a check of pump performance will give reason-
ably close results. This can be done by installing a mercury manometer at pipe taps located at
least-one pipe diameter away from the suction and discharge flanges of the pump. If-gauges are
used, the pressure differential times 2.31 divided by the specific gravity of the slurry indicates the
TDH against which the pump is actually operating. If a manometer is used, then inches of mercu-
ry times 1.0455 divided by specific gravity equals TDH, providing water is in both legs of the
manometer and connecting lines.
13. Check the pump speed and determine flow rate (gpm) from the pump curve. This curve will also
give efficiency from which the hp requirement can be determined. A double check is to take mo-
tor ammeter readings, convert to hp, figure 90% drive efficiency, and use it against the pump
curve to get GPM. This is only an approximate check, as the hp curve on some applications is
rather flat, but is probably within 7-1/2%. It is important to take and record these readings when
the equipment is new, so that later readings can be judged on a relative basis.
Operating at reduced capacity
WARNING:
Risk of explosion and serious physical injury. Do not operate pump with blocked system piping
or with suction or discharge valves closed. This can result in rapid heating and vaporization of
pumpage.
Driver may overload if the pumpage specific gravity (density) is greater than originally assumed, or the
actual flow is much less than the rated flow.
The pump and system must be free of foreign objects. If pump becomes plugged, shut down and unplug
prior to restarting pump.
Listed below are some causes for circulation loss. Keep in mind that operation at reduced capacities can
cause damage to the pump.
1.
Increase in TDH against which pump operates could be caused by:
1.
Heat exchanger tubes partially plugged.
2.
Too many heat exchanger tubes blanked off
3.
Improperly sized or partially plugged strainer.
2.
Viscosity of slurry higher than it should be.
3.
Pump speed low. V-belt drive may be slipping and operating pump below design speed.
4.
Pump throttled on suction side. This could be caused by:
1.
rubber lining pulling away from the suction pipe and partially collapsing,
2.
large solids dropping into the suction, or
3.
by an improperly sized or-plugged strainer in the suction pipe.
5.
Pump partially plugged by large solid jammed between two impeller blades. This will also cause
rough operation with excessive vibration.
6.
Incorrect pump rotation. When changing motors for any reason or after any electrical system
changes or modifications, always check motors for correct direction of rotation.
7.
Worn pump impeller and/or casing. On a new pump, clearance between tip of impeller blade and
casing or elbow is carefully determined. As this clearance increases, pump performance de-
creases.
It is not practical to predict performance at any given clearance without running a test at this clearance.
On small pumps, this effect is magnified as the percentage of impeller blade area lost from wear and
corrosion is higher.
Other pump conditions and possible causes are:
5.3 Operation
Model AF (42"/1200mm/54"/60"/66") LM/LMR Bearings Installation, Operation, and Maintenance Manual
43