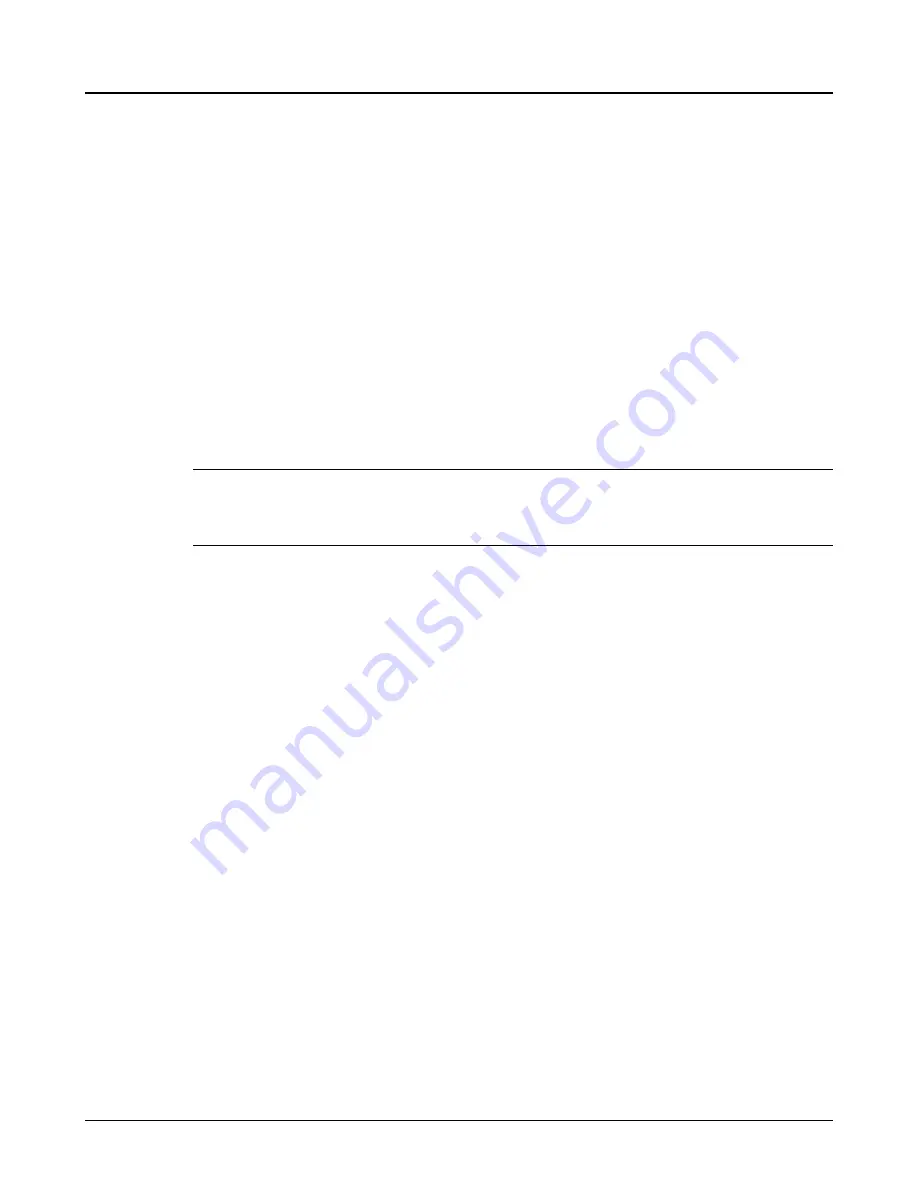
2.
Record the largest gauge size that fits snugly between the two flanges.
3.
Rotate both flanges to position 3 - 180°
4.
Insert a feeler gauge at the periphery of the couplings at position 3.
5.
Record the largest gauge size that fits snugly between the two flanges.
6.
Calculate the difference between the readings at positions 1 and 3. The difference should not be
greater than 0.076mm | 0.003".
7.
Correct any misalignment by shimming under the motor or gearbox feet to attain the proper align-
ment.
When using positions 2 and 4 in steps 1 - 6, correct any misalignment by sliding the motor or
gearbox back and forth to attain the proper alignment.
8.
Repeat steps 1-6 substituting positions 2 and 4 for position 1 and 3 respectively. Use the same
marks made on the coupling from position 1 and be sure to turn the coupling halves together.
Parallel Alignment
The unit is in parallel alignment when indicator “P” (Parallel Indicator) does not vary by more than
0.076mm | 0.003" as measured at four points on the coupling periphery 90° apart at operating tempera-
ture. There are two methods outlined below that are acceptable to achieve the desired alignment.
NOTICE:
Equal amounts of shims must be added to or removed from each driver foot. Otherwise the
vertical angular alignment will be affected.
METHOD I - Dial Indicator Method
For the following steps, refer to Figure:
Directions for viewing coupling (view from front end of pump).
1.
Zero the indicator “P” at position 1 of coupling half (Y). Mark this position on both flanges.
2.
Rotate both flanges 180° to position 3. Observe needle and record reading.
3.
Negative Reading - Coupling half (Y) is shifted toward position 1.
If the value is greater than 0.076mm | 0.003", correct the misalignment by evenly (at equal
amounts on both sides) shimming the motor higher. When using positions 2 and 4 in steps 1 - 2,
correct any misalignment by sliding the motor evenly toward position 2.
Positive Reading - Coupling half (Y) is shifted toward position 3.
If the value is greater than 0.076mm | 0.003" , correct the misalignment by evenly (at equal
amounts on both sides) shimming the motor or gearbox lower. When using positions 2 and 4 in
steps 1 - 2, correct any misalignment by sliding the motor or gearbox evenly toward position 4.
4.
Repeat steps 1-3 until indicator “P” reads 0.076mm | 0.003" or less.
5.
Once the ideal alignment is reached, repeat steps 1-4 substituting position 2 for position 1 and
position 4 for position 3.
METHOD 2 - Straight-Edge Method
For the following steps refer to Figure:
Directions for viewing coupling (view from front end of pump).
1.
Place a straight edge across the two coupling flanges at position 1 and mark the spot on both
flanges.
2.
Adjust the motor or gearbox so that the straight-edge rests evenly on both flanges (within
0.076mm | 0.003").
3.
Rotate both flanges 90° to positions 2 and repeat steps one and two.
4.
The unit will be in parallel alignment when the straight edge rests evenly (within 0.076mm |
0.003") on the coupling periphery at both positions along the periphery.
4.4 Drive Alignment Procedures
Model AF (42"/1200mm/54"/60"/66") LM/LMR Bearings Installation, Operation, and Maintenance Manual
31