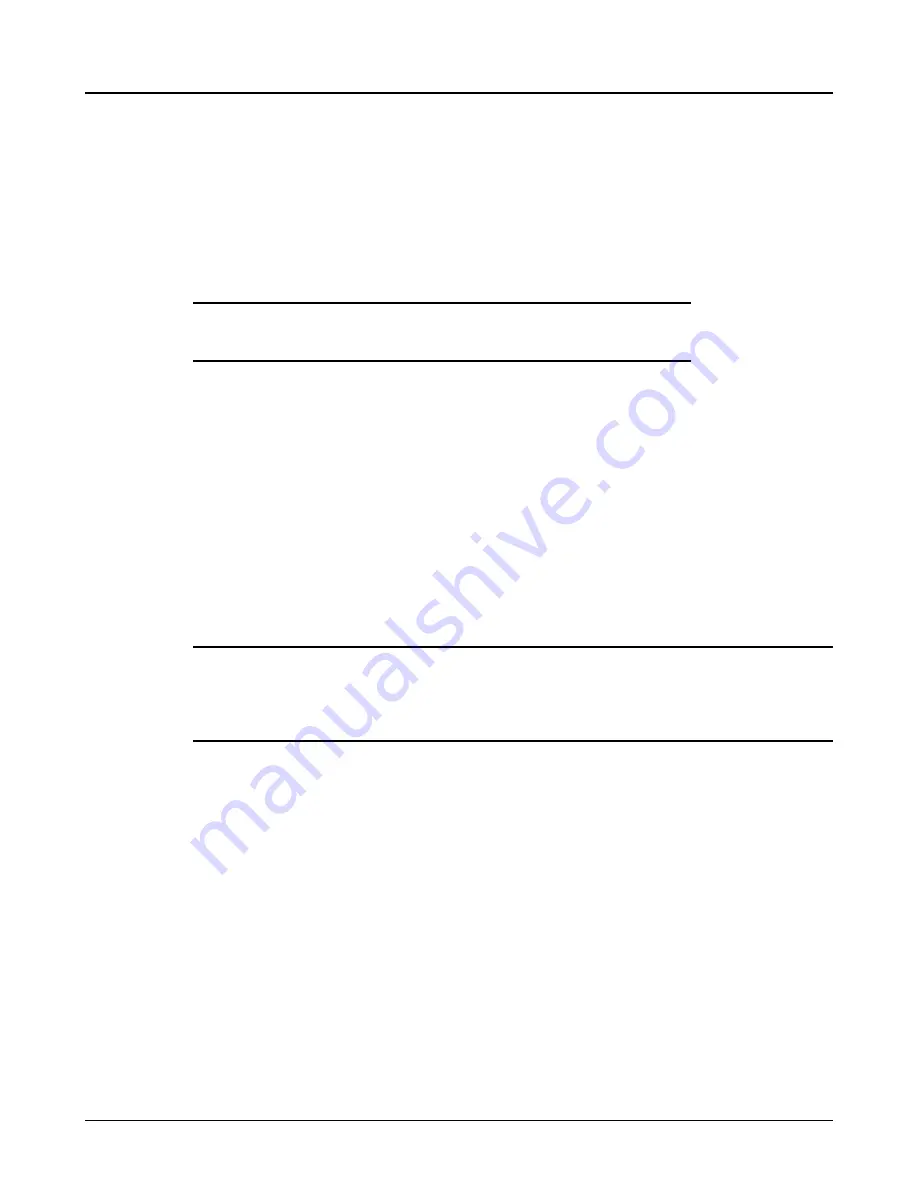
valve prevents pump or seal damage due to reverse flow through the pump when the driver is
turned off.
2.
Increasers, if used, should be placed between pump and check valves.
3.
Cushioning devices should be used to protect the pump from surges and water hammer if quick-
closing valves are installed in system.
Final piping check
1.
Rotate shaft several times by hand to be sure that there is no binding and all parts are free.
2.
Check alignment, per
4.6 Impeller alignment worksheet on page 34
to determine absence of
pipe strain. If pipe strain exists, correct the piping.
NOTICE:
Prior to starting pump, ensure all flush and cooling systems are operating.
4.3 Pipe Hung Installation
Location of Unit
The pump should be located in a clean, dry area free from flooding. The area should provide adequate
space for maintenance and repair, considering complete disassembly and handling of equipment. The
unit should be positioned to provide the most efficient pipeline system.
Piping
Short, direct suction and discharge pipelines having a minimum of elbows and fittings will result in the
least amount of pipe friction. Excessive friction losses will result in insufficient capacity and cavitation.
Future access to the pump impeller and shaft will require removal of a section of discharge pipe (spool
piece).
NOTICE:
The horizontal pipe flange must be parallel with the pump flange before the bolts are tightened.
If the flanges are not parallel, forcing them parallel by tightening the bolts may put excessive
strain on the pump.
Installation of Pump in Pipeline
1.
Connect the pump top flange to the vertical pipe and tighten flange bolts. Level pump with-
in .005"/foot (0.42 mm/meter).
2.
Check the impeller clearance in the casing so that it is reasonably well centered using the criteria
that the minimum gap at the vane.
3.
O.D. is at least 50% of the maximum gap (see the impeller alignment worksheet).
4.
Connect the casing flange to the spool piece and tighten the flange bolts.
Installation of the Driver
1.
Install the driver (motor and reduction gear on a separate sub-base) as indicated on the installa-
tion drawing for the pump. The universal joint drive shaft requires the gear and pump shafts be
parallel within 1 degree but off-set as indicated on the drawing. The optimal universal joint life is
obtained with off-set shaft angles of 1 to 3 degrees.
2.
Level the driver base relative to the pump, in accordance with the proceeding paragraph using
leveling wedges adjacent to the anchor bolts. Partially tighten the anchor bolt nuts and check the
shaft alignment between the motor and reduction gear. If the alignment is reasonably satisfactory,
grout the base in place.
4.3 Pipe Hung Installation
Model AF (42"/1200mm/54"/60"/66") LM/LMR Bearings Installation, Operation, and Maintenance Manual
25