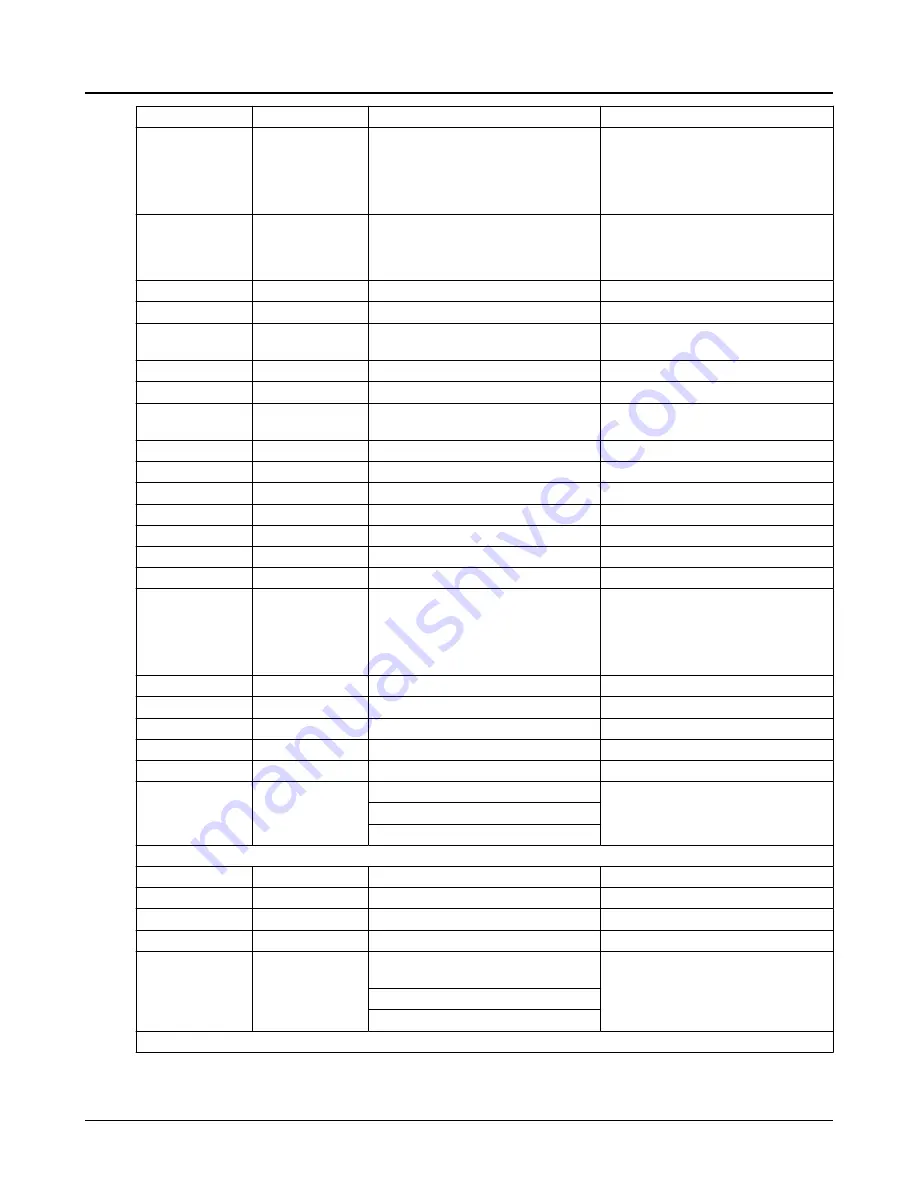
Item
Quantity
Part name
Material
351
1
Backplate-to-case gasket
Optional gasket material:
•
Aramid fiber/EPDM (standard)
•
White gylon (optional)
•
Fawn gylon (optional)
351X
2
Intermediate ring spacer
Optional spacer material:
•
TFM1600 (PTFE) (standard)
•
Viton B (optional)
360A
1
End cover gasket
Vellumiod
360W
1
Frame-to-adapter gasket
Aramid fiber/EPDM
370
8 for 6 in. pumps,
12 for 8 in. pumps
Adapter-to-case hex capscrew
Steel
370B
4
Frame-to-adapter hex capcrew
Steel
370C
1
End cover hex capscrew
Steel
370V
2
Adapter-to-backplate hex capscrew
(8 in. pumps)
Steel
382
1
Internal tooth lockwasher
Stainless steel
370C
4
End cover hex capscrew
Steel
400
1
Coupling key
Steel
408A
1
Drain plug
Steel
412A
1
Impeller nut O-ring
PTFE
444
1
Backplate
Stainless steel (1.4408)
529
1
Wave washer
Steel
540N
1
Containment shell gasket
Optional gasket material:
•
Aramid fiber/EPDM (standard)
•
White gylon (optional)
•
Fawn gylon (optional)
740A
1
Driven carrier assembly
Duplex SS/NdFeB (1.4517)
740B
1
Drive carrier assembly
Ductile iron/NdFeB (0.7043)
750
1
Containment shell
Hastelloy-C (2.4610)
791D
1
Drive-to-shaft capscrew socket head Steel
791E
3
Cartridge-to-backplate hex capscrew Stainless steel
849
1
Bearing cartridge assembly
Duplex SS/SSiC
Silicon Carbide (standard)
Dryguard Silicon Carbide (optional)
High temperature optional components
351
1
Backplate-to-case gasket
Grafoil
540N
1
Containment shell gasket
Grafoil
740A
1
Driven carrier assembly
Duplex SS/SmCo (1.4517)
740B
1
Drive carrier assembly
Ductile iron/SmCo (0.7043)
849
1
High temperature bearing cartridge
assembly
Duplex SS/SSiC
Silicon Carbide (standard)
Dryguard Silicon Carbide (optional)
*Included in 740A driven carrier assembly.
8.3 S-group with bearing frame — stainless steel
Model 3296 EZMAG Installation, Operation, and Maintenance Manual
83
Содержание GOULDS PUMPS 3296 EZMAG
Страница 1: ...Installation Operation and Maintenance Manual Model 3296 EZMAG ...
Страница 2: ......