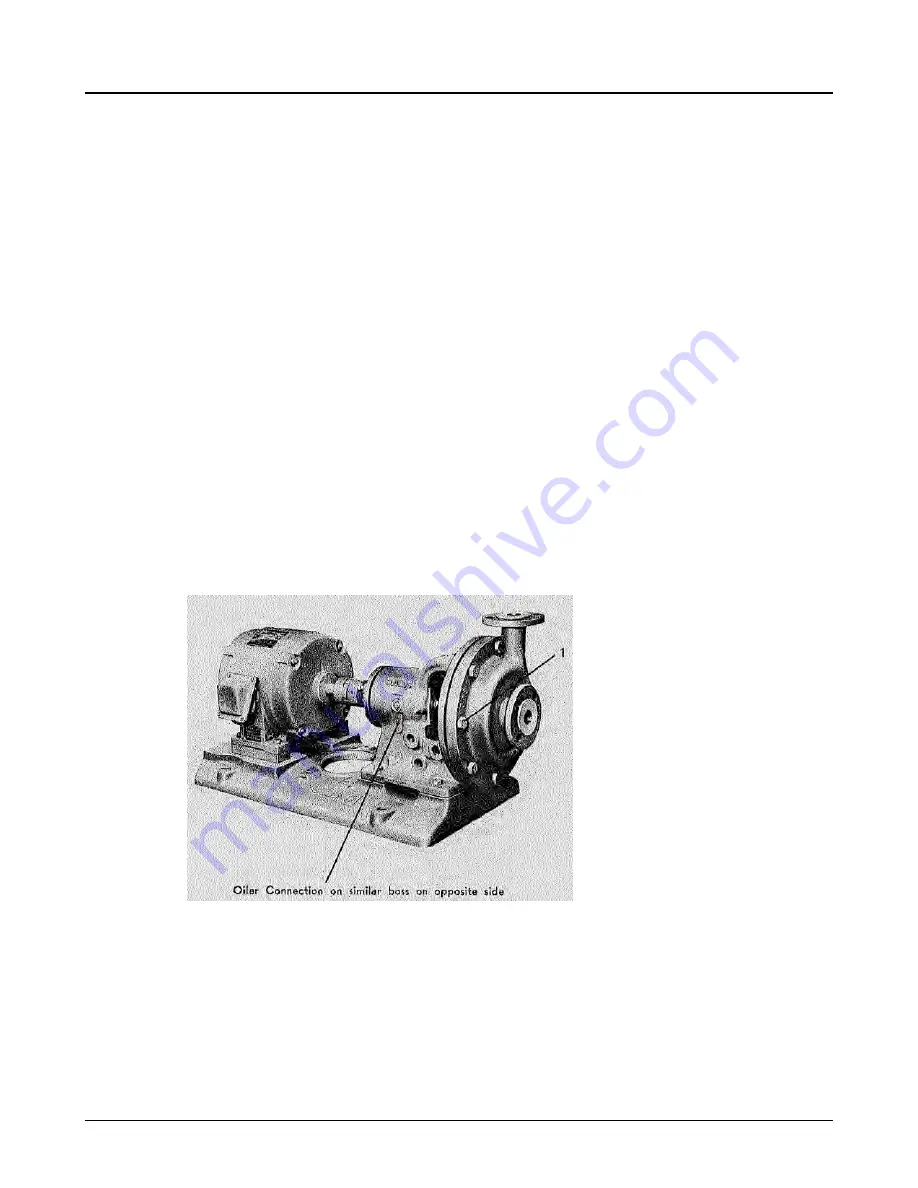
6.2 Impeller adjustment
Some end suction pumps, in addition to vertical pumps, have means of adjusting impeller clearance with-
in the casing. The clearance was set at the factory, but in transit, the clearance may have been lost.
Proper clearance must be attained before a pump is operated or serious damage may occur. Check and
reset impeller clearance by method described in Impeller clearance adjustment.
6.3 Disassembly of pump
To prepare pump for disassembly proceed as follows:
1.
Lock out power supply to motor.
2.
Shut off valves controlling flow to and from pump.
3.
Remove all auxiliary tubing and piping.
4.
Disconnect suction and discharge piping. If pumpage is hazardous or toxic care should be taken
to flush liquid off pump parts.
5.
Disconnect coupling.
6.
Loosen bearing frame hold-down bolts and remove pump from bedplate.
7.
Mark coupling position on shaft and remove pump half coupling hub.
8.
If pump is oil lubricated remove constant level oiler and oil drain plug and drain oil. Pump can
now be moved to the shop for disassembly.
The numbers located on the following figures refer to the procedure steps.
1.
Loosen casing-to drain. Be careful if pumpage is corrosive or toxic. After draining remove bolts
and casing and flush all traces of pumpage from the pump.
Figure 30:
2.
All units contain a mechanical seal. Refer to the order acknowledgement and seal drawing (sup-
plied with pump) to determine seal type. The following instructions are for three basic seal types
available. single outside, PTFE bellows, and inside double seal determine the applicable type
and carefully follow the procedures.
A. Single outside seal
6.2 Impeller adjustment
3107 Installation, Operation and Maintenance Instructions
37