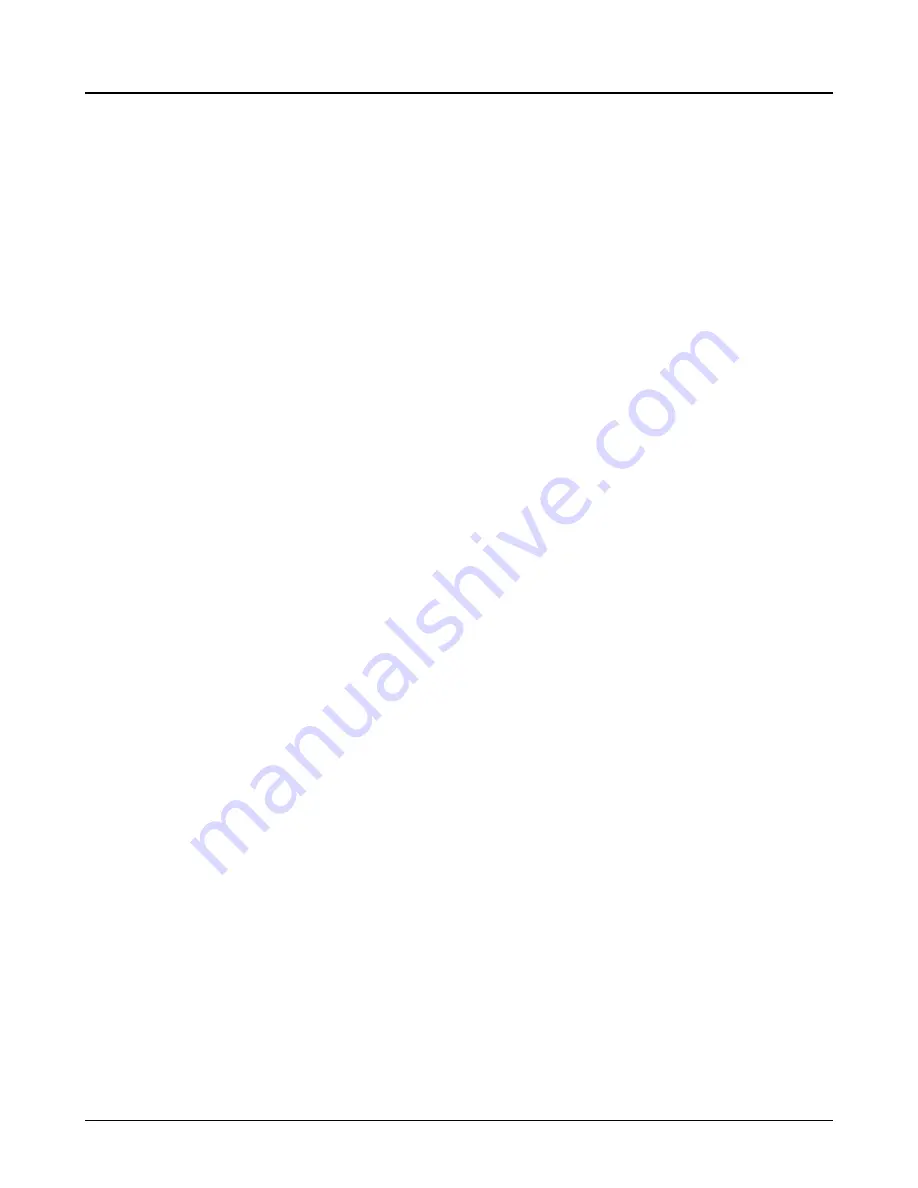
Bearings
Bearing cooling is available on some units. When it is available, cooling water must be connected to the
jacket when pumping hot liquids. See the temperature limits listed under
Construction Details
tional View and Parts List on page 41
. Valves should be installed in the coolant supply lines to regulate
the flow.
Stuffing boxes
Some units are equipped with cooling jackets around the stuffing box as standard. It is optional on vari-
ous other models. Coolant lines are connected in the same manner as the bearing cooling lines.
Casing pedestals
On some models, water cooled pedestals are available. Connection of coolant lines is made in the same
manner as above.
Mechanical seals
Seal materials (carbon, ceramic, PTFE, etc.) are suitable for use at temperatures to 500°F. (212° to
250°F if seal has rubber parts). However, for satisfactory operation, there must be a liquid film between
the seal faces to lubricate them. If the liquid .flashes to vapor, the faces will run dry and be damaged. To
prevent this, the liquid must be cool. In general, this requires that the liquid be cooled so that the vapor
pressure is well below the stuffing box pressure. Doubtful cases should be referred to Goulds for a rec-
ommendation. Refer to seal manufacturer's drawing for location of taps. Some methods which may be
used to cool the seal are:
1.
Dead Ended Seal Chamber
No liquid is circulated through the stuffing box.
The isolated or dead ended liquid around the seal is cooled by circulating water in the stuffing
box jacket, if any.
2.
Cool Liquid Flushing - External Source
A clean, cool compatible liquid is injected from an outside source directly into the seal chamber.
The flushing liquid must be at a pressure 20 to 40 PSI greater than the pressure in the stuffing
box. Onehalf to two GPM should be injected. A control valve and rotometer placed in the inlet line
permits accurate regulation. Cooling water can be circulated through the stuffing box water jacket
(if any) in addition to the external flush.
3.
Cool Liquid Flushing - Product Cooling
In this arrangement, pumped liquid is piped from the pump casing, cooled in an external heat ex-
changer, then injected into the seal chamber. A control valve together with a rotometer and/or a
dial thermometer should be installed in a line from the exchanger to the seal chamber. One-half
to two GPM should be circulated. Cooling water, one to three GPM, should be circulated through
the stuffing box jacket, if any.
3.6 Connection of drain piping
All units contain tapped openings around the stuffing box for draining leakage. On corrosion resistant
units, a drain pan is supplied with a tapped opening. Check the assembly dimension print for size and
location.
3.6 Connection of drain piping
26
3107 Installation, Operation and Maintenance Instructions