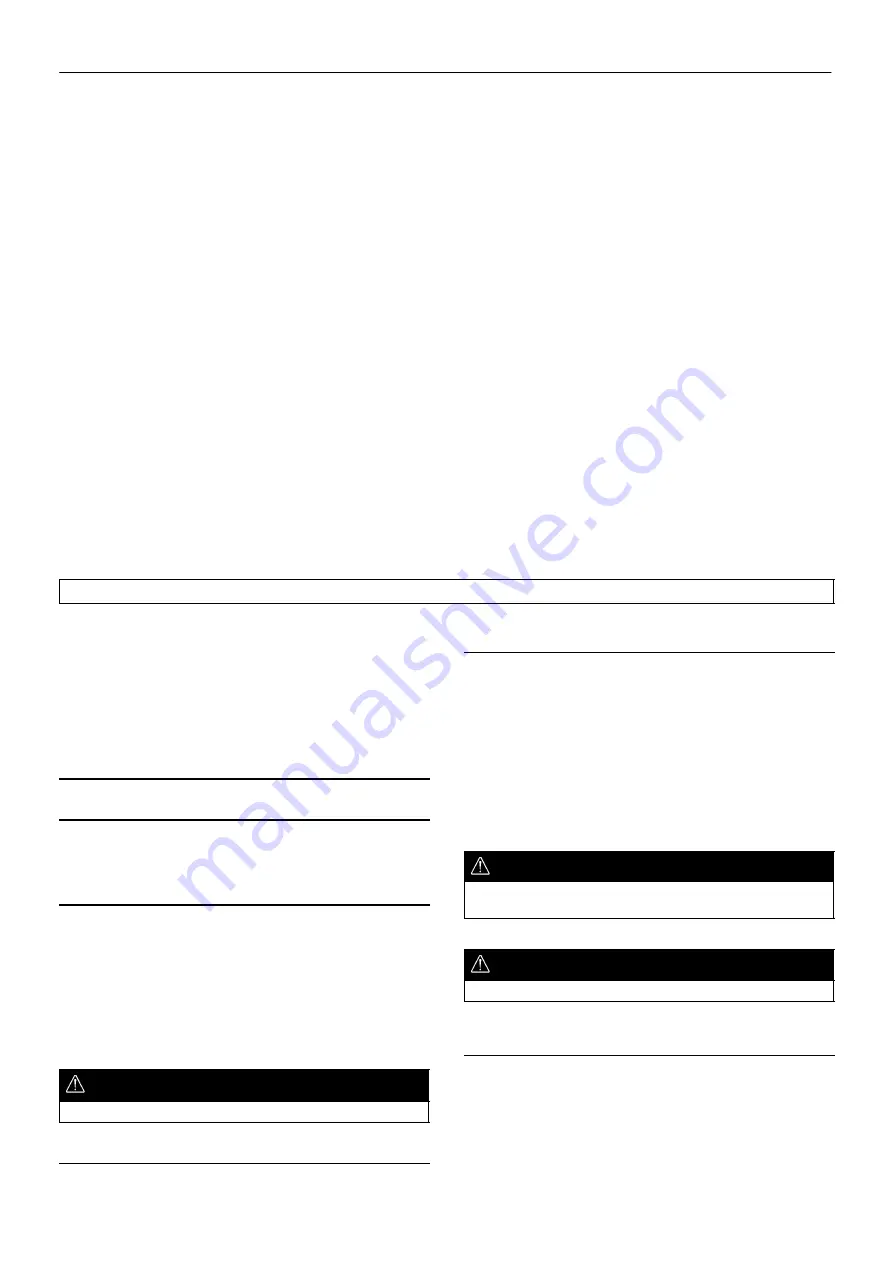
11.0 MAINTENANCE
TS1A–13A
http://air.irco.com
44
Compressed air can be dangerous if incorrectly handled. Before doing
any work on the unit, ensure that all pressure is vented from the system
and that the machine cannot be started accidentally.
Ensure that maintenance personnel are adequately trained, competent
and have read the Maintenance Manuals.
Prior to attempting any maintenance work, ensure that:
S
all air pressure is fully discharged and isolated from the system.
S
the machine cannot be started accidentally or otherwise, by posting
warning signs and/or fitting appropriate anti–start devices.
S
all residual electrical power sources (mains and battery) are
isolated.
Prior to opening or removing panels or covers to work inside a
machine, ensure that:
S
anyone entering the machine is aware of the reduced level of
protection and the additional hazards, including hot surfaces and
intermittently moving parts.
S
the machine cannot be started accidentally or otherwise, by posting
warning signs and/or fitting appropriate anti–start devices.
Prior to opening the refrigeration circuit, ensure that:
S
the refrigeration is recovered by a qualified technician with the
appropriate certifications to handle refrigerants.
S
the appropriate fire control and oil spill equipment is available.
Note: The liquid refrigerant line (condenser–to–evaporator(s) line) is
very likely to contain oil even when the refrigerant is evacuated.
Prior to attempting any maintenance work on a running machine,
ensure that:
S
the work carried out is limited to only those tasks which require the
machine to run.
S
the work carried out with safety protection devices disabled or
removed is limited to only those tasks which require the machine to
be running with safety protection devices disabled or removed.
S
all hazards present are known (e.g. pressurized components,
electrically live components, removed panels, covers and guards,
extreme temperatures, inflow and outflow of air, intermittently
moving parts, etc.).
S
appropriate personal protective equipment is worn.
S
loose clothing, jewelry, long hair etc. is made safe.
S
warning signs indicating that Maintenance Work is in Progress are
posted in a position that can be clearly seen.
Upon completion of maintenance tasks and prior to returning the
machine into service, ensure that:
S
the machine is suitably tested.
S
all guards and safety protection devices are refitted.
S
all panels are replaced, canopy and doors closed.
S
hazardous materials are effectively contained and disposed of.
11.4 ROUTINE MAINTENANCE
This section refers to the various components which require periodic
maintenance and replacement.
For all other maintenance, contact your local Ingersoll Rand office,
Distributor or Air Center.
Refer to safety information and maintenance procedures prior to
carrying out any of the maintenance in the following sections.
Prior to starting
Oil level checking procedure
The oil level should be checked daily. An oil level sight glass is located
at the bottom of the refrigeration compressor and while the machine is
running on load, oil should always be visible in the sight glass. The
normal position is half way.
Adding oil
The refrigeration circuit is hermetically sealed so adding oil should
never be necessary unless the system is leaking or has been pumped
down or recharged.
If adding oil is necessary, do the following.
Run the dryer for a minimum of 2 minutes, the oil level should be visible
in the sight glass. If not, slowly add the proper oil, using the appropriate
pump, to the Schrader
t
valve on the suction connector of the
compressor. Continue until the oil level is visible in the sight glass with
the compressor running.
CAUTION
Do not mix oil types. Use only oil specified by IR
Panel filter change procedure
S
Remove the panel filter by pulling up and out of its slots.
S
Fit the new element in.
Aircooled Condenser Cleaning
Ensure that the dryer is isolated from the compressed air system and
is vented of all pressure. When undertaking any work on the dryer
always use certified lifting equipment and employ sound working
principles.
Ensure that the main power disconnect switch is locked off and tagged.
Visually check the outside of the condenser core to be certain that a
complete cleaning of the condenser is required. Frequently, dirt, dust
or other foreign material may only need to be removed to remedy the
problem.
Acceptable methods of cleaning include vacuuming or compressed air.
WARNING
Do not use steam or water to clean the condenser, since the electrical
panel is NOT water tight.
WARNING
Strong cleaners can harm aluminum cooler parts.
Timed Solenoid Drain Valves (where fitted) Check / Cleaning
S
Remove the central nut and then the electrical coil.
S
Remove screws holding bonnet of valve and carefully split the
valve. Clean and inspect all internal parts.
S
Similarly check and clean the ball valve and needle valve.
S
Replace any defective parts as identified in parts manual.
S
Re–assemble and later, with machine running, check that
condensate and air is expelled at the frequency and duration set into
the INTELLISYS controller.
Содержание TS10A
Страница 2: ......
Страница 10: ...5 0 SAFETY TS1A 13A http air irco com 8 5 3 TEXT DECALS NORTH AMERICA ...
Страница 50: ......
Страница 52: ......
Страница 60: ...5 0 SECURITE TS1A 13A http air irco com 8 5 3 DÉCALCOMANIES DES TEXTES AMÉRIQUE DU NORD ...
Страница 101: ......
Страница 102: ......
Страница 104: ......
Страница 112: ...5 0 SEGURANÇA TS1A 13A http air irco com 8 5 3 AUTOCOLANTES DE TEXTO AMÉRICA DO NORTE ...
Страница 152: ......
Страница 161: ...5 0 SEGURIDAD TS1A 13A http air irco com 8 5 3 CALCOMANÍAS DE TEXTO AMÉRICA DEL NORTE ...
Страница 203: ......
Страница 204: ......