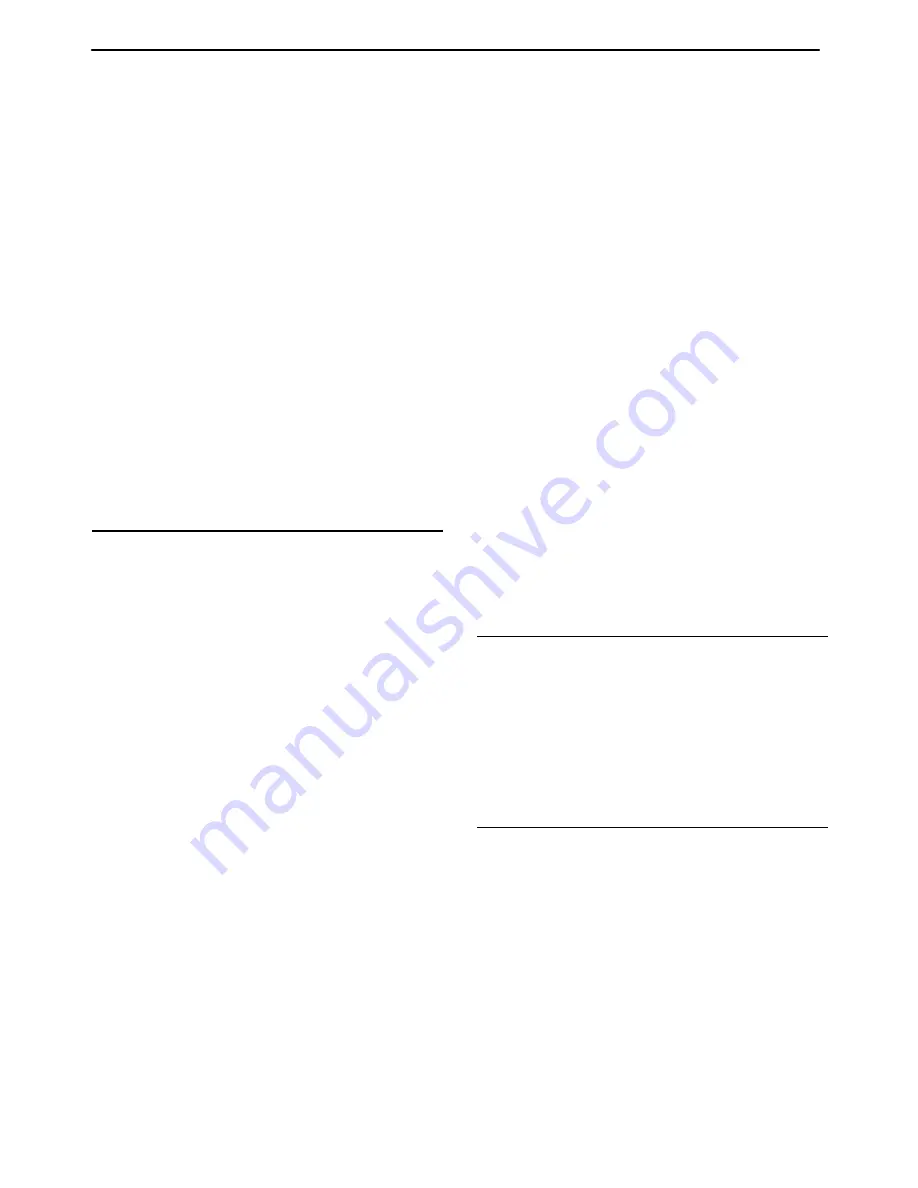
33
( )
Book 54757919 (5/02)
Bare Airend -- Pertains to major airend parts (rotors,
housings, and bearings).
Airend Components -- Pertains to auxiliary
attachments to the bare airend (drive coupling,
seals, pumps, valves, tubes, hoses, fittings and filter
housing).
The compressor oil must be replaced every 1000
hours of operation or six (6) months, whichever
comes first.
Refer to the fluids and lubricants chart for ambient
temperature ranges and specifications, in the
lubrication section of this manual.
Refer to the fluids and lubricants chart for ambient
temperature ranges and specifications in the
lubrication section of this manual.
AIR CLEANER
This unit is equipped with an AIR FILTERS
RESTRICTED lamp on the instrument panel.
When this message is viewed, both the engine and
airend filters should be replaced.
Also, each week, squeeze the rubber valve
(precleaner dirt dump) on each air cleaner housing
to ensure that they are not clogged.
NOTICE: Holes or cracks downstream of the air
cleaner housing will cause the restriction indicators
to be ineffective.
To service the air cleaners on all units proceed as
follows:
1.
Loosen outer wing nut and remove with
outer element. Inspect red window on
special inner wing nut to find small dot. If dot
is not visible, remove cotter pin and special
wing nut and inner (safety) element.
2.
Inspect air cleaner housing for any condition
that might cause a leak and correct as
necessary.
3.
Wipe inside of air cleaner housing with a
clean, damp cloth to remove any dirt
accumulation, especially in the area where
the element seals against the housing.
4.
If a new air filter element is to be used check
it closely for shipping damage. To reset the
signal indicator in the special wing nut, apply
suction to the red window.
5.
Install cleaned or new elements in the
reverse order to the above. Tighten wing
nuts firmly and replace cotter pin.
6.
Inspect to ensure that the end cap seals
tightly 360 degrees around the air cleaner
body.
The air cleaner system (housing and piping) should
be inspected every month for any leakage paths or
inlet obstructions.
Make sure the air cleaner
mounting bolts and clamps are tight. Check the air
cleaner housing for dents or damage which could
lead to a leak. Inspect the air transfer tubing from the
air cleaner to the compressor and the engine for
holes. Make sure that all clamps and flange joints
are tight.
GAUGES
The instruments or gauges are essential for safety,
maximum productivity and long service life of the
machine.
Inspect the gauges and test any
diagnostic lamps prior to start--up. During operation
observe the gauges and any lamps for proper
functioning. Refer to Operating Controls for the
normal readings.
FUEL TANK
This unit is equipped with dual tanks that can be filled
from either side. Using clean fuel in the fuel tanks is
important and every precaution should be taken to
ensure that only clean fuel is either poured or
pumped into the tank. When filling the fuel tank on
this unit, by methods other than a pump and hose,
use a CLEAN non--metallic funnel.
Содержание HP1300WCU
Страница 57: ...57 Book 54757919 5 02 Replace this sheet with 11 x 17 System Schematic Sheet 1 of 5...
Страница 58: ...58 Book 54757919 5 02 Replace this sheet with 11 x 17 System Schematic Sheet 2 of 5...
Страница 59: ...59 Book 54757919 5 02 Replace this sheet with 11 x 17 System Schematic Sheet 3 of 5...
Страница 60: ...60 Book 54757919 5 02 Replace this sheet with 11 x 17 System Schematic Sheet 4 of 5...
Страница 61: ...61 Book 54757919 5 02 Replace this sheet with 11 x 17 System Schematic Sheet 5 of 5...
Страница 75: ...75 Book 54757919 5 02 54699657 Deutsch Terminal Removal Tool 54749643 Packard Metri Pack Removal Tool...