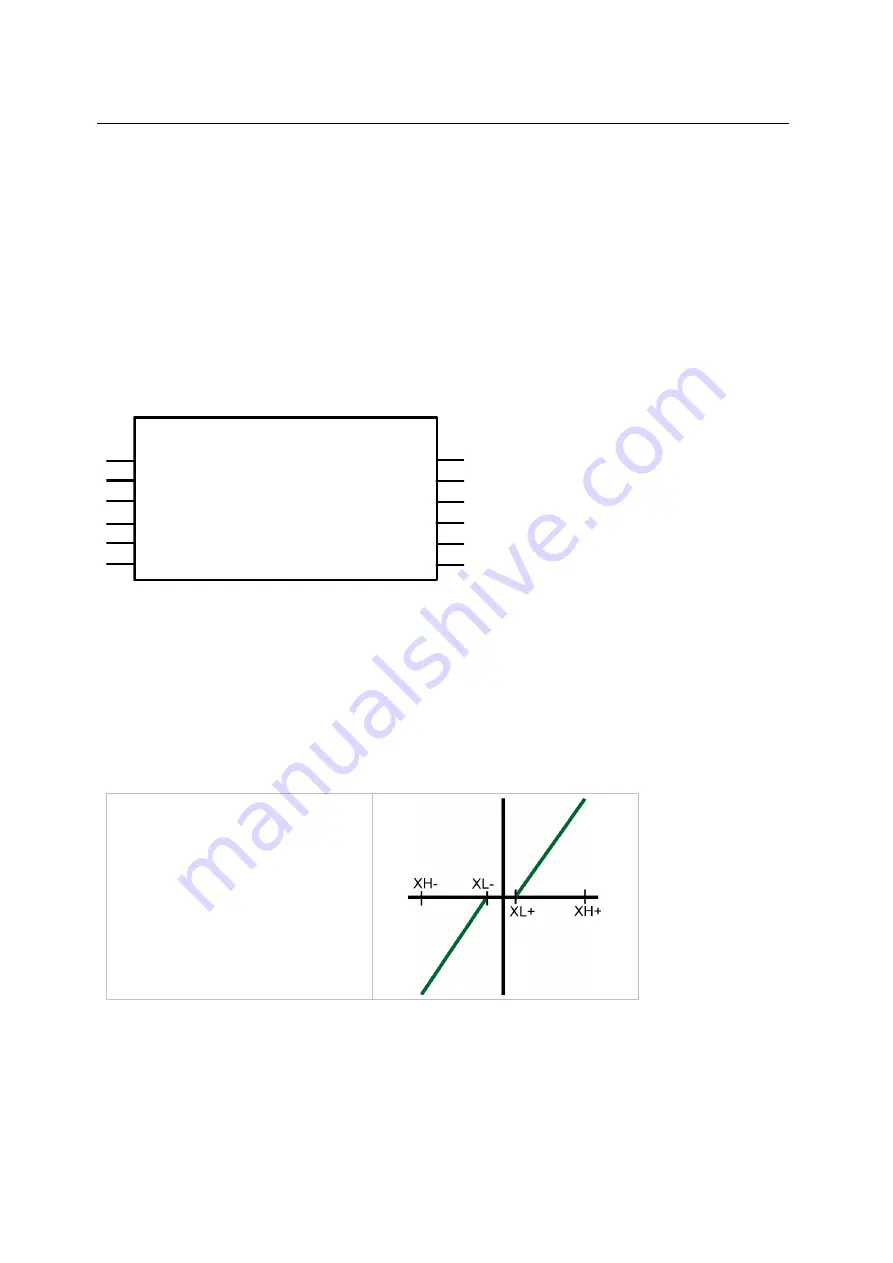
186
ifm
System Manual
ecomat
mobile
SmartController (CR2500) V05
PWM in the ecomatmobile controller
Hydraulic control in PWM
9.3.6
Function JOYSTICK_0
Contained in the library:
ifm_HYDRAULIC_16bitOS05_Vxxyyzz.Lib
Available for the following devices:
•
ClassicController: CR0020, CR0505
•
ExtendedController:
CR0200
•
SafetyController: CR7020, CR7021, CR7200, CR7201, CR7505, CR7506
•
SmartController:
CR2500
Function symbol:
JOYSTICK_0
X
OUT1
XH_POS
OUT2
ERR1
ERR2
XL_POS
OUT3
XH_NEG
WRONG_MODE
XL_NEG
MODE
Description
JOYSTICK_0 scales signals from a joystick to clearly defined characteristic curves, standardised
to 0...1000.
For this function the characteristic curve values are specified (
→
figures):
•
Rising edge of the ramp = 5 increments/PLC cycle
•
Falling edge of the ramp = no edge
The parameters XL_POS (XL+),
XH_POS (XH+), XL_NEG (XL-) and
XH_NEG (XH-) are used to evaluate
the joystick movements only in the
requested area.
The values for the positive and
negative area may be different.
The values for XL_NEG and XH_NEG
are negative here.
Содержание Ecomat Mobile Series
Страница 1: ...System Manual SmartController CR2500 CoDeSys V2 3 Target V05 7390675 00 10 2009...
Страница 6: ......