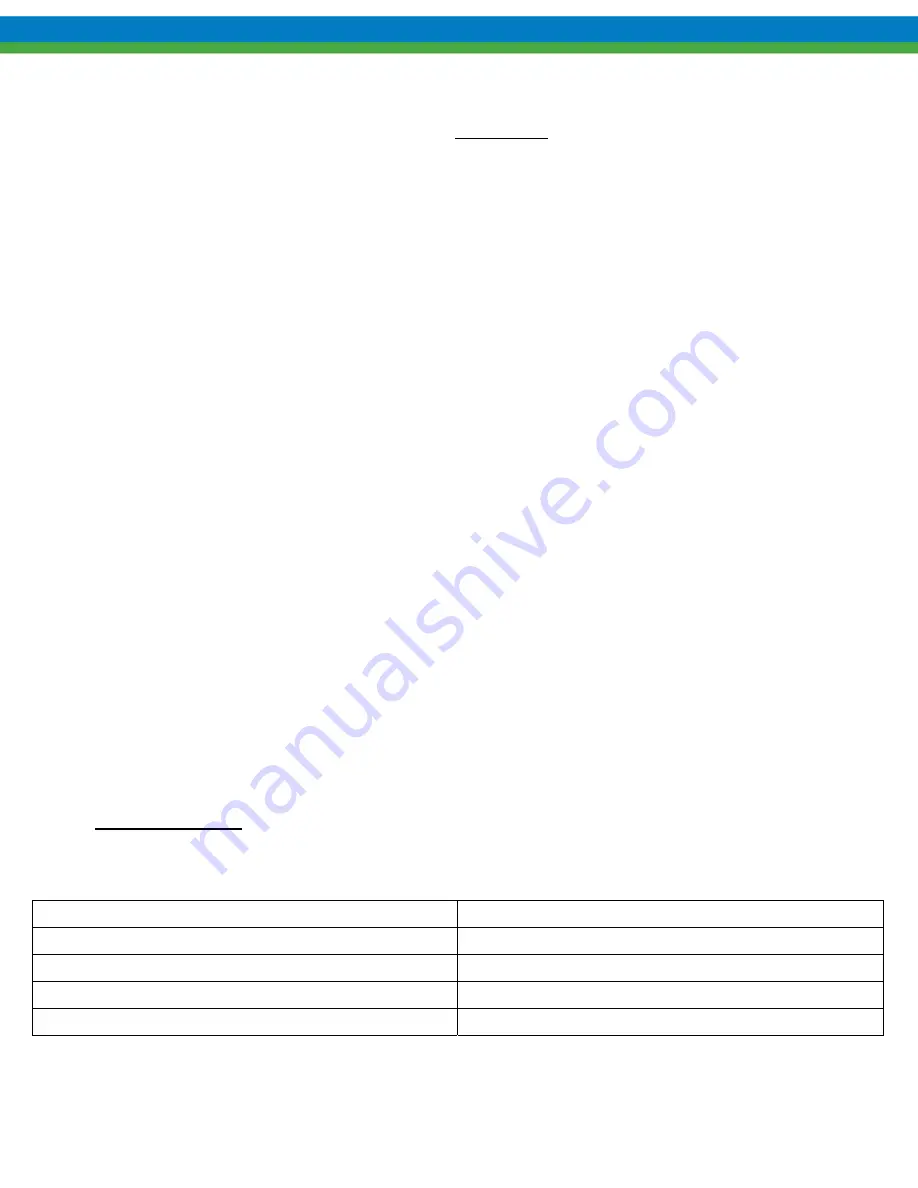
71
14. Pump Motor Selection
Your MPC VECTOR pump controller can accept
input power
in the at frequency ranges of both 50 and 60
Hz power. This allows your controller to be run from 50 and 60 Hz line frequency locales. Your motor supply
frequency may be 50 or 60 Hz and is independent of your supply input frequency as the motor’s input supply
frequency is generated by the AC drive. Maximum synchronous motor speed (derived from the frequency of
operation); however, will directly affect your pump flow capacity (maximum flow rate). In general, 60 Hz motors
will have a theoretical synchronous speed of 1800 RPM while 50 Hz motors will be 1500 RPM. The speed
difference theoretically results in a pump capacity reduction of approximately 17%.
14.1 General
Specifications
All motors used with the MPC VECTOR controller must meet these minimum specifications:
50 or 60 Hz 3-phase input power AC induction motor
o
208/230 VAC for 208/240 VAC Input Voltages
o
400/460 VAC for 400/480 VAC Input Voltages
1800 rpm (60 Hz) or 1500 rpm (50 Hz) synchronous speed
Service Factor 1.05 or greater
Class F Insulation (minimum)
Refer to your equipment specifications and documentation for the correct frame size
Motors may or may not need feet and/or a C-face mount depending on equipment
14.2
Motor Type and Turndown Requirements
Motor turndown is defined by the ratio of motor base speed to the slowest speed used in the pump application. Pump application
specifics will determine the motor type and turndown required to drive your pump.
Motor turndown ratings are dependent on the application and intended use of the pump. Users should understand and take into
account the following factors when considering motor selection:
Application required turndown ratio
Motor Cooling
Length of wiring between the MPC VECTOR controller and the pump (motor)
Application Turndown
Shown below are the typical motor types and recommended maximum turndowns. The user must ensure that the positive
displacement pump application can operate over the turndown range (that is max flow to turndown flow) effectively in order to fully
utilize the turndown range of the motor. Shown below are the typical motor types and recommended maximum turndowns.
Motor Type
Typical Turndown
Commercial Duty Motor
2:1
Premium Efficiency Motor (Inverter Ready) *
4:1 – 10:1
Inverter Duty Motor*
Up to 15:1
Vector Duty Motor
Up to 20:1
*All motors must be inverter ready per NEMA Standard MG1 Part 31, failure to comply may result in premature motor winding
breakdown and motor failure.
Содержание Pulsafeeder MPC Vector
Страница 6: ......
Страница 14: ...8 Figure 1 3 Closed Loop Control Feedback Block Diagram Figure 1 4 Closed Loop Flow Calibration Curve...
Страница 43: ...37 This page is intentionally left blank...
Страница 73: ...67 Continues next page...
Страница 80: ...74 16 Menu Maps...
Страница 81: ...75...
Страница 82: ...76...
Страница 83: ...77...
Страница 84: ...78...
Страница 85: ...79...
Страница 86: ...80...
Страница 87: ...81...
Страница 88: ...82...
Страница 89: ...83...
Страница 90: ...84...
Страница 91: ...85...
Страница 92: ...86...
Страница 93: ...87...
Страница 94: ...88...
Страница 95: ...89...
Страница 96: ...90...
Страница 97: ...91...
Страница 105: ...99 Figure 8 Handheld Remote...
Страница 112: ......
Страница 113: ......
Страница 114: ...and Keypad Functionality BULLETIN No IOM MPCVector UMPC 11 201010 Rv A...