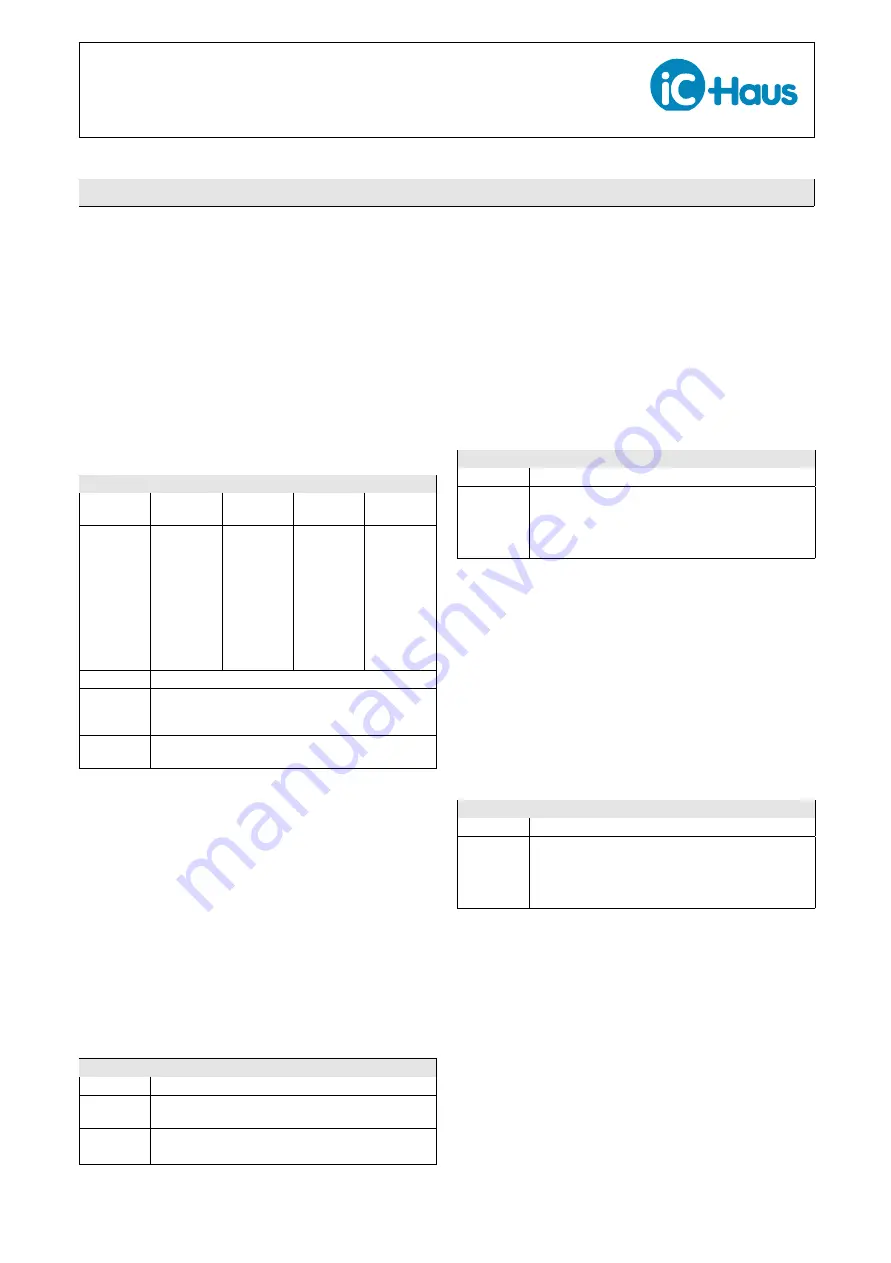
preliminary
preliminary
iC-PVS
LINEAR/OFF-AXIS
BATTERY-BUFFERED ABSOLUTE POSITION HALL SENSOR
Rev A2, Page 31/51
MAGNETIC SIGNAL CONDITIONING
POLEWID: Pole Size of Magnetic Scale
iC-PVS is able to scan magnetic wheels or linear scales
with a pole width of 0.5 mm to 2.5 mm. This corresponds
to a magnetic period (N-S sequence) of 1 to 5 mm. The
measurement is highly tolerant to external common
mode magnetic fields. This allows the usage for direct
gear tooth sensing with back-bias magnets. In Table 28
the configuration for different magnetic pole widths and
gear tooth modules is given.
POLEWID(3:0)
Addr. 0x09; bit 3:0
reset: 0x0
Code
Pole
Width
Period
Width
Gear Tooth
Module
Module
Ideal Width
0x0
0.50 mm
1.0 mm
0.3
0.94 mm
0x1
0.75 mm
1.5 mm
0.5
1.57 mm
0x2
1.00 mm
2.0 mm
—
—
0x3
1.25 mm
2.5 mm
0.7/0.8
2.51 mm
0x4
1.50 mm
3.0 mm
1.0
3.14 mm
0x5
1.75 mm
3.5 mm
—
—
0x6
2.00 mm
4.0 mm
—
—
0x7
*
2.50 mm
5.0 mm
1.5
4.71 mm
0x8-0xF
Reserved
Note:
Changes to parameter POLEWID are only effective
after a REBOOT or CONF_READ_SENSOR
command (0x4F)
*
Note:
Setting POLEWID = 0x7 is not functional in chip
revision iC-PVS X or prior revisions. Do not use.
Table 28: Pole Size of Magnetic Scale and usability for
gear tooth applications
DCCOMP: High Magnetic Field Strength Compen-
sation
iC-PVS can tolerate the presence of high DC magnetic
fields. Nevertheless, for the analog output stage it may
be necessary to reduce the signal gain at very high
DC magnetic fields. Please set DCCOMP according to
DCCOMP
Addr. 0x09; bit 5
reset: 0
Code
Application Type and Magnetic Field Range
0
All common magnetic disc or wheel applications
without backbias magnet
0
Backbias magnet; Field range - 180 ... + 180 kA/m
1
Backbias magnet; Field range - 380 ... + 380 kA/m
Table 29: High Magnetic Field Strength Compensation
LOWPOW: Low Power Mode
When iC-PVS is powered via VDD the magnetic signal
acquisition can run in four different power modes. In de-
fault mode, the maximum permissible input frequency
is equal to f
mag
defined in Elec. Char. 106. Additional
power safe modes are available to reduce the power
consumption of the analog stage. This reduces the per-
missible magnetic input frequency according to Table
30.
LOWPOW(1:0)
Addr. 0x0D; bit 3:2
reset: 00
Code
Mode
00
No power optimization, input frequency = f
mag
01
Low power mode level 1, input frequency = f
mag
/2
10
Low power mode level 2, input frequency = f
mag
/4
11
Low power mode level 3, input frequency = f
mag
/8
Table 30: Low Power Mode
NOMAG: Behaviour of NoMagnet Detection
The magnetic field amplitude is monitored and on de-
tection of magnet loss the NoMagnet working state
(NOMAG_ST) is entered in order to save battery power.
Status Bit MAG_ERR is set as long as the NoMagnet
working state is active. The NoMagnet detection can
be disabled by parameter NOMAG = 0x3 (Table 31).
NOMAG(1:0)
Addr. 0x0A; bit 7:6
reset: 0x0
Code
Condition
0x0
NoMagnet detection active
0x1
Reserved
0x2
Reserved
0x3
NoMagnet detection disabled
Table 31: Behaviour of NoMagnet Detection
The error bit NOMAG_L is latched and set upon entry
of the NoMagnet working state. It can be be cleared
by a pin preset or using the status clear (SCLEAR) or
reboot command.
MAG_THR: Magnetic Field Amplitude Working
Threshold
The error bit AMPL_ERR is set whenever the magnetic
field amplitude is below the working threshold defined
in Elec. Char. 109. Table 32 shows the configuration
options.