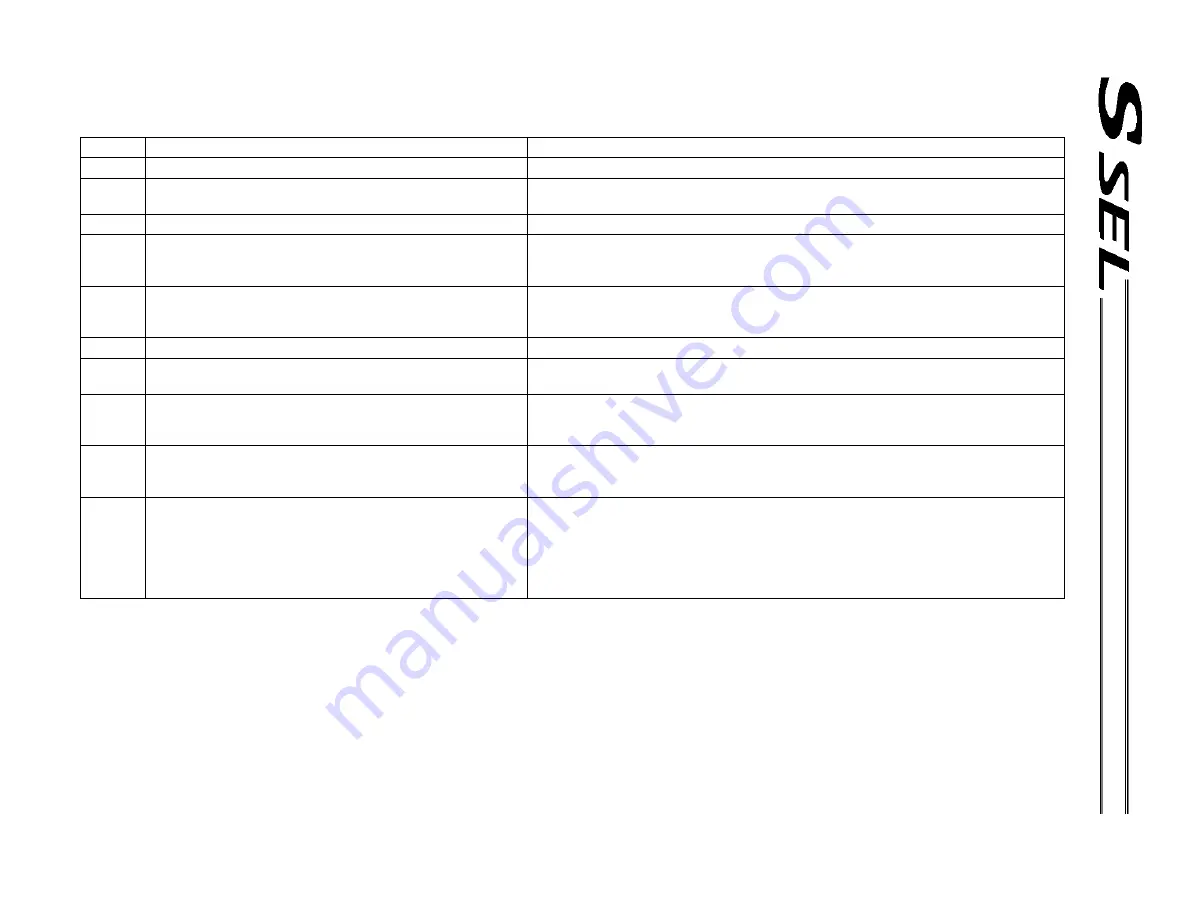
429
Appendi
x
(In the panel window, the three digits after “E” indicate an error number.)
Error No.
Error name
Description, action, etc.
406
Flash busy reset timeout
Error erasing/writing the flash ROM
407
Control constant table management information mismatch
error
The management information regarding the control constant table is invalid. If this error
occurs when the controller is started, the control constant table may need to be updated.
408
Control constant table ID error
The control constant table ID is invalid.
409
Encoder control constant error (power-source voltage control)
An encoder control constant relating to power-source voltage control is invalid. The
encoder power-source voltage cannot be adjusted (the encoder power will be supplied
without voltage adjustment).
40A
Encoder power-source voltage calculation error
The encoder power-source voltage cannot be adjusted (the encoder power will be
supplied without voltage adjustment). Check the “motor/encoder configuration
information” in driver parameter No. 26 and encoder parameter No. 11.
40B
Speed control parameter calculation error
Check driver parameter Nos. 38, 39, 40, 43, 44, 45, etc.
420
Stationary (non-push) torque limit over error
The stationary (non-push) torque limit is exceeded. The load or operation may have
been locked or other event occurred unexpectedly.
422
Multi-slider command position near-miss error
Entry into the multi-slider servo command-position near-miss range has been detected.
Jog the applicable actuator or otherwise pull it out of the near-miss position, and then
perform the next operation.
423
Multi-slider actual position near-miss error
Entry into the multi-slider servo current-position near-miss range has been detected. Jog
the applicable actuator or otherwise pull it out of the near-miss position, and then
perform the next operation.
443
Current position output specification error
An invalid output port specification was detected when the OTPS command was
executed.
Check if an output port on the network is used.
Check for duplication with a system output function or other output port for which zone
output is specified.
Check for duplication with the current position output port for other axis.
Содержание ssel
Страница 1: ...Operation Manual Eighth Edition SSEL Controller ...
Страница 26: ......
Страница 50: ...25 Part 1 Installation 3 Specification with system memory backup battery optional ...
Страница 385: ...359 ...
Страница 495: ......
Страница 496: ......