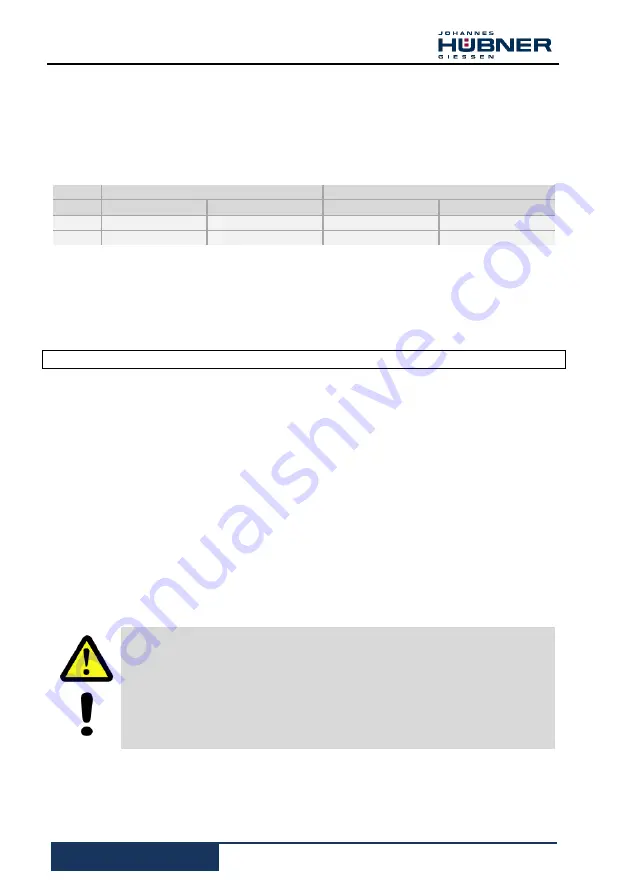
46
AMP(H)41_MANUAL-en_R11 - 2019-03-28
Absolute Encoder AMP(H) 41
If the measured speed exceeds the display range of –32768…+32767, this results in an
overflow, which is reported in the cam register via bit 2
0
. At the time of the overflow the speed
stops at the resp/- maximum value, until the speed is once again in the display range.
In this case the message in the cam register is also cleared.
The speed is specified in
increments
per
Integration time Unsafe
.
6.6.4.1.3
Multi-Turn / Single-Turn
Multi-Turn, Integer16
Single-Turn, Integer16
Byte
X+4
X+5
X+6
X+7
Bit
15 – 8
7 – 0
15 – 8
7 – 0
Data
2
15
– 2
8
2
7
– 2
0
2
15
– 2
8
2
7
– 2
0
As only 16-bit registers have previously been possible on the control side, the position value
must be calculated first. The number of revolutions is noted in the
Multi-Turn
register, and
the current Single-Turn position is noted in steps in the
Single-Turn
register. Together with
the measuring system resolution, max. number of steps per revolution according to type plate,
the actual position can then be calculated:
Position in steps =
(steps per revolution * number of revolutions)
+ Single-Turn position
Steps per revolution:
8192
≙
13 Bit
Number of revolutions:
0…32767
≙
15 Bit
The output position does not have a preceding sign.
6.7
Parameterization
Parameterization means providing a PROFIBUS-DP slave with certain information required for
operation prior to commencing the cyclic exchange of process data. The measuring system
requires e.g. data for the integration time, counting direction etc.
Normally the configuration program provides an input box for the PROFIBUS-DP master with
which the user can enter parameter data or select from a list. The structure of the input box is
stored in the device master file. The number and type of parameters entered by the user
depend on the configuration.
DANGER!
NOTICE!
Danger of death, serious physical injury and/or damage to property due to
malfunction, caused by incorrect parameterization!
The system manufacturer must ensure correct functioning by carrying out a
protected test run during commissioning and after each parameter change.
Содержание AMP 41
Страница 96: ...96 AMP H 41_MANUAL en_R11 2019 03 28 Absolute Encoder AMP H 41 16 3 T V certificate...
Страница 97: ...Absolute Encoder AMP H 41 AMP H 41_MANUAL en_R11 2019 03 28 97 16 4 PROFIBUS DP certificate...
Страница 98: ...98 AMP H 41_MANUAL en_R11 2019 03 28 Absolute Encoder AMP H 41 16 5 PROFIsafe certificate...