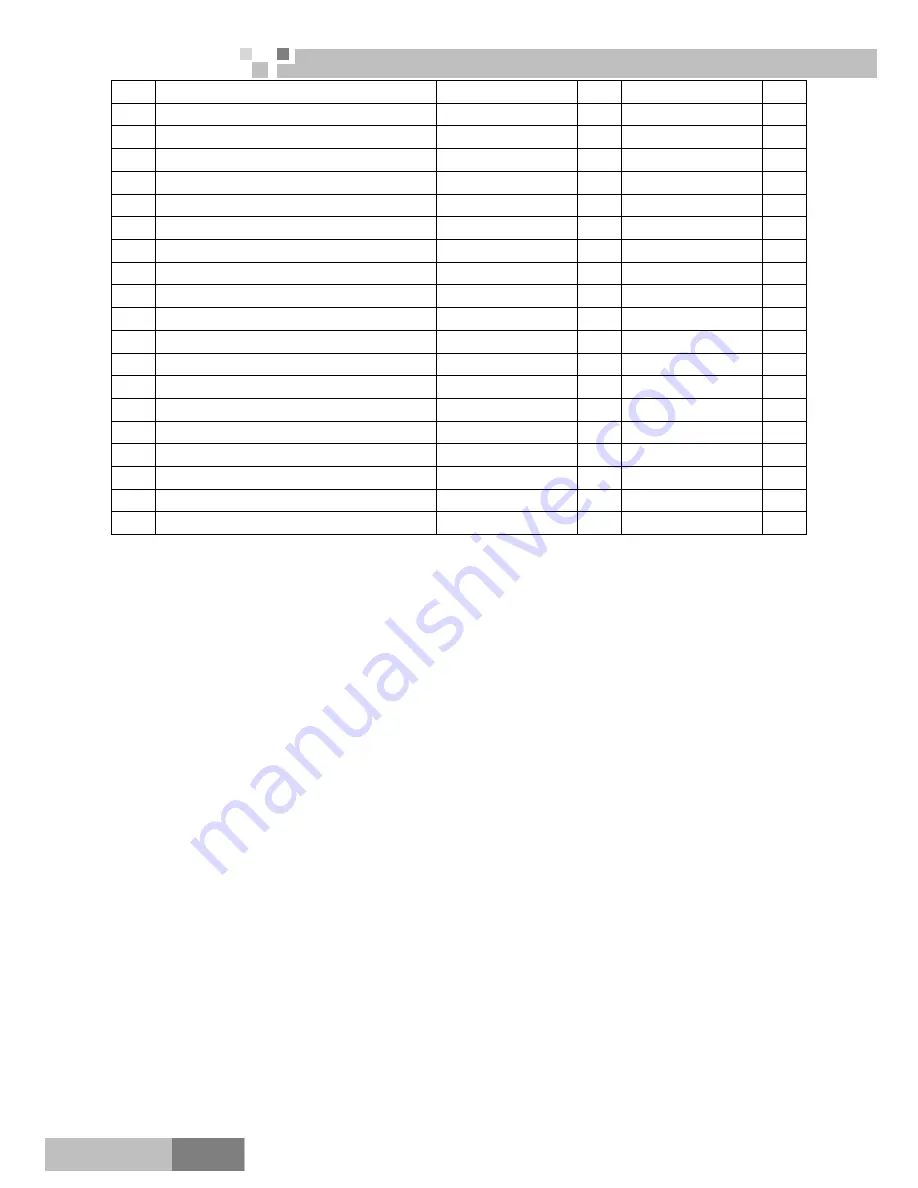
Super Free Match
Service Manual
MAINTENANCE
176
42
Nozzle for Adding Freon
06120012
2
06120012
2
43 Low
pressure
sensor
322101001
1
322101001
1
44
Electronic Expansion Valve Sub-assy
43044100022
1
43044100022
1
45
Check
Valve
07130101 1 07130101 1
46
Capillary Sub-assy (oil returning)
04004100011
1
04004100011
1
47 Pressure
regulating
valve 07334100002
1
07334100002
1
48
Electromagnetic
Valve
43000054 1 43000054 1
49
Magnet
Coil
4304000415 1 4304000415 1
50
Electronic Expansion Valve
07334412
1
07334412
1
51
Electronic Expansion Valve Coil
4304413205
1
4304413205
1
52
Electronic Expansion Valve
43042800005
1
43042800005
1
53
Electronic Expansion Valve Coil
4304413208
1
4304413208
1
54 Sub-cool
Copper
Assy 04534100044
1
04534100044
1
55 Filter
Board 30224100002
1
30224100002
1
56
Terminal
Board
42011204 1 42011204 1
57
Terminal
Board
42011154 0 42011154 0
58 Testing
Board 30118000003
1
30118000003
1
59 Main
Board 30226000039
1
30226000043
1
60 Radiator 49018000053
1
49018000053
1
61 Driving
Board 30118000015
1
30118000015
1
Содержание R410A
Страница 1: ...SUPER FREE MATCH SERIES SERVICE MANUAL T1 R410A 50Hz GC201306 CENTRAL AIR CONDITIONERS ...
Страница 5: ...Super Free Match Service Manual PRODUCT 1 PRODUCT ...
Страница 28: ...Super Free Match Service Manual CONTROL 24 CONTROL ...
Страница 29: ...Super Free Match Service Manual CONTROL 25 Control 1 OPERATION FLOWCHART ...
Страница 31: ...Super Free Match Service Manual CONTROL 27 1 2 Heating Operation ...
Страница 66: ...Super Free Match Service Manual INSTALLATION 62 INSTALLATION ...
Страница 97: ...Super Free Match Service Manual INSTALLATION 93 ...
Страница 118: ...Super Free Match Service Manual INSTALLATION 114 7 Electrical Wiring Work 7 1 Wiring Connection Precept 1 Precept 2 ...
Страница 129: ...Super Free Match Service Manual MAINTENANCE N 125 MAINTENANCE ...
Страница 152: ...Super Free Match Service Manual MAINTENANCE 148 5 Console GEH 09 AA K3DNA1C I GEH 12 AA K3DNA1C I GEH 18 AA K3DNA1C I ...
Страница 153: ...Super Free Match Service Manual MAINTENANCE N 149 4 2 3 BU module FXB3A K ...
Страница 154: ...Super Free Match Service Manual MAINTENANCE 150 FXB5A K ...
Страница 203: ...Super Free Match Service Manual MAINTENANCE N 199 7 2 3 Cassette type GKH 12 BA K3DNA2A I GKH 18 BA K3DNA2A I ...
Страница 217: ...JF00301896 ...