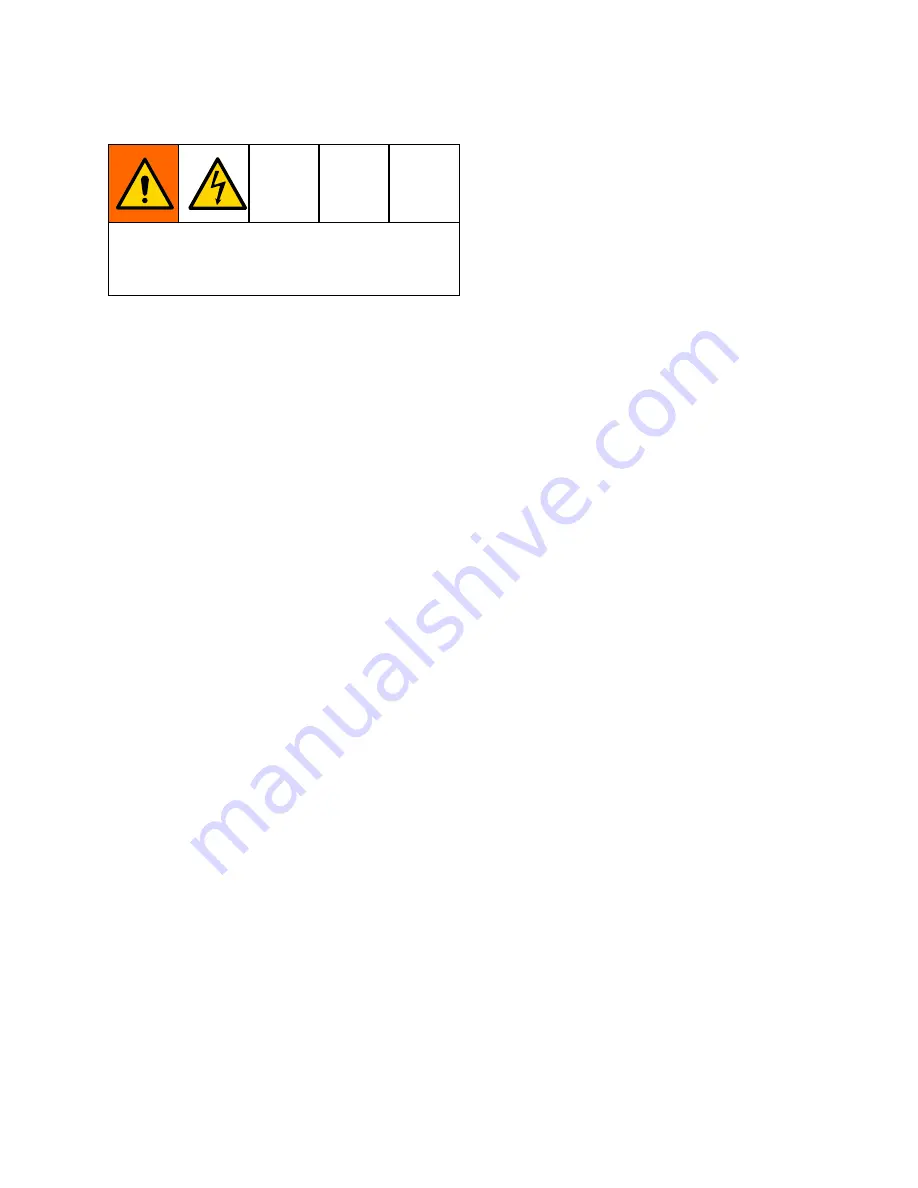
Electro-pneumatic Control Panel Display Screens
Ethernet/IP
Ethernet/IP
Ethernet/IP
To reduce the risk of injury due to electric
shock, remove power to the control panel before
entering the control panel to make connections for
measurement devices.
A network cable is required to use Ethernet/IP
communication with a remote Allen-Bradley PLC.
Insert the network cable into the IF2 port on the back
side of the screen unit.
NOTE:
NOTE:
NOTE: The minimum Requested Packet Interval
(RPI) for this interface is 20 milliseconds.
NOTE:
NOTE:
NOTE: The Ethernet/IP interface uses implicit
messaging. One variable bank is for inputs, and one
variable bank is for outputs.
Connect
Connect
Connect a
a
a Remote
Remote
Remote PLC
PLC
PLC
Contact Graco Customer Support to obtain a
configuration file with the .L5K file extension needed
for this procedure. Then, follow this procedure to
configure the remote PLC to communicate with the
control panel.
NOTE:
NOTE:
NOTE: These instructions are for configuring an
Allen-Bradley PLC using the Studio 5000 software.
1.
Import the .L5K file into Studio 5000 to create a
new Studio 5000 project.
NOTE:
NOTE:
NOTE: Contact Graco Customer Support to
obtain a configuration file with the .L5K file
extension.
2.
Export the following settings from the project:
a.
The controller tags
b.
The “CopyEthIP” program (located under
Tasks)
c.
The “AssembInType” and “AssembOutType”
data types (located under User-Defined Data
Types)
3.
Open the run-time project, where the settings
from Step 2 will be imported.
4.
In the run-time Studio 5000 project, create the
Ethernet/IP communication module.
a.
Under Ethernet, select
ETHERNET-MODULE to create a new
generic Ethernet module.
b.
Configure the module exactly as the
ETHERNET-MODULE is configured in the
project with the imported .L5K file, except
for the IP Address. Enter the IP Address
assigned to the SDU system.
c.
After creating the module, set the RPI
to a minimum of 20 milliseconds in the
Connection Properties.
5.
Right-click on User-Defined Data Types
and import the “AssembInType” and
“AssembOutType” data types.
6.
Import the controller tags: Select
Tools > Import
> Tags and Logic Comments
.
This will create EthIP_In and EthIP_Out data
types in the controller tags with all variables
named in the Variable Interface List.
7.
Right-click on the Main Task and import the
CopyEthIP program. Once the CopyEthIP
program is done importing, the configuration
for the Ethernet/IP communication with the
Allen-Bradley PLC will be complete. Modify the
program as needed within bounds of the protocol.
8.
For remote communication, configure the IP
Address, Subnet Mask, and the Remote IP
Address on the Network page of the SDU. See
9.
Enable the Ethernet/IP communication on the
SDU system.
NOTE:
NOTE:
NOTE: Restart the SDU to initiate communication
between the PLC and the SDU.
Variable
Variable
Variable Interface
Interface
Interface List
List
List
Allen-Bradley PLC variables are prepended with the
following naming structures:
Input: BR2AB_
Output: AB2BR_
NOTE:
NOTE:
NOTE: All output variables correspond to a variable
on the input interface. The output variables are sent
back from the SDU so that the remote PLC can verify
that the sent value was seen by the SDU system.
NOTE:
NOTE:
NOTE: The SDU must be told which variables
to read from the Allen-Bradley PLC. Set the
AB2BR_networkOverwriteBitfield variable
appropriately to control the SDU system remotely.
3A5402J
53
Содержание SaniForce SDU A01AAA1AA0C21
Страница 74: ...Notes Notes Notes Notes 74 3A5402J...