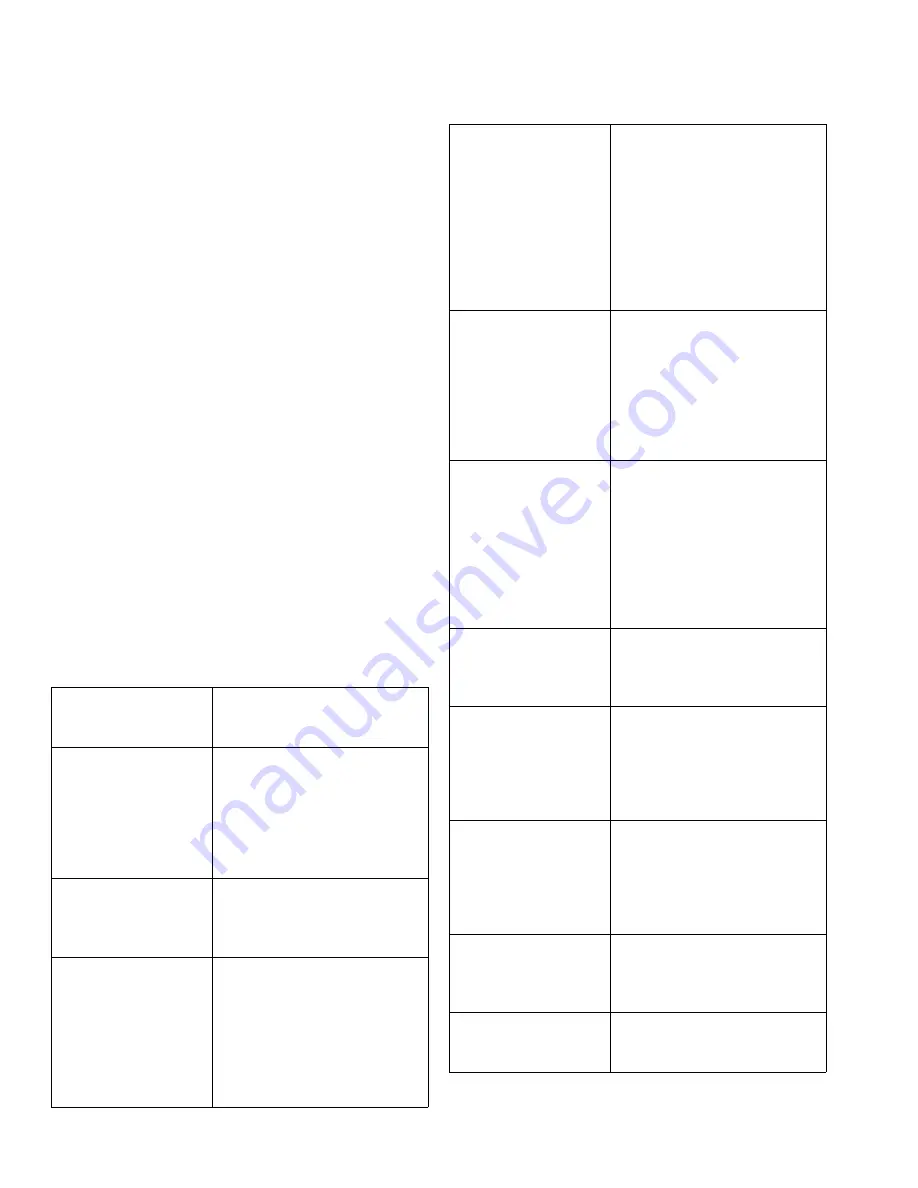
Pump
28
3A5082G
Error Log
The Error Log lists Set Time and Clear Time for the last
400 faults and warnings. The most recent event is listed
first.
The log file is stored as:
GRACO/{DMS_id}/{download date -
YYYYmmDD}/ERRORLOG.CSV
Example: GRACO/00613/20160911/ERRORLOG.CSV.
Sample Error Log
Common Error Log entries are listed below.
Error Log
DMS ID Number: 00613
Software Part No.:17J936
Software Version:0703
12/31/2016 23:04:00
Date
Time
Description
12/31/2015 23:03:54 Low Level Cleared
12/31/2015 23:03:42 Low Level Fault
12/31/2015 23:03:32 Low Level Warning
12/31/2015 23:03:22 Over Current
12/31/2015 23:03:19 Over Current Shut Down
Software Fault
An internal software error
occurred. Contact Graco
Customer Service.
Low Level Warning
The unit entered a low level
warning mode and is running
low on material. The pump
continues to dispense material
for the duration of the low level
alarm time specified by the
unit.
Low Level Fault
The alarm time in low level
warning has elapsed. The unit
will not pump until the reservoir
is filled and the fault is cleared.
Motor Overcurrent
Warning
The unit is out of expected
motor current range. Check the
system to determine that it is
functioning correctly (i.e., no
blocked lines). Continued
operation at excessive motor
currents will cause degradation
in pump life.
High Temperature
Warning
Internal temperature of the unit
is above the designated
operating temperature. Check
the unit and system to
determine that it is functioning
correctly. Operating outside of
the specified temperature
range may cause reduced
performance and possible unit
failure.
Motor Overcurrent
Fault
The unit is out of expected
motor current range. Check the
system to determine that it is
functioning correctly (i.e., no
blocked lines). Continued
operation at excessive motor
currents will cause degradation
in pump life.
Low Temperature
Warning
Internal temperature of the unit
is below the designated
operating temperature. Check
the unit and system to
determine that it is functioning
correctly. Operating outside of
the specified temperature may
cause reduced performance
and possible unit failure.
Low Power Fault Pump
On
The power source does not
have enough power to power
the pump when it turns on.
Replace power source.
Low Power Warning
Cleared
The voltage of the power
source dropped below and
acceptable threshold. The
warning was cleared either by
user intervention, or by
self-correction.
Low Power Fault
Cleared
The voltage of the power
source dropped below an
acceptable threshold for longer
than 15 minutes and the pump
faulted out. The fault was
cleared by the user.
USB Unable to Mount
The USB flash drive that was
installed was unable to connect
and communicate with the
pump.
USB Unsupported
Device
The USB flash drive is
unsupported. Use a different
flash drive.
Содержание 24Z660
Страница 7: ...Typical System Installation 3A5082G 7 FIG 4 ...
Страница 11: ...Pump 3A5082G 11 Pump Dimensions FIG 7 ...
Страница 13: ...Pump 3A5082G 13 Mounting Bracket and Pump Dimensions FIG 9 ...
Страница 67: ...Notes 3A5082G 67 Notes ...