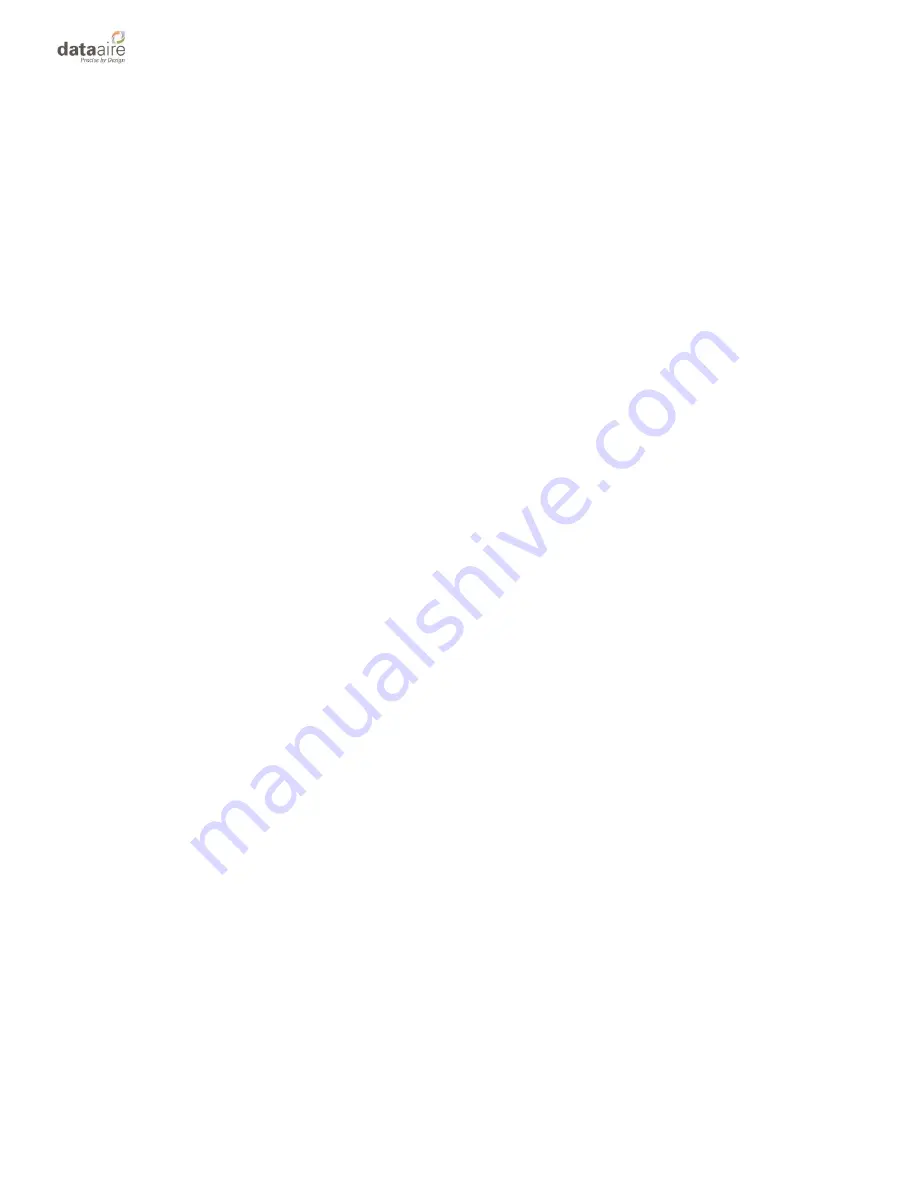
INDEX
87
A
Air 3, 4, 5, 6, 7, 17, 18, 19, 21, 22, 26, 35, 41, 45, 46, 47,
48, 68, 76, 77, 80
air discharge plenum ..................................................... 18
air distribution plenum ................................................... 18
Air filter .......................................................................... 68
Air vent .......................................................................... 26
B
Building Management System ...................................... 68
C
Charging ... 4, 5, 44, 45, 46, 48, 50, 51, 53, 54, 56, 61, 63
Computer Room Air Conditioner ..................................... 7
Condensate pump ................................................... 29, 38
Condensing unit ............................................................ 36
Contact Data Aire ........................................ 31, 67, 70, 75
Controls ......................................................................... 76
CRAC .................................................................... 7, 8, 60
Crankcase heater .............................................. 48, 49, 52
D
dap microprocessor controller ........................................ 7
dap4 .. 2, 4, 14, 18, 37, 41, 46, 48, 49, 50, 52, 53, 55, 62,
66, 68, 74
dap4 microprocessor ..................................................... 37
Discharge Lines ........................................................ 3, 20
Disconnect switch ............................................... 4, 33, 38
Disconnect Switch ......................................................... 33
Drain/fill valve ................................................................ 26
E
EC ............................................ 18, 40, 46, 47, 74, 76, 80
Electric .............................................. 6, 12, 41, 73, 74, 79
Electric reheat ............................................................... 73
Electrical ........... 3, 4, 6, 11, 31, 34, 35, 38, 41, 73, 76, 79
Electronic Expansion Valve ....................................... 5, 40
Electronically Commutated ........................... 6, 18, 40, 74
Elements ................................................................... 6, 74
Energy Saver................................................................. 65
Evacuation .................................. 4, 42, 43, 44, 48, 51, 54
F
FAQ ............................................................................... 79
Filter ................................................................ 5, 6, 69, 72
Flooded system ....................................................... 54, 64
Frequently Asked Questions ......................................... 79
Fuse ........................................................................ 35, 73
G
Glycol system ................................................................ 35
Grounding ................................................................. 4, 35
H
Head pressure ........................................................ 50, 53
Heat .......................................................... 4, 6, 36, 45, 47
Humidifier ............................................ 3, 5, 30, 70, 76, 78
I
Inspection .......................................................... 3, 5, 8, 67
Installation .. 3, 6, 9, 12, 17, 19, 23, 26, 29, 30, 31, 32, 35,
41, 47, 59, 80
L
Liquid line ................................................................ 21, 63
Liquid line solenoid valve .............................................. 63
Locating .................................................................... 3, 16
Loose items ..................................................................... 8
Low Ambient Receiver Package ..... 4, 5, 6, 45, 54, 63, 64
M
Maintenance .... 2, 5, 9, 26, 29, 32, 35, 41, 47, 59, 67, 71,
76, 79, 80
Manual Override Switches ........................................ 4, 39
Maximum Overcurrent Protection ........................... 35, 79
Minimum circuit ampacity ............................................. 79
O
Outside air ..................................................................... 13
P
Paperwork ................................................................... 3, 8
Phase check ................................................................. 46
Piping 3, 5, 18, 19, 21, 23, 24, 25, 26, 27, 29, 30, 65, 72,
76, 80, 81
R
raised floor .................................................. 17, 18, 19, 39
Receiver ...................................................... 45, 54, 64, 65
Recommended gas velocity .......................................... 21
Reheat .......................................................... 6, 74, 76, 78
Remote ................... 3, 4, 6, 23, 24, 35, 36, 37, 39, 79, 80
return air plenums ......................................................... 18
Rigging ................................................................ 3, 13, 15