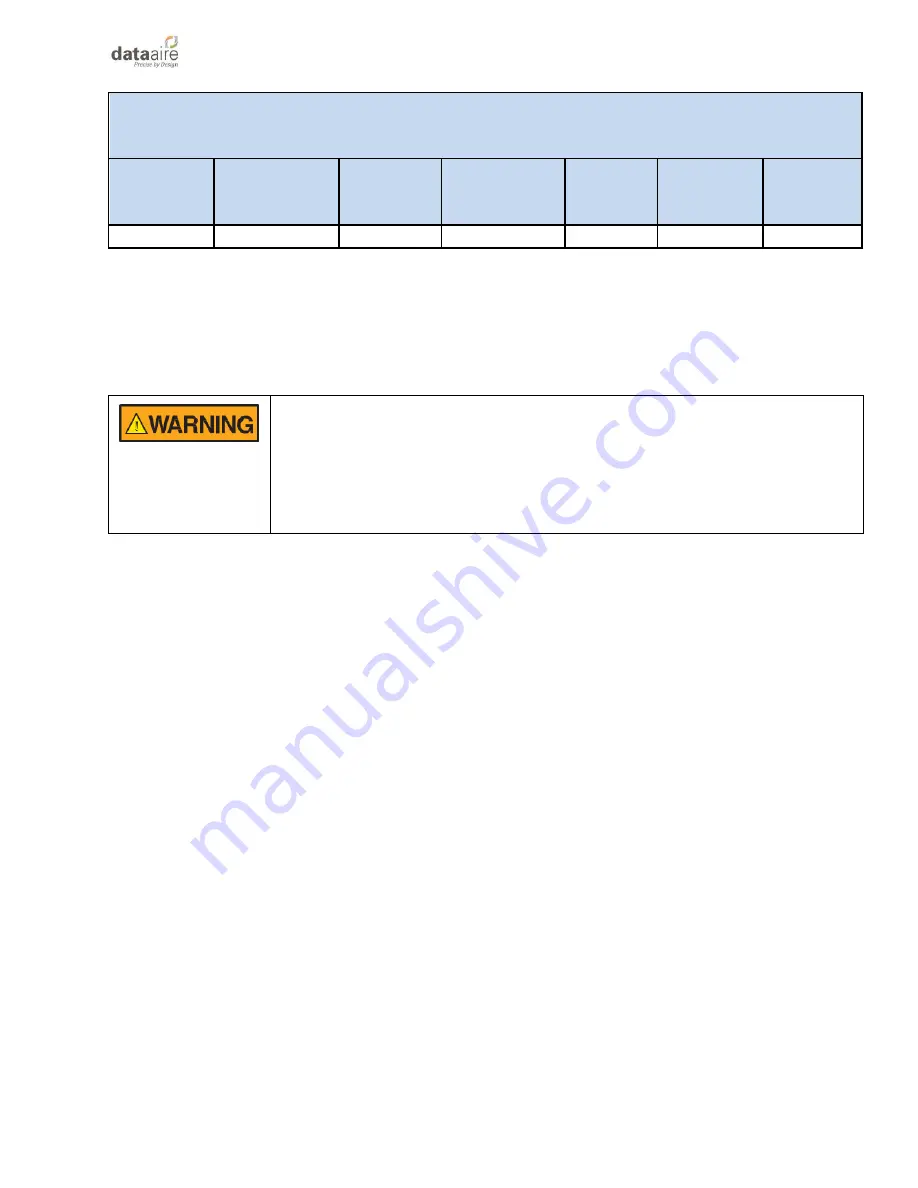
59
Table 2 - Packaged Units with Receivers
Acceptable parameters range for water/glycol packaged units with receivers, with return air temperature of
65°F to 85°F and entering water/glycol temp of 65 - 85°F (110°F for Glycol)
Refrigerant
Liquid Line
Pressure (psig)
Liquid Line
Temp (°F)
Suction
Pressure (psig)
Suction
Sat.
Temp (°F)
Subcooling
Temp (°F)
Superheat
Temp (°F)
R410A
290
– 390
85 - 100
103 - 130
33 - 45
0 - 3
12 - 18
The superheat at the compressor suction line at least 6 inches (152 mm) away from the
compressor.
All water/glycol cooled units have a water regulating valve. A head pressure transducer is
connected to a Schrader fitting on the discharge line and water is regulated into the condenser
coil (plate fin condensers are standard).
WARNING:
Before starting a compressor, the crankcase heater should
be energized for a minimum of 12 hours to reduce the possibility of liquid
slugging on start-up. Failure to energize the crankcase heater could
result in compressor damage. If the system is charged from a vacuum,
the preheating of the compressor is not necessary.
5.8.
Commissioning a Running Compressor
The system must be monitored after initial startup for a minimum of 60 minutes to ensure proper
operating characteristics, such as:
•
Check the current draw of compressor is within acceptable values.
•
Check the suction and discharge pressures are within acceptable levels.
•
Check for proper EEV operation and desired superheat readings.
•
Check the superheat to reduce risk of slugging.
•
Observe the oil level in compressor sump at startup and during operation to confirm that the
oil level remains visible and indicating proper oil return.
✓
Excess foaming in oil sight glass indicates refrigerant on the sump.
•
Monitor the oil sight glass for 1 hour after system equilibrium to ensure proper oil return to
the compressor. This oil check must be done over the full speed range of the compressor to
guarantee:
✓
A good oil return at low speed with minimum gas velocity.
✓
A good oil management at high speed with maximum oil carry over.
✓
Low foaming in sight glass and compressor sump temperature 10⁰ F above
saturation temperature to show there is no refrigerant migration taking place.
•
Acceptable cycling rates of compressors, including duration or run times.
•
Check all piping for abnormal vibration or noise. Movements in excess of 1.5 mm require
corrective measures such as piping braces or brackets.
•
When needed, add refrigerant.
•
Do not overcharge the system.
•
Record type and amount of refrigerant charge as well as operating conditions as a reference