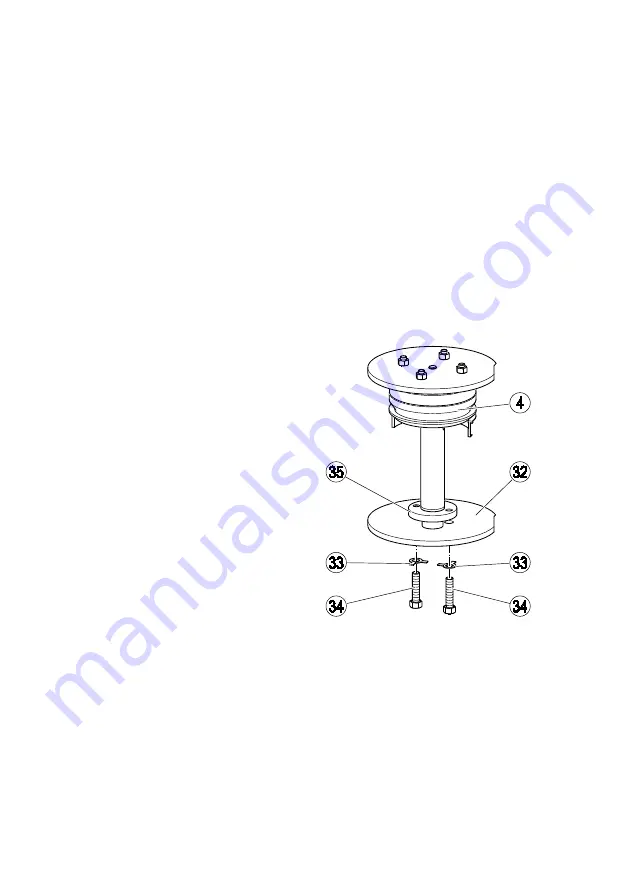
44
For work on the equipment you will need the
following tools:
Torque spanner (US: wrench) 4-40 Nm
Torque spanner (US: wrench) 20-120 Nm
2 Spanners A. F. 8 mm
2 Spanners A. F. 19 mm (TK 23) or 24 mm (TK
24)
Screwdriver 6 mm
Screwdriver 10 mm
Exchanging the regulator unit of equipment
with DN 50
Remove the cover as described in section
"
Removing cover of equipment with DN 50
from page 34 onwards.
The regulator set comprises the whole regulator
unit with the adjustment screw attached to it.
Replace the regulator unit with the attached
adjustment screw with a new one.
Attach the cover to the body as described in
section "
Mounting cover of equipment with DN
Exchanging the regulator unit of equipment
with DN 65 - 100
Remove the cover as described in section
"
Removing cover of equipment with DN 65 -
To take out the regulator unit (4) you have to
remove the lift plate (32).
Bend open the retaining metal straps (33).
Remove the hexagon-head cap bolts (34).
Detach the lift plate (32) from the regulator unit.
Unscrew the washer nut (35) from the stem of
the regulator unit.
Lift the regulator unit (21) off the body.
Put a new regulator unit into the body.
Screw the washer nut (35) onto the stem of the
regulator unit.
The stop dog for the lift plate at the lower end of the
stem must protrude approx. 3 to 4 mm after
positioning the lift plate in place.
Put the lift plate (32) onto the stem of the
regulator unit.
Turn the lift plate until the bores in the lift plate
and in the washer nut are aligned one on top of
the other.
Put the retaining metal straps (33) onto the
threads of the hexagon-head cap bolts.
Screw the hexagon-head cap bolts (34) into the
bores.
Tighten the hexagon-head cap bolts with a
torque of 5 Nm.
Bend back the retaining metal straps.
Attach the cover to the body as described in
section "
Mounting cover of equipment with DN
Содержание TK 23
Страница 1: ...Steam Trap for Large Condensate Flowrates TK 23 TK 24 Original Installation Instructions 819309 01 ...
Страница 56: ...56 Capacity Charts Capacity chart for hot water A Flowrate B Differential pressure Δ PMX ...
Страница 57: ...57 Capacity chart for cold water A Flowrate B Differential pressure Δ PMX ...
Страница 62: ...62 ...
Страница 63: ...63 ...