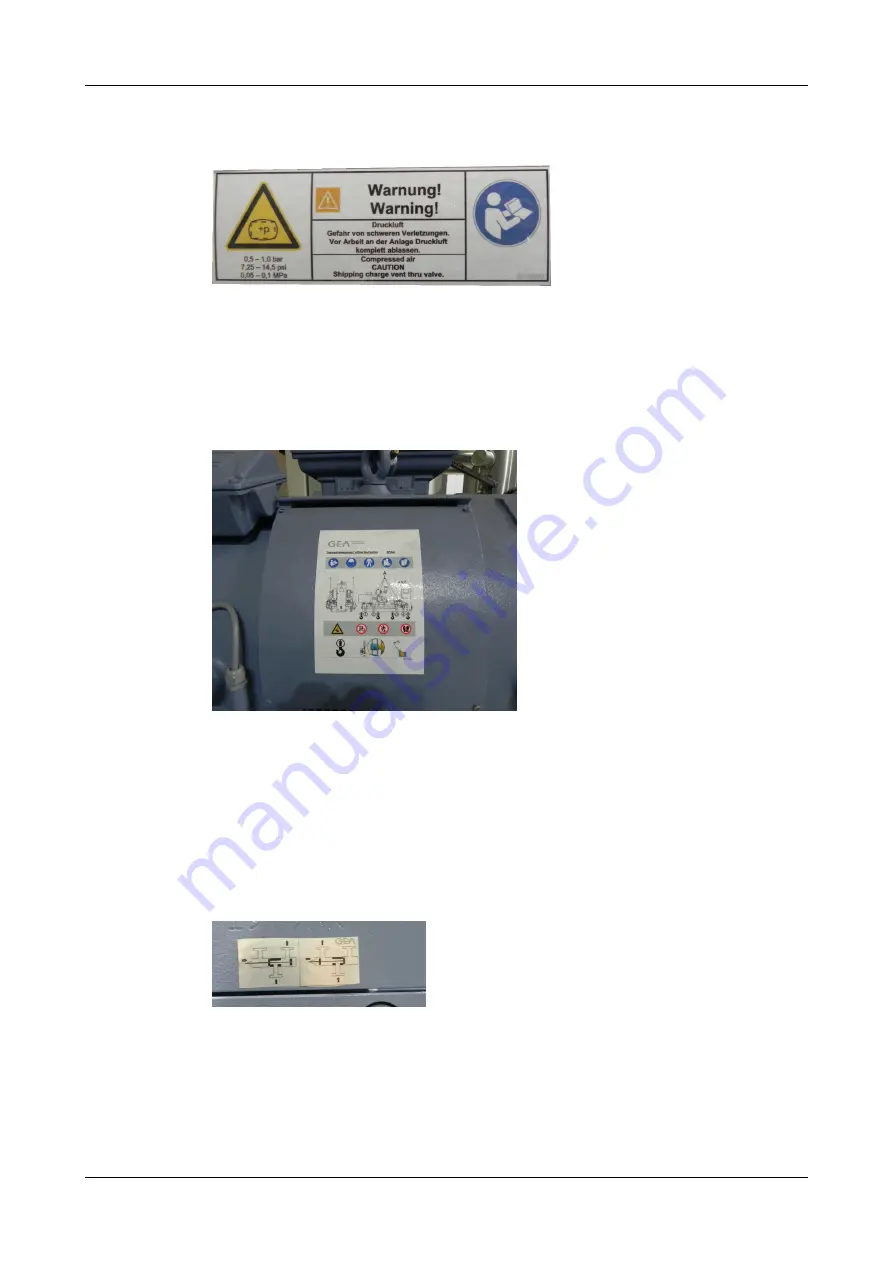
3.1.5.6 Label, Pressurised product
(Safety labels)
Fig.18:
Label, Pressurised product
Importance of the labels:
Before working on the product, the inert gas filling must be completely emptied.
3.1.5.7 Label for transport
(Handling instructions)
Fig.19:
Label for transport
Importance of the labels:
Adherence to all guidelines and information on the transport instruction.
The transport instruction for the respective product can be called up as separate
document at GEA Refrigeration Germany GmbH.
3.1.5.8 Label of the change-over valve
(Handling instructions)
Fig.20:
Label of the change-over valve
Importance of the labels:
Representation showing which valve setting is active.
Description
Design
L_151511_2
46
19.12.2019
Содержание RedGenium
Страница 6: ...L_151511_2 6 19 12 2019...
Страница 8: ...L_151511_2 8 19 12 2019...
Страница 14: ...L_151511_2 14 19 12 2019...
Страница 118: ......