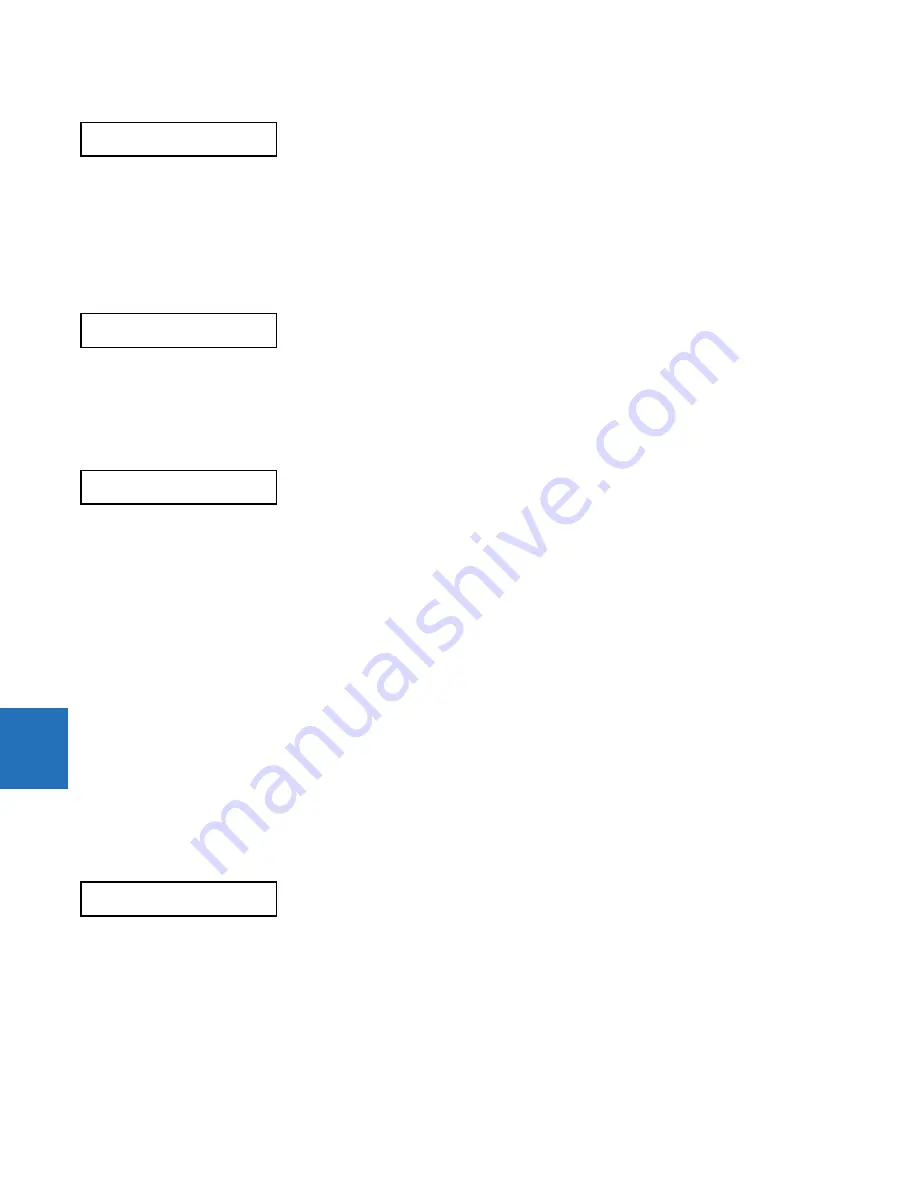
7-12
T35 TRANSFORMER PROTECTION SYSTEM – INSTRUCTION MANUAL
TARGETS MENU
CHAPTER 7: COMMANDS AND TARGETS
7
•
Description of problem
: The number or type of installed hardware modules does not match the order code stored in
the CPU. The standard UR-series Equipment Mismatch self-test is extended to cover the possible presence of a
Process Card.
•
Severity
: Protection is not available and all contact outputs and shared outputs are de-asserted.
•
What to do
: Check all modules against the order code. Ensure they are inserted properly, and cycle the control power.
If a module has intentionally been added or removed use the Update Order Code command to notify the relay that the
current module configuration is correct.
•
Description of problem
: UR-series device module hardware failure detected.
•
Severity
: Protection is not available and all contact outputs and shared outputs are de-asserted.
•
What to do
: Contact the factory and supply the failure code noted in the display. Text in the message identifies the
failed module (for example, H81). If operated on a Process Card failure, the Module Fail self-test seals-in (latches) till the
UR-series device is restarted.
•
Description of problem
: Mission critical data is not available via the process bus. An AC quantity is considered critical if
both AC bank origins and the crosschecking settings are other than None. This self-test is also initiated by an AC input
discrepancy being detected. See the description in the
Crosschecking
setting in the HardFiber manual for further
information. In addition, this self-test can be initiated by user logic responding to loss of critical contact input/output
or other data using the
Process Bus Failure Operand
user-programmable self-test setting. This setting is located in
the
Settings > Product Setup > User-Programmable Self Test
menu.
•
Severity
: Protection is not available and all contact outputs and shared outputs are de-asserted.
•
What to do
: First rectify any Process Bus Trouble and Brick Trouble self-test errors. Check the actual value of the
operand referenced by the Process Bus Failure Operand setting, and if “On,” determine the cause and rectify.
If the problem persists with the foregoing all clear, the cause must be an AC input discrepancy, which is typically the
result of problems in the input signals to the Bricks, or faults in the Brick input conditioning hardware. If the error was
annunciated the first time significant signal was encountered, suspect the former cause and check the copper
connections external to the Brick. Where multiple UR-series devices have self-test errors, look for common causes.
To further isolate AC input discrepancy errors, put the relay in test-isolated mode, then one by one, temporally change
an AC bank Crosschecking setting to None, until the Process Bus Failure clears. Once the problem AC bank has been
identified, the values from each of the two Bricks can be examined individually by temporarily mapping each to an AC
bank with a single origin.
7.2.2.5 HardFiber minor self-test error messages
•
Description of problem
: Communications problems with one or more Bricks. The text of the message identifies the
affected field units. This self-test is initiated by low received signal levels at either the Brick or Process Card end, and
by the sustained failure to receive poll responses from the proper Brick.
•
Severity
: This self-test error does not directly inhibit protection. However, the affected Brick inputs/outputs may not be
available to the UR device.
•
What to do
: Check the field unit actual values. An indication of equipment mismatch means that messages are being
received from a Brick, but there is a discrepancy between the settings and the actual Brick serial number, order code,
and/or core number. Check that the correct core on the correct Brick is patched through to the correct Process Card
EQUIPMENT MISMATCH
MODULE FAILURE
PROCESS BUS FAILURE
PROCESS BUS TROUBLE
Содержание T35
Страница 9: ...TABLE OF CONTENTS T35 TRANSFORMER PROTECTION SYSTEM INSTRUCTION MANUAL ix ABBREVIATIONS INDEX ...
Страница 10: ...x T35 TRANSFORMER PROTECTION SYSTEM INSTRUCTION MANUAL TABLE OF CONTENTS ...
Страница 14: ...1 4 T35 TRANSFORMER PROTECTION SYSTEM INSTRUCTION MANUAL FOR FURTHER ASSISTANCE CHAPTER 1 INTRODUCTION 1 ...
Страница 202: ...4 88 T35 TRANSFORMER PROTECTION SYSTEM INSTRUCTION MANUAL FLEXLOGIC DESIGN USING ENGINEER CHAPTER 4 INTERFACES 4 ...
Страница 472: ...5 270 T35 TRANSFORMER PROTECTION SYSTEM INSTRUCTION MANUAL TESTING CHAPTER 5 SETTINGS 5 ...
Страница 500: ...6 28 T35 TRANSFORMER PROTECTION SYSTEM INSTRUCTION MANUAL PRODUCT INFORMATION CHAPTER 6 ACTUAL VALUES 6 ...
Страница 514: ...7 14 T35 TRANSFORMER PROTECTION SYSTEM INSTRUCTION MANUAL TARGETS MENU CHAPTER 7 COMMANDS AND TARGETS 7 ...
Страница 580: ...A 16 T35 TRANSFORMER PROTECTION SYSTEM INSTRUCTION MANUAL FLEXANALOG ITEMS APPENDIX A FLEXANALOG OPERANDS A ...
Страница 588: ...C 6 T35 TRANSFORMER PROTECTION SYSTEM INSTRUCTION MANUAL COMMAND LINE INTERFACE APPENDIX C COMMAND LINE INTERFACE C ...
Страница 596: ...iv T35 TRANSFORMER PROTECTION SYSTEM INSTRUCTION MANUAL ABBREVIATIONS ...