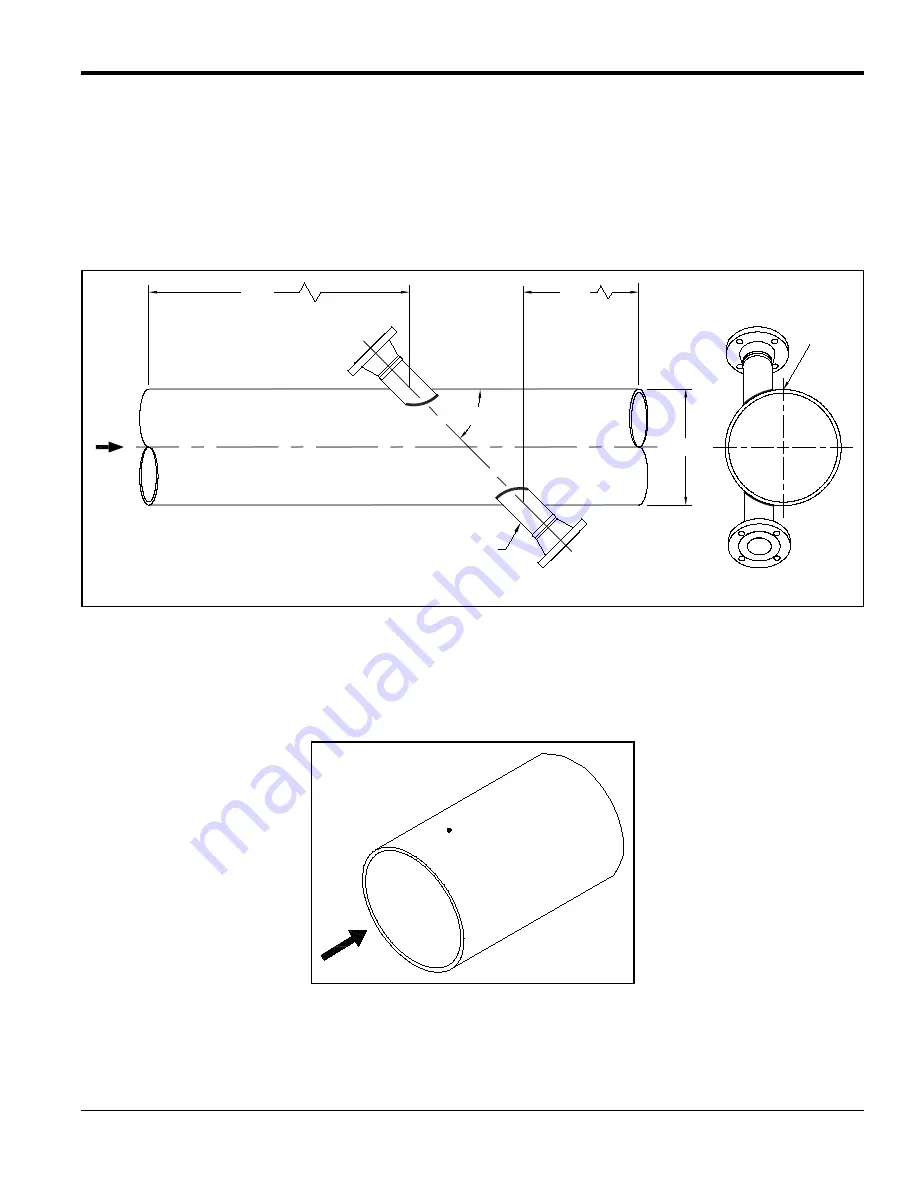
Model T17 Installation Guide
39
Chapter 2. Installing the Pipe Nozzles
2.4.2 Selecting and Marking the First Nozzle Location - MR2 Mid-Radius (cont.)
To mark the first nozzle location, complete the following steps:
1.
For optimum performance, you should select a location that has at least 20 pipe diameters of straight,
undisturbed flow upstream and 10 pipe diameters of straight, undisturbed flow downstream from the
measurement point (see
below). Undisturbed flow means avoiding sources of turbulence such as
valves, flanges, elbows, swirl and disturbed flow profiles.
Figure 48: MR2 Mid-Radius Nozzle Locations
Note:
We recommend that you install the nozzles on a chord as near as possible to the horizontal plane for horizontal
pipe. If you cannot find a proper nozzle location, please contact GE for assistance.
2.
Locate the top of the pipe and put a center punch mark there as a reference mark.
Figure 49: Punch Mark on Top of Pipe
FLOW
NOZZLE
(2 PLACES)
10D
20D
D
45°
TOP VIEW
END VIEW
TOP
Содержание T17
Страница 1: ...GE Oil Gas Flow 916 128 Rev D September 2020 Model T17 Ultrasonic Flow Transducer Installation Guide ...
Страница 2: ......
Страница 4: ...ii no content intended for this page ...
Страница 62: ...Chapter 2 Installing the Pipe Nozzles 54 Model T17 Installation Guide no content intended for this page ...
Страница 64: ...Chapter 3 Installing an Isolation Valve 56 Model T17 Installation Guide no content intended for this page ...
Страница 88: ...Chapter 6 Specifications 80 Model T17 Installation Guide no content intended for this page ...
Страница 90: ...Warranty 82 Model T17 Installation Guide no content intended for this page ...
Страница 92: ......
Страница 93: ......