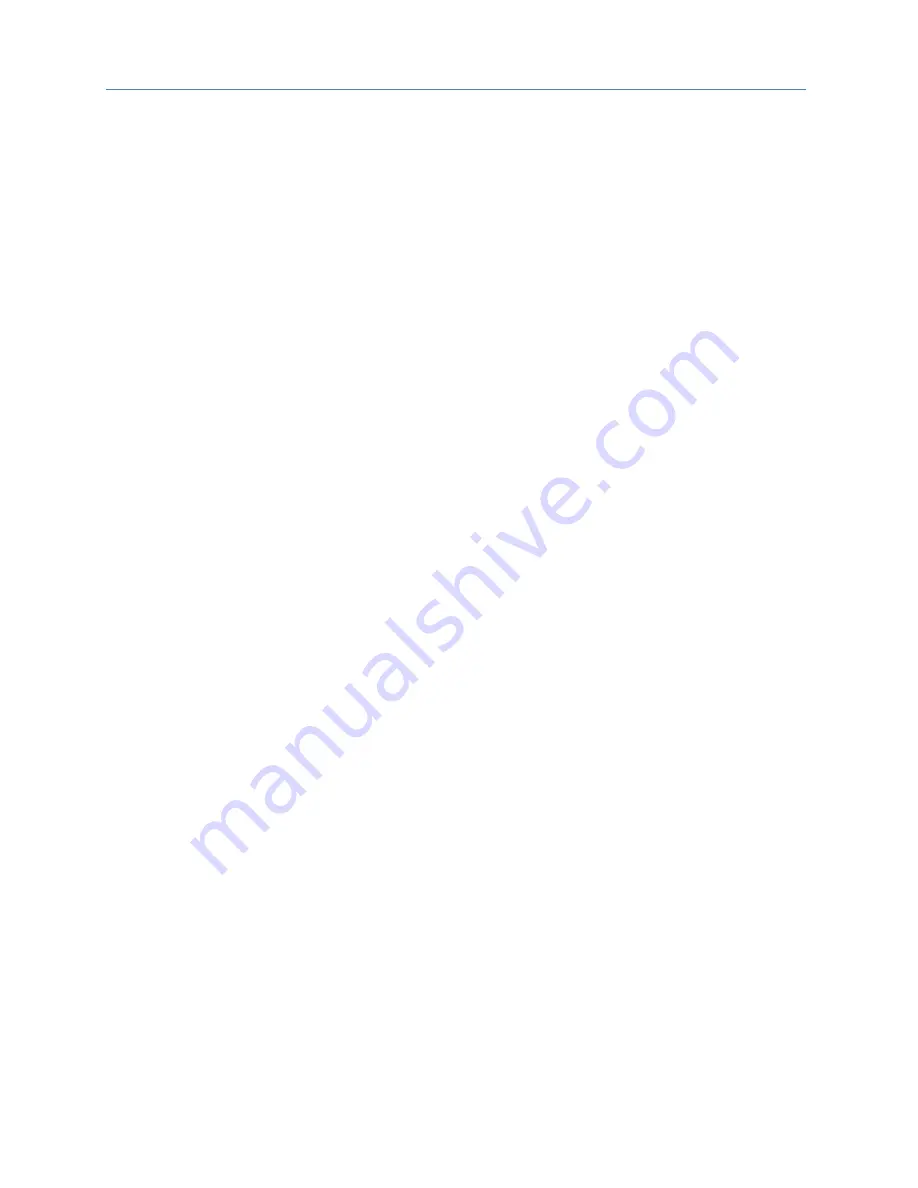
Chapter 2. CPU Features & Specifications
102
PACSystems* RX7i, RX3i and RSTi-EP CPU Reference Manual
GFK-2222AD
The CPE100/CPE115 are
programmed and configured over Ethernet via GE’s Proficy* Machine Edition
(PME) software. Each is a standalone CPU with the following features:
•
A built-in PACSystems RSTi-EP PLC CPU
o
User may program in Ladder Diagram, Structured Text, Function Block Diagram.
o
Both CPE100 & CPE115 have configurable data and program memory. This entire memory will
be preserved between power cycles.
o
Supports auto-located Symbolic Variables that can use any amount of user memory.
o
Reference table sizes include 2k bits for discrete %I and %Q and up to 2k words each for analog
%AI and %AQ. Bulk memory (%W) also supported for data exchanges.
o
Supports up to 512 program blocks. Maximum block size is 128KB.
•
Supports two independent 10/100 Ethernet LANs. LAN1 has only one port and is dedicated to high
speed Ethernet and whereas LAN2 is comprised of three switched ports (labelled as 2, 3 & 4)
configurable either as a second embedded Ethernet controller or an embedded PROFINET controller.
All four ports are located on the front panel, as shown in Figure 31.
•
The embedded communications interface has dedicated processing capability, which permits the
CPU to independently support LAN1 and LAN2 with:
o
up to 16 combined SRTP Server and Modbus TCP Server connections out of which:
a)
Modbus TCP cannot exceed more than 8 simultaneous connections.
b)
SRTP server cannot exceed more than 16 simultaneous connections.
o
8 Clients are permitted; each may be SRTP or Modbus TCP or a Combination of both.
o
up to 8 simultaneous Class 1 Ethernet Global Data (EGD) exchanges.
•
The PLC may use one, two or three of the Ethernet ports of LAN2 to support the embedded Simplex
PROFINET I/O Controller. PROFINET supports up to 8 I/O devices with update rates of 16
–
512ms. It
is not recommended to use update rates below 16ms.
•
The CPE100/CPE115 is secure by design, incorporating technologies such as secure boot, trusted
platform module (disabled), and encrypted firmware updates.
•
Module LEDs on the face plate provides basic status and control information of CPE100/CPE115.
•
Ability to display serial number and date code in PME Device Information Details.
•
Media Redundancy Protocol (MRP) allows the CPE100/CPE115 to participate in a PROFINET I/O
network with MRP ring technology. This eliminates the I/O network as a single point of failure. The
CPE100/CPE115 may be used as either a Media Redundancy Manager or Media Redundancy Client.
•
OPC UA Server supports up to 2 concurrent sessions with up to 4 concurrent variable subscriptions
and up to 1000 variables.
•
Modbus RTU Slave support on two serial ports i.e. RS-232 and RS-485 with both 2-wire and 4 -wire
interface. These ports are located on the underside side of the controller and does not provide any
type of isolation.
•
Operating temperature range -40
C to 70
C (-40
F to 158
F).
•
The CPE100/CPE115, when shipped, is configured only for DIN-rail mount. An alternate panel-mount
adaptor plate (ICMFAACC001-AA) is optional and not included in the ship-set.