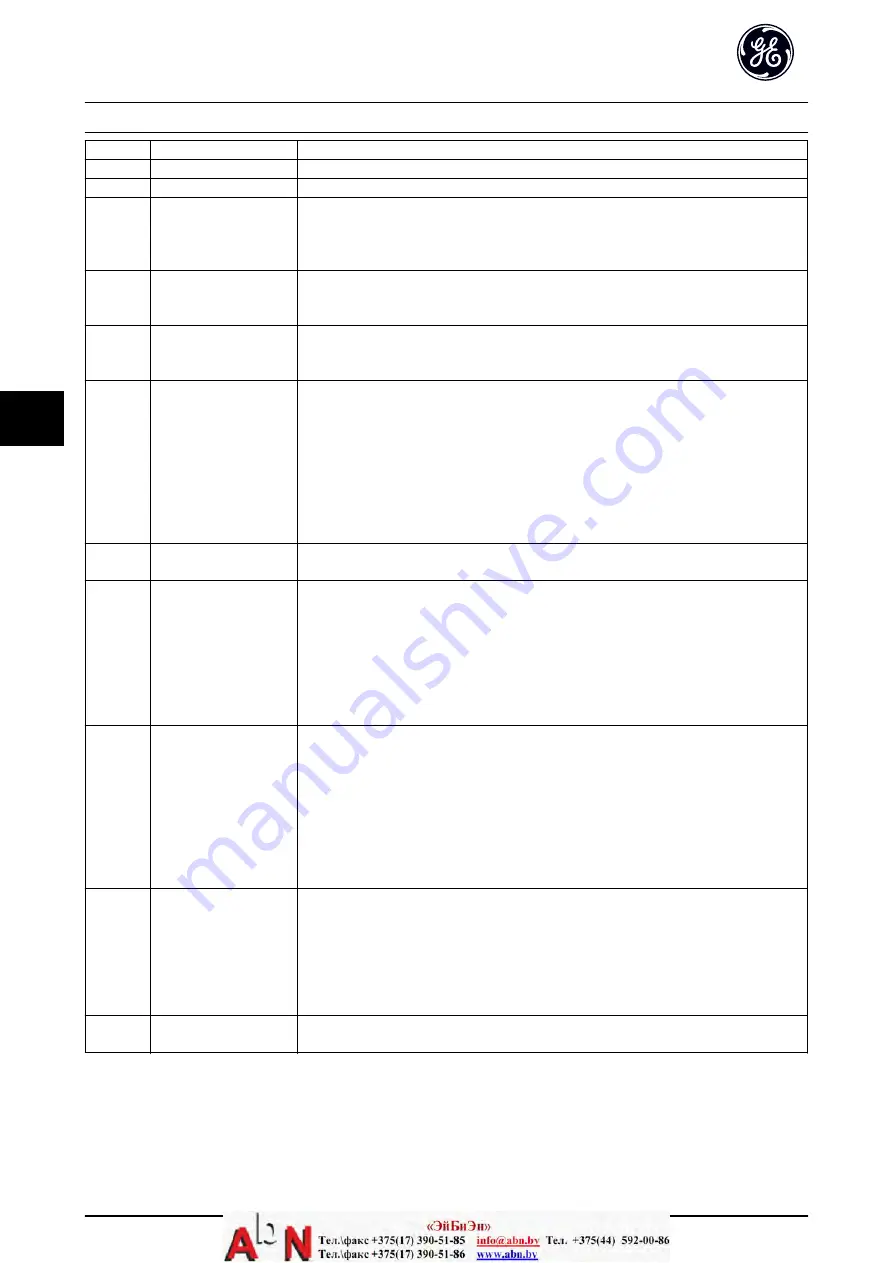
Group
Title
Function
LN-##
LonWorks
Parameters only applicable when a Lonworks option is installed.
BN-##
BACnet
Parameters used for BACnet configuration.
ID-##
Drive Information
Parameters providing operating data and other drive information including: operating and
running hour counters; kWh counter; resetting of the running and kWh counters; alarm/fault log
(where the past 10 alarms are logged along with any associated value and time) and drive and
option card indentification parameters such as code number and software version.
DR-##
Data Readouts
Read only parameters which display the status/value of many operating variables which can be
displayed on the keypad or viewed in this parameter group. These parameters can be partic-
ularly useful during commissioning when interfacing with a BMS via a high level interface.
LG-##
Logs & I/O Opt. Status
Read only parameters which display the last 10 preventative maintenance log items, actions and
time and the value of analog inputs and outputs on the Analog I/O option card which can be
particularly useful during commissioning when interfacing with a BMS via a high level interface.
AP-##
HVAC Appl. Param.
Parameters used to monitor, protect and control pumps, fans and compressors including: no
flow detection and protection of pumps (including auto-setup of this function); dry pump
protection; end of curve detection and protection of pumps; sleep mode (especially useful for
cooling tower and booster pump sets); broken belt detection (typically used for fan applications
to detect no air flow instead of using a Δp switch installed across the fan); short cycle protection
of compressors and pump flow compensation of setpoint (especially useful for secondary chilled
water pump applications where the Δp sensor has been installed close to the pump and not
acoss the furthest most significant load(s) in the system; using this function can compensate for
the sensor installation and help to realise the maximum energy savings).
FB-##
Fire/Bypass Operation
Parameters used to set-up Fire Mode and/or to control a bypass contactor/starter if designed
into the system.
T-##
Timed Functions
Time based parameters including: those used to initiate daily or weekly actions based on the
built in real time clock (e.g. change of setpoint for night set back mode or start/stop of the
pump/fan/compressor start/stop of a external equipment); preventative maintenance functions
which can be based on running or operating hour time intervals or on specific dates and times;
energy log (especially useful in retrofit applications or where information of the actual historical
load (kW) on the pump/fan/compressor is of interest); trending (especially useful in retrofit or
other applications where there is an interest to log operating power, current, frequency or speed
of the pump/fan/compressor for analysis and a payback counter.
CL-##
PID Closed Loop
Parameters used to configure the closed loop PI(D) controller which controls the speed of the
pump, fan or compressor in closed loop mode including: defining where each of the 3 possible
feedback signals come from (e.g. which analog input or the BMS HLI); conversion factor for each
of the feedback signals (e.g. where a pressure signal is used for indication of flow in an AHU or
converting from pressure to temperature in a compressor application); engineering unit for the
reference and feedback (e.g. Pa, kPa, m Wg, in Wg, bar, m3/s, m3/h, °C, °F etc); the function (e.g.
sum, difference, average, minimum or maximum) used to calculate the resulting feedback for
single zone applications or the control philosophy for multi-zone applications; programming of
the setpoint(s) and manual or auto-tuning of the PI(D) loop.
XC-##
Ext. PID Closed Loop
Parameters used to configure the 3 extended closed loop PI(D) controllers which for example
can be used to control external actuators (e.g. chilled water valve to maintain supply air
temperature in a VAV system) including: engineering unit for the reference and feedback of each
controller (e.g. °C, °F etc); defining the range of the reference/setpoint for each controller;
defining where each of the references/setpoints and feedback signals come from (e.g. which
analog input or the BMS HLI); programming of the setpoint and manual or auto-tuning of the
each of the PI(D) controllers.
PC-##
Pump Controller
Parameters used to configure and monitor the built in pump controller (typically used for pump
booster sets).
How to Program
AF-600 FP High Power Operating Instructions
74
6
6
Содержание AF-600 FP Series
Страница 44: ...Please note airflow directions Mechanical Installation AF 600 FP High Power Operating Instructions 43 4 4...
Страница 45: ...Please note airflow directions Mechanical Installation AF 600 FP High Power Operating Instructions 44 4 4...
Страница 46: ...Please note airflow directions Mechanical Installation AF 600 FP High Power Operating Instructions 45 4 4...