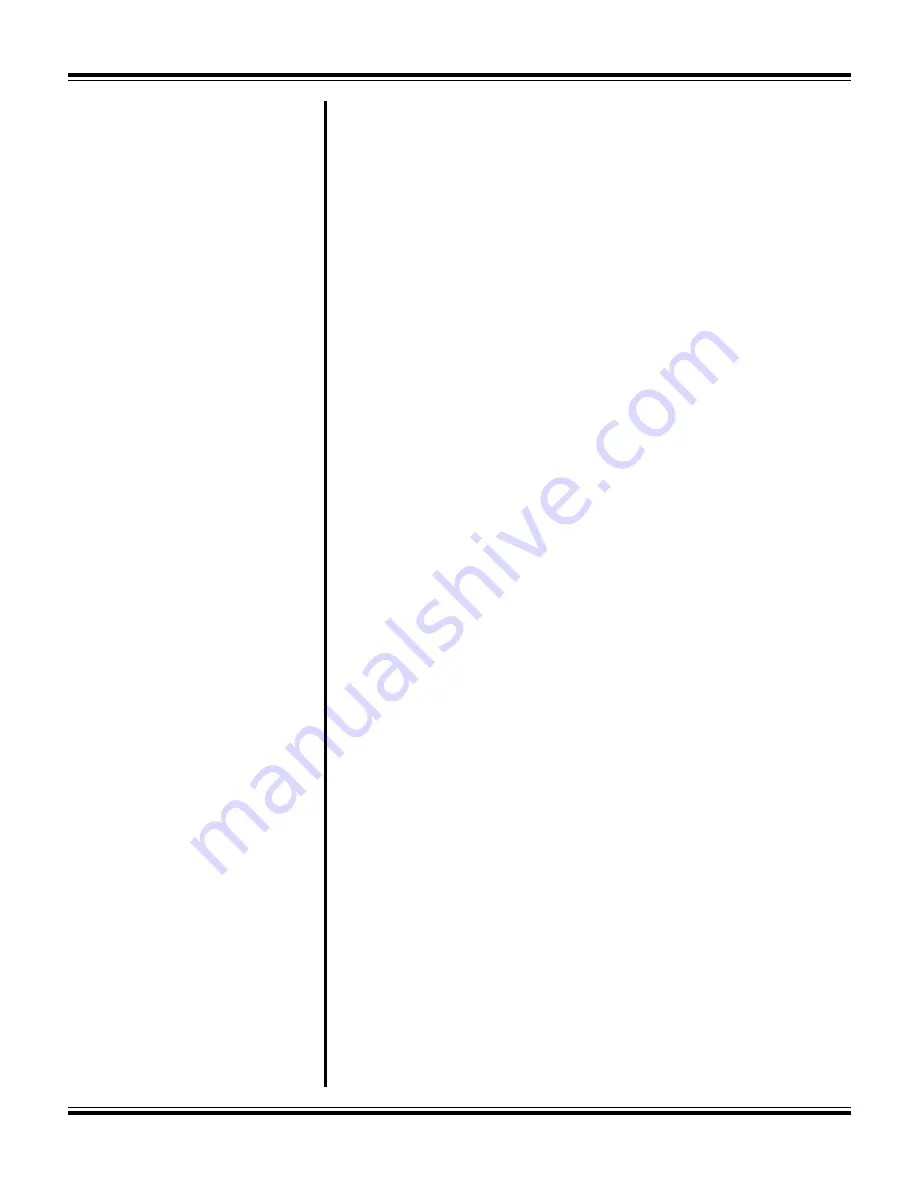
SERVICE MANUAL
Medi-Therm II
THEORY OF OPERATION
w
w
w
.g
aymar
.com P/N 10187-000 7/98
Four cables connect the components in the base of the machine to the PC
boards in the head (see figure 8, p.67):
•
A
9-pin connector
P6 ties the blanket water probe RT2, cold
water reservoir probe RT1, flow switch S5, and level switch S4 to
the power supply board at J2 and ultimately to the control/display
board.
•
A
12-pin connector
P7 ties the high voltage devices (pump,
heater, hot solenoid valve SV2, cold solenoid valve SV1, and
refrigeration compressor relay K1) to the interface circuits on the
power supply board, as well as thermostats S1, S2, and S3 to the
high voltage backup circuitry on the power supply board.
•
A
6-pin connector
P5 connects transformer T1 housed in the
base to the power supply circuitry at J3 on the power supply
board.
•
A
chassis ground harness
from the control/display board
connects to the chassis.
See figure 18, p.79 for the system wiring diagram; figures 19, 20 and 21, pp. 80,
81, 82 for the electrical schematics; figures 22 and 23, pp. 83, 84 for component
layouts and part designations; and figure 24, p. 85 for the control/display board
block diagram.
Power enters the Medi-Therm II machine through circuit breaker CB1 to feed the
refrigeration unit through relay K1. It also then enters the power supply board at
J1 to feed the hot solenoid valve, cold solenoid valve, heater and pump triacs, the
high voltage backup water temperature limiting circuits and transformer T1.
Power to drive the low voltage circuits on the control/display board is derived
from the machine’s power supplies which reside entirely on the power supply
board. The transformer T1 output is rectified and filtered to generate
unregulated positive and negative voltages. Q5, D1, L1 and associated
components are configured as a DC to DC switching regulator in a buck
configuration yielding a nominal output of +5.3 volts DC. Q6 is a linear
regulator with a nominal output of plus twelve (+12) volts DC, while Q7, also
a linear regulator, delivers a nominal output of minus twelve (-12) volts DC.
See figure 18, p. 79 for system wiring diagram; figures 19, 20 and 21, pp. 80, 81,
82 for the electrical schematics; figures 22 and 23, pp. 83, 84 for component
layouts and part designations; and figure 24, p. 85 for the control/display board
block diagram.
The U37 microprocessor is fully dependent on the code stored in the U31
EPROM. When the machine is on, the microprocessor continually cycles through
its main program loop to perform the following:
•
Thermistor output measurement (see section 6.4.1, p. 13)
•
Digital control panel input (section 6.4.2, p. 13)
•
Display update (section 6.4.3, p. 13)
•
Peripheral input (section 6.4.4, p. 14)
•
Blanket/Patient temperature control (section 6.4.5, p. 15)
•
Cold water reservoir temperature control (section 6.4.6, p. 16)
Backup water temperature limiting is achieved independently of the
microprocessor. (See section 6.4.7, p. 16.)
6.2
SYSTEM
COMPONENT
INTERCONNECTIONS
(continued)
6.3
POWER SUPPLY
6.4
MACHINE
FUNCTIONS
12
Содержание MEDI-THERM II MTA5900 Series
Страница 76: ...SERVICE MANUAL Medi Therm II www gaymar com P N 10187 000 7 98 SERVICE INFORMATION Figure 13 Test setup 72...
Страница 82: ...SERVICE MANUAL Medi Therm II www gaymar com P N 10187 000 7 98 This page has been intentionally left blank 78...
Страница 83: ...MEDI THERMTM II IS MADE IN THE USA www gaymar com...