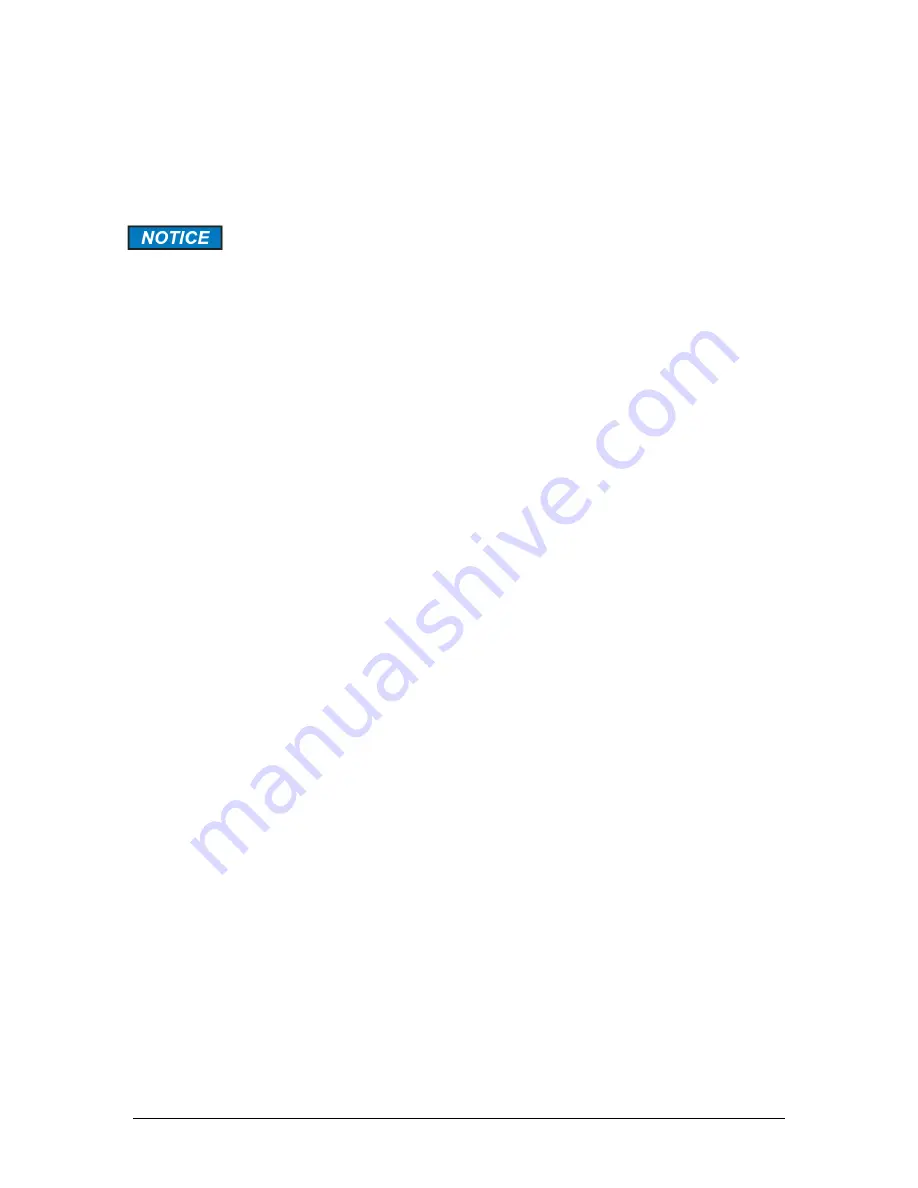
Revision 5
110
August 2021
22. Use the PANEL NEXT / PANEL PREV keys to navigate to the
Spectrum
panel. Adjust
the position of each SMA fitting in the measurement cell by rotating it slightly left and
right and sliding it in and out to find the position that gives the greatest
Peak Height
.
Once the optimal position is found for each fibre, re-tighten the set screw.
The SMA connectors only need to be finger-tight. Do not overtighten the
connectors as this may damage the cable.
23. Optimize the integration period by using the FIELD NEXT / FIELD PREV keys to
highlight
Optimize Integ. Time
, then press ENTER.
24. Observe the optimized integration time. If the
High Integration Period
warning has
cleared, no further work is required at this time. Proceed to the next step in this
procedure. If the
High Integration Period
warning is still present, however, it is likely
that the cell windows are dirty and/or damaged. Proceed to Section 7.5.
25. Make sure that both fibre optic cables are in their correct indent in the oven enclosure
frame, then replace the oven enclosure cover and securely fasten both latches.
26. Reconnect the AC Power to the oven heaters by pushing down and snapping closed
the oven heater fuse terminal cover (ACTS:25). The oven will begin heating to the set
point temperature.
27. Close and latch the oven cover.
28. Close and latch the control cabinet and oven cabinet doors.
29. Confirm that the
High Integration Period
warning has not returned.
30. Once the measurement cell temperature rises to >140°C, and the
Cell Temperature
fault has cleared, use the PANEL NEXT / PANEL PREV keys to navigate to the
Analysis 1
panel. Perform a manual zero calibration cycle by using the FIELD NEXT
/ FIELD PREV keys to highlight
Manual Zero
, then press ENTER..
31. Once the manual zero calibration cycle is complete, place the analyzer into sampling
mode by highlighting the
Sample
checkbox using the FIELD NEXT / FIELD PREV
keys, then press ENTER. Alternatively, press the PURGE key
32. Once normal operation has been confirmed, return the
Online
/
Offline
control toggle
on the
Analysis 2
panel back to
Online
(green).
7.4 Troubleshooting the UV Source Lamp
The UV Source Lamp
requires replacement when either the lamp will not start, or when the
energy output of the lamp has diminished to a point where a
Peak Height
of >20,000 A/D counts
as displayed on the
Spectrum
panel cannot be achieved even with the maximum 1000
millisecond integration period.
Before replacing the UV Source Lamp, it is advisable to eliminate all other potential sources of
the problem, unless the time since the last replacement is >8 months (if using standard lifespan
lamp, Galvanic part number BA7195) or >16 months (if using long life lamp, Galvanic part
Содержание 943-TGXeNA
Страница 130: ...Revision 5 130 August 2021 Figure 82 Oven Cabinet Door Removed ...
Страница 131: ...Revision 5 131 August 2021 Figure 83 Control Cabinet Door Removed ...
Страница 132: ...Revision 5 132 August 2021 Figure 84 Power Steam Air Signals Connection Details ...
Страница 133: ...Revision 5 133 August 2021 Figure 85 AC Wiring Schematic ...
Страница 134: ...Revision 5 134 August 2021 Figure 86 DC Signals and Wiring Diagram ...
Страница 135: ...Revision 5 135 August 2021 Figure 87 Flow Diagram ...