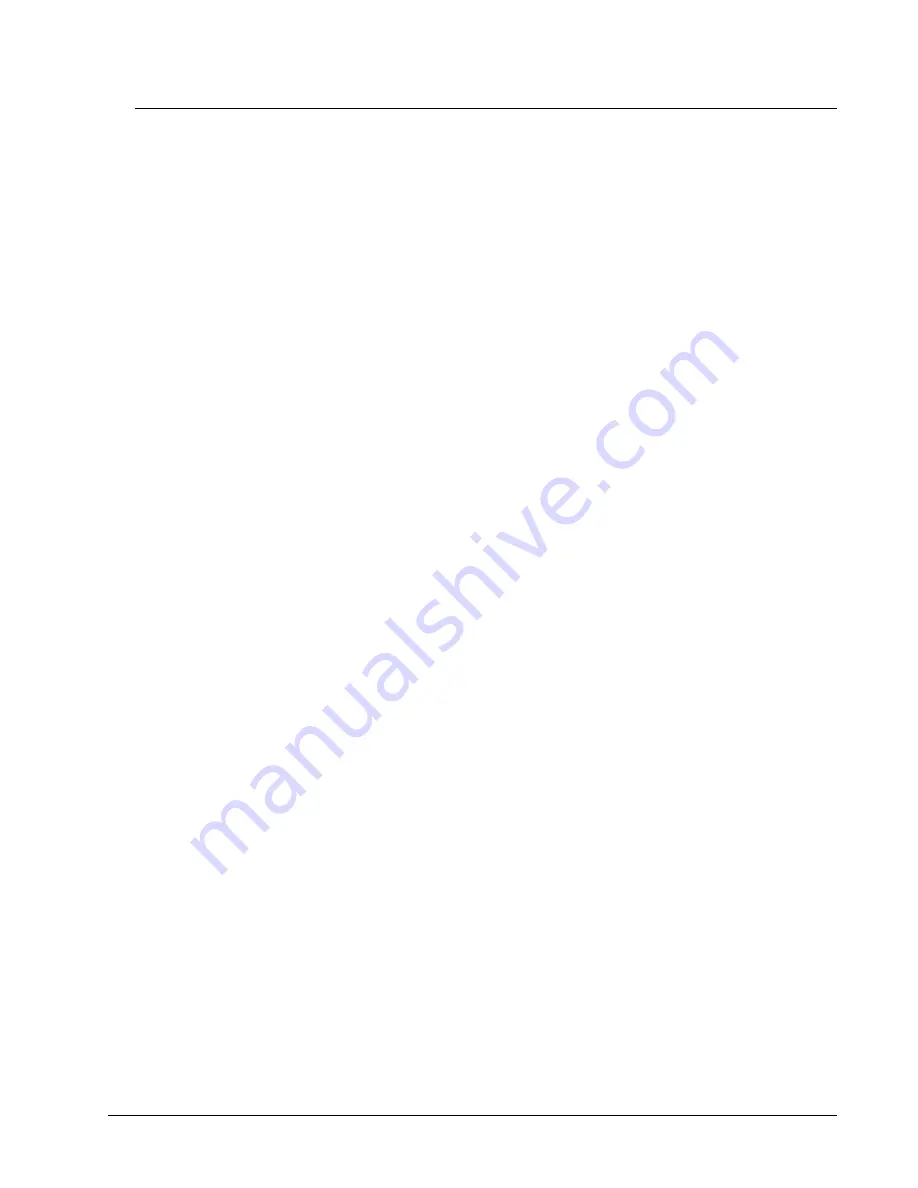
Operation
Brushless Motor Setup
Note
: If you purchased a Galil motor with the amplifier, it is ready for use. No additional setup is necessary.
To begin the setup of the brushless motor and amplifier, it is first necessary to have communications with the motion
controller. Refer to the user manual supplied with your controller for questions regarding controller
communications. It is also necessary to have the motor hardware connected and the amplifier powered to begin the
setup phase. After the encoders and motor leads are connected, the controller and amplifier need to be configured
correctly in software. Take all appropriate safety precautions. For example, set a small error limit (ER*=1000), a
low torque limit (TL*=3), and set off on Error to 1 for all axes (OE*=1). Review the command reference and
controller user manual for further details.
There are 3 settings for the amplifier gain: 0.4 A/V, 0.7 A/V, and 1.0 A/V corresponding to AG (amplifier gain) 0, 1
and 2. If the gain is set to 0.7 A/V, a torque limit of 3 (TLn=3) will allow the amplifier to output no more than 2.1
amps of current on the specified axis. The controller has been programmed to test whether the Hall commutation
order is correct. To test the commutation for the X axis, issue the BS command (BSX= n,m). The controller will
attempt to move the motor through one revolution. If the motor is unable to move, the controller will return
“unknown Hall transition”, check wiring, and execute BS again’. It may be necessary to issue more voltage to
create motion. The default for the BS command is BSn=0.25,1000 which will send 0.25 volts to the amplifier for 1
second. BSX=0.5,300 will issue 0.5 volts from the controller for 300 milliseconds. If the controller is able to move
the motor and the Hall transitions are not correct, the controller will alert the operator and recommend which motor
phases to change. For example, the controller might return “Wire A to Terminal B, Wire B to Terminal A.” If the
controller finds that the commutation order is correct, but the motor would run away due to positive feedback, the
controller will prompt the user to “Wire Phase B to C and C to B. Exchange Hall Sensors A and B…”. After
making any necessary changes to the motor phase wiring, confirm correct operation by reissuing the BS command.
Once the axis is wired correctly, the controller is ready to perform closed-loop motion.
Brushless Amplifier Software Setup
Select the amplifier gain that is appropriate for the motor. The amplifier gain command (AG) can be set to 0, 1, or 2
corresponding to 0.4, 0.7, and 1.0 A/V. In addition to the gain, peak and continuous torque limits can be set through
TK and TL respectively. The TK and TL values are entered in volts on an axis by axis basis. The peak limit will set
the maximum voltage that will be output from the controller to the amplifier. The continuous current will set what
the maximum average current is over a one second interval. The following figure captured with WSDK is indicative
of the operation of the continuous and peak operation. In this figure, the continuous limit was configured for 2 volts,
and the peak limit was configured for 10 volts.
Chopper Mode
The AMP-43040 can be put into what is called a “Chopper” mode. The chopper mode is in contrast to the normal
inverter mode in which the amplifier sends PWM power to the motor of +/-VS. In chopper mode, the amplifier
sends a 0 to +VS PWM to the motor when moving in the forward direction, and a 0 to –VS PWM to the motor when
moving in the negative direction.
This mode is useful when using low inductance motors because it reduces the losses due to switching voltages
across the motor windings. It is recommended to use chopper mode when using motors with 200-500
µ
H
inductance.
DMC-40x0 User Manual
A1 – AMP-430x0 (-D3040,-D3020)
•
238
Содержание DMC-4040
Страница 17: ...DMC 4080 Layout Figure 2 2 Outline of the of the DMC 4080 DMC 40x0 User Manual Chapter 2 Getting Started 8...
Страница 19: ...DMC 4040 Dimensions Figure 2 5 Dimensions of DMC 4040 DMC 40x0 User Manual Chapter 2 Getting Started 10...
Страница 20: ...DMC 4080 Dimensions Figure 2 6 Dimensions of DMC 4080 Chapter 2 Getting Started 11 DMC 40x0 User Manual...
Страница 54: ...Chapter 3 Connecting Hardware 45 DMC 40x0 User Manual...
Страница 55: ...DMC 40x0 User Manual Chapter 3 Connecting Hardware 46...
Страница 56: ...Chapter 3 Connecting Hardware 47 DMC 40x0 User Manual...
Страница 73: ...Figure 4 1 GalilTools DMC 40x0 User Manual Chapter 4 Software Tools and Communication 64...
Страница 185: ...THIS PAGE LEFT BLANK INTENTIONALLY DMC 40x0 User Manual Chapter 7 Application Programming 176...
Страница 205: ...THIS PAGE LEFT BLANK INTENTIONALLY DMC 40x0 User Manual Chapter 10 Theory of Operation 196...
Страница 220: ...Step 2 Remove ICM For DMC 4040 Proceed to Step 3 Configure Circuit Appendices 211 DMC 40x0 User Manual...
Страница 222: ...Step 2 Remove ICM s Appendices 213 DMC 40x0 User Manual...
Страница 232: ...DMC 4080 Steps 4 and 5 Step 4 Replace ICM s Appendices 223 DMC 40x0 User Manual...