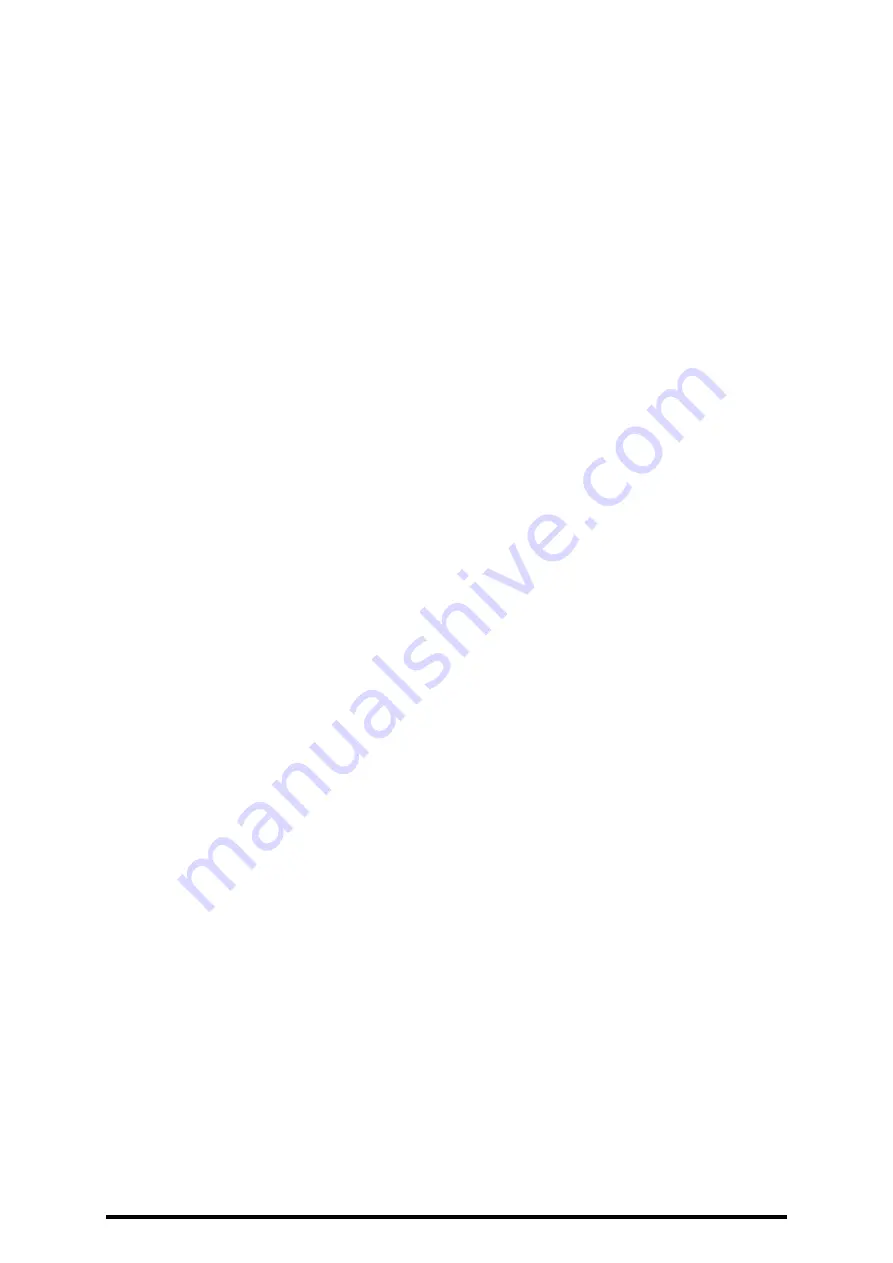
Page 46
FCO770 Users Guide Issue 1
•
This should only be used to remove repeatable leak offsets. A typical use is for
reducing cycle times, where a repeatable offset is present at the end of a test due to
not allowing a component long enough to fully stabilise. Offset is described in more
detail in a separate section later in this guide.
•
Note that if leak units are changed then the offset must be re-learnt.
TRACK FILTER
•
The filter value for the offset tracking system controls how the instrument responds to
variations in consecutive readings. Low filter values will allow the instrument to track
rapid changes in offset drift but will be affected by variations caused by leaks, large
filter values will only track slow changes in offset but will be affected less by leaks. A
value of five is suitable for most applications.
•
Set to zero to disable offset tracking.
•
The offset tracking system is described in a separate section later in this guide.
TEST O/P A-H
•
For each of up to eight outputs, define when the output is active.
•
Options:
o
OFF:
The output is not activated for this test.
o
ON
: The output is active for the whole of the test
o
STANDBY:
The output is only active whilst the test is selected but has not been
started. The output is deactivated when the test is started.
o
TEST:
The output is only active once the test is started.
FEEDBACK A-H
•
Define which feedback inputs are required before the test is allowed to run. The
feedback signals will typically be used to indicate correct positioning of the jig.
•
Each of up to eight possible inputs may be selected on (1) or off (0), e.g. to wait for
inputs A and C the setting will be “10100000”.
•
Feedback is checked after the test outputs A-H have been activated, but before the
vent output.
•
Note that the feedback inputs must be configured in the I/O Configuration menu.
FEEDBACK TIMEOUT
•
The default feedback timeout is set to 0.0 which disables the timeout function. The
instrument will display “Awaiting Feedback” until the correct feedback is applied or
the test is reset.
•
When the feedback inputs are not used for jigging they may be used to check signals
from test components. If the correct feedback is not supplied within the feedback
timeout period then the test ends with a FEEDBACK FAIL result.
EXTERNAL FAIL
•
Allows an external signal, for example a pressure switch, to be monitored during the
test. An External Fail result is given if the signal is not in the expected state during the
stabilisation period.
•
Note that the input function must be defined in the i/o configuration menu.
•
Options:
o
NO:
External fail is not used for this test.
o
ON:
The input is expected to be active during the stabilisation time.
Содержание FCO770
Страница 2: ......